In this article, we will give you an overview of the Phoenix Contact MINT AI-Enhanced Energy Management.
We will also discuss the hardware and software required to operate the MINT.
Finally, we’ll demonstrate how easily the associated PLCnext Engineer program and associated software are parameterized to suit client Energy Management needs.
What is MINT?
Let’s begin with the question: What is MINT?
MINT is a portfolio of energy management solutions including AI-based software and self-learning technology by Phoenix Contact.
MINT is a self-learning and self-managing energy management solution developed by Phoenix Contact that connects and coordinates all your energy sources and consumers and continuously maintains the balance of the electricity grid.
PLCnext Technology Overview
PLCnext Technology is at the heart of the MINT.
For those who don't know, PLCnext Technology is an open control platform developed by Phoenix Contact combining traditional PLC functionality with modern software technology, open standards, ecosystem collaboration, and IT security as certified and accredited by IEC 62443-4-1 and 62443-4-2.
The programming software PLCnext Engineer supports the 5 traditional IEC 61131-3 languages and easily integrates programs created in higher-level languages such as C++, MATLAB, and more.
To enable integration with IoT devices and cloud services, PLCnext Technology supports several communication protocols and standards, including OPC UA, MQTT, RESTful APIs, and others.
Practical Application Scenario
Ok… before we get into the details of the Phoenix Contact MINT, let’s look at a scenario where Energy Management is key to the success of a commercial company.
Your company has decided to provide several employees with Electric Vehicles, or EVs. These EVs can be charged at any of the ten units of the central Charging Station located just outside the main office building.
Considering this scenario, a few questions come to mind…
- Can all the EVs be charged at the same time and the same charge rate?
- Can solar power be incorporated?
- What will be the impact on our environment?
- And how much is this going to cost?
MINT in Action
Let’s look at how MINT can operate and control the Charging Station.
An employee drives up and connects his EV to a charging station. This employee does not need to charge this vehicle immediately to full charge because he’s in the office all day.
A second employee arrives and uses a phone app to instruct the station to charge his EV to 80% by 2 PM.
A third employee arrives and uses the same phone app to instruct the station to charge her EV to 70% by noon as she has a morning meeting scheduled at that time.
Three more employees arrive but will be in the office all day.
So, some employee EVs can sit and charge all day, while others need to be on the road to a specific destination at different times of the day.
Charging all these EVs simultaneously at a maximum rate can cause serious issues or even an electrical supply fuse failure.
MINT can easily shift the charging rate of each vehicle based on the assessed needs and the electrical system limits.
To minimize cost and reduce the grid power consumption we’ll add solar power to our energy supply. This allows the charging to be shifted to match the needs according to the charging profile of the solar power generation.
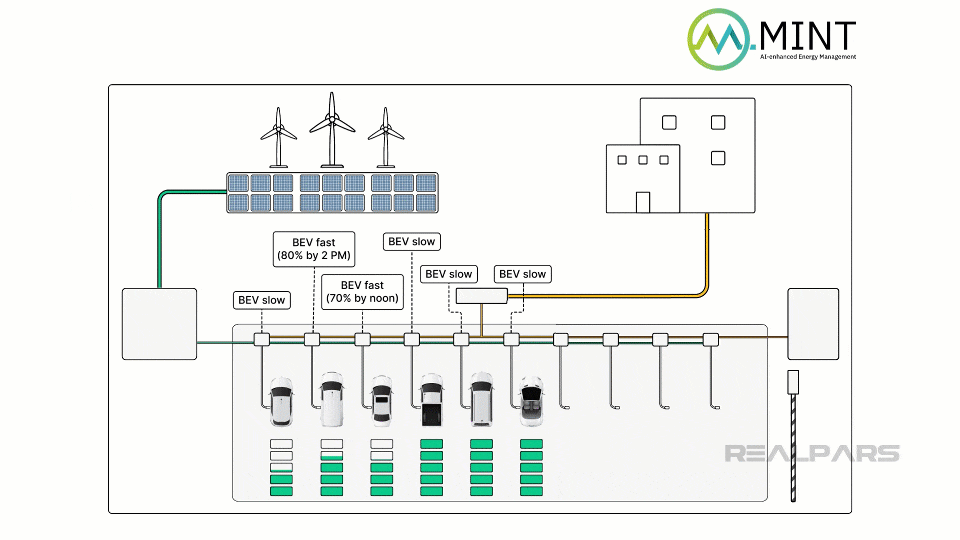
That’s good as long as the sun is shining and the solar panels are contributing.
This scenario is an oversimplification, but we think it paints a good picture of what MINT can do.
PLCnext Engineer Basic Application
System Setup and Configuration
As we said earlier, PLCnext Technology is at the heart of MINT. The system's brain is the PLCnext Engineer programming software and the muscle is the AXC F 2152 controller.
We don’t want to give you the impression that the AXC F 2152 is the only MINT-capable controller because other controllers can also be used.
The AXC F 2152 controller runs with an EMS app, a ready-to-use solution providing load management functions for system integrator programming. This solution allows you to operate your charging park, building, or property safely, reliably, and economically.
As with most PLCnext apps, the EMS.Core PLCnext App can easily be installed via the web-based management of the PLCnext AXC F 2152 controller.
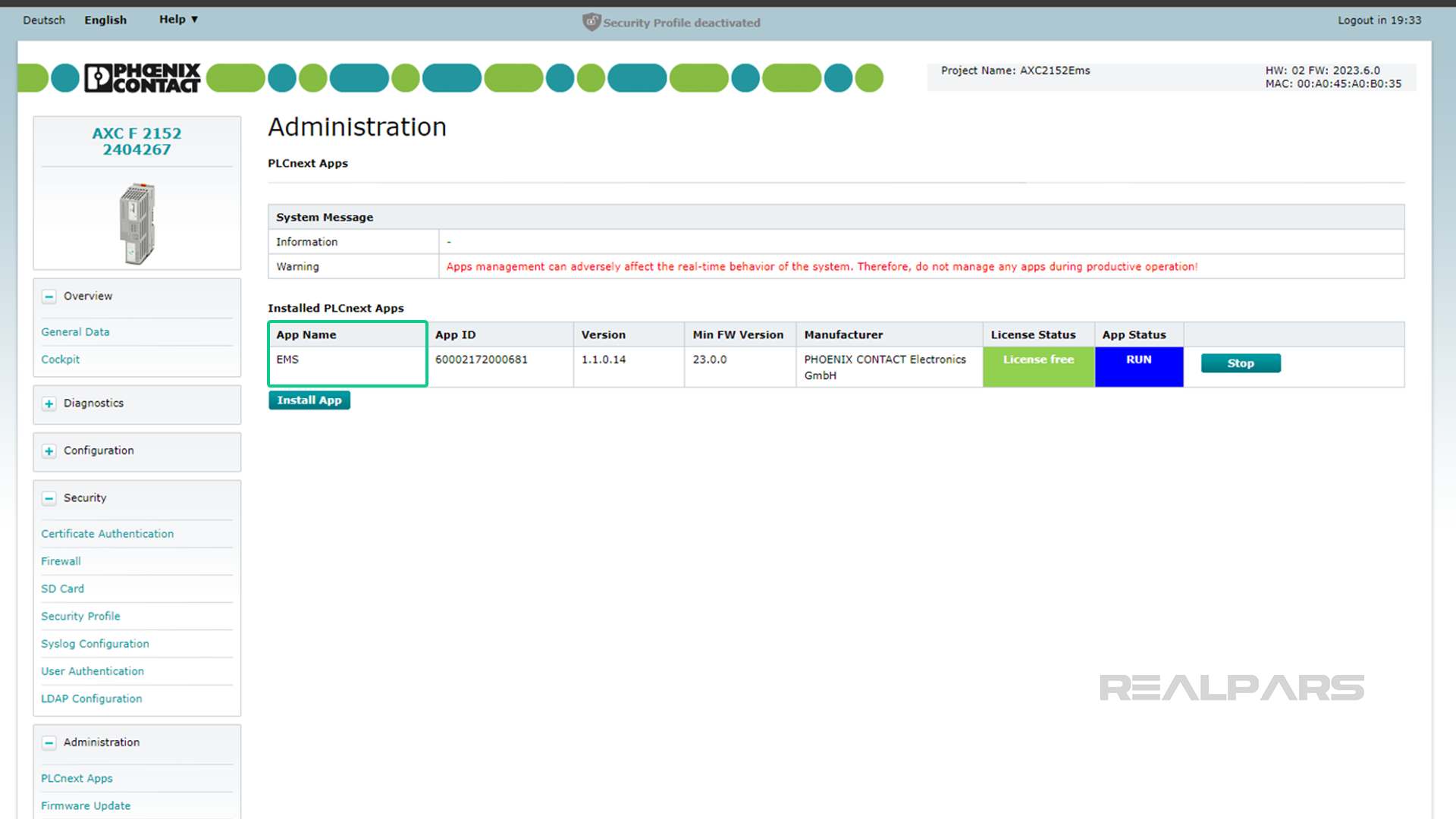
The EMS.Core app allows the implementation of individual energy management systems (EMS) for the manufacturer-independent control of several loads and generators.
Project Development and GDS Integration
Let’s have a look at the PLCnext Engineer Basic Application.
A facility structure definition is required to enable faultless load management. This can be done via an XML configuration file.
As a quick example, we will model five AC-Charging points, one photovoltaic system and a building as not controllable load.
1<EEMS>
2<loadCircuit>
3<id>Loadmanagement</id>
4<name>EEMS</name>
5<description>Here we can add a text to describe the circuit</description>
6<!-- The system maximal current for each phase -->
7<fuse>100</fuse>
8<!-- You can configure a reserve that will be substract from the fuse-->
9<reserve>0</reserve>
10<!-- defining our not controllable loads -->
11<consumers>
12<consumer>
13<id>Building_01</id>
14<name>Building</name>
15<description>Example Factory Grid</description>
16<prio>MEDIUM</prio>
17</consumer>
18</consumers>
19<!-- defining our producers -->
20<producers>
21<producer>
22<id>Photovoltaic_01</id>
23<name>Producer1</name>
24<description>Example Photovoltaik</description>
25<prio>MEDIUM</prio>
26<type>Photovoltaik</type>
27</producer>
28</producers>
29<!-- defining our controllable loads like charging points -->
30<controllableConsumers>
31<controllableConsumer>
32<!-- The ID must be unique and is required to access the charging point data inside the PLCnext engineer -->
33<id>CPoint_01</id>
34<name>ControllableConsumer1</name>
35<description>Charging Point 01</description>
36<prio>MEDIUM</prio>
37<!-- minimal required charging current -->
38<minLoad>6</minLoad>
39<!-- maximal possible cahrging current -->
40<maxLoad>32</maxLoad>
41</controllableConsumer>
42<controllableConsumer>
43<id>CPoint_02</id>
44<name>ControllableConsumer2</name>
45<description>Charging Point 02</description>
46<prio>MEDIUM</prio>
47<minLoad>6</minLoad>
48<maxLoad>32</maxLoad>
49</controllableConsumer>
50<controllableConsumer>
51<id>CPoint_03</id>
52<name>ControllableConsumer3</name>
53<description>Charging Point 03</description>
54<prio>MEDIUM</prio>
55<minLoad>6</minLoad>
56<maxLoad>32</maxLoad>
57</controllableConsumer>
58<controllableConsumer>
59<id>CPoint_04</id>
60<name>ControllableConsumer4</name>
61<description>Charging Point 04</description>
62<prio>MEDIUM</prio>
63<minLoad>6</minLoad>
64<maxLoad>32</maxLoad>
65</controllableConsumer>
66<controllableConsumer>
67<id>CPoint_05</id>
68<name>ControllableConsumer5</name>
69<description>Charging Point 05</description>
70<prio>MEDIUM</prio>
71<minLoad>6</minLoad>
72<maxLoad>32</maxLoad>
73</controllableConsumer>
74</controllableConsumers>
75</loadCircuit>
76</EEMS>
Everything is part of the same load circuit. As we mentioned earlier, this data must be added to the XML configuration file stored at a specific location on the PLCnext device.
After structuring the system, a new PLCnext Engineer project can be created. The example uses the PLCnext Engineer programming software and the target device is an AXC F 2152. First, we have to include the EMS.Runtime software library.
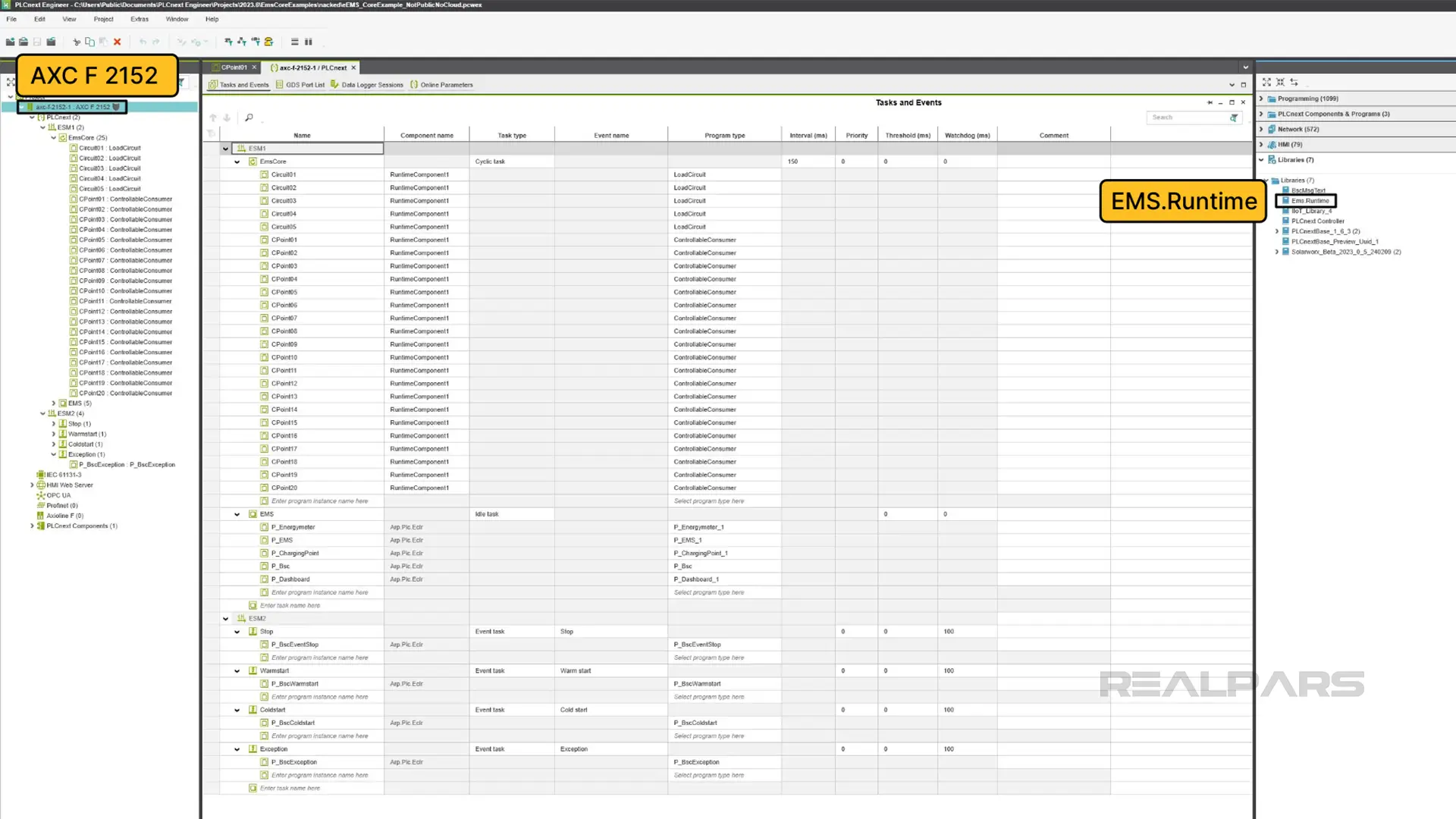
Now it is possible to access the various type definitions. For each entity in the project, the program instance must be added. The name of each entity in the PLCnext Engineer must be the same value as indicated in the XML file under the ID tag.
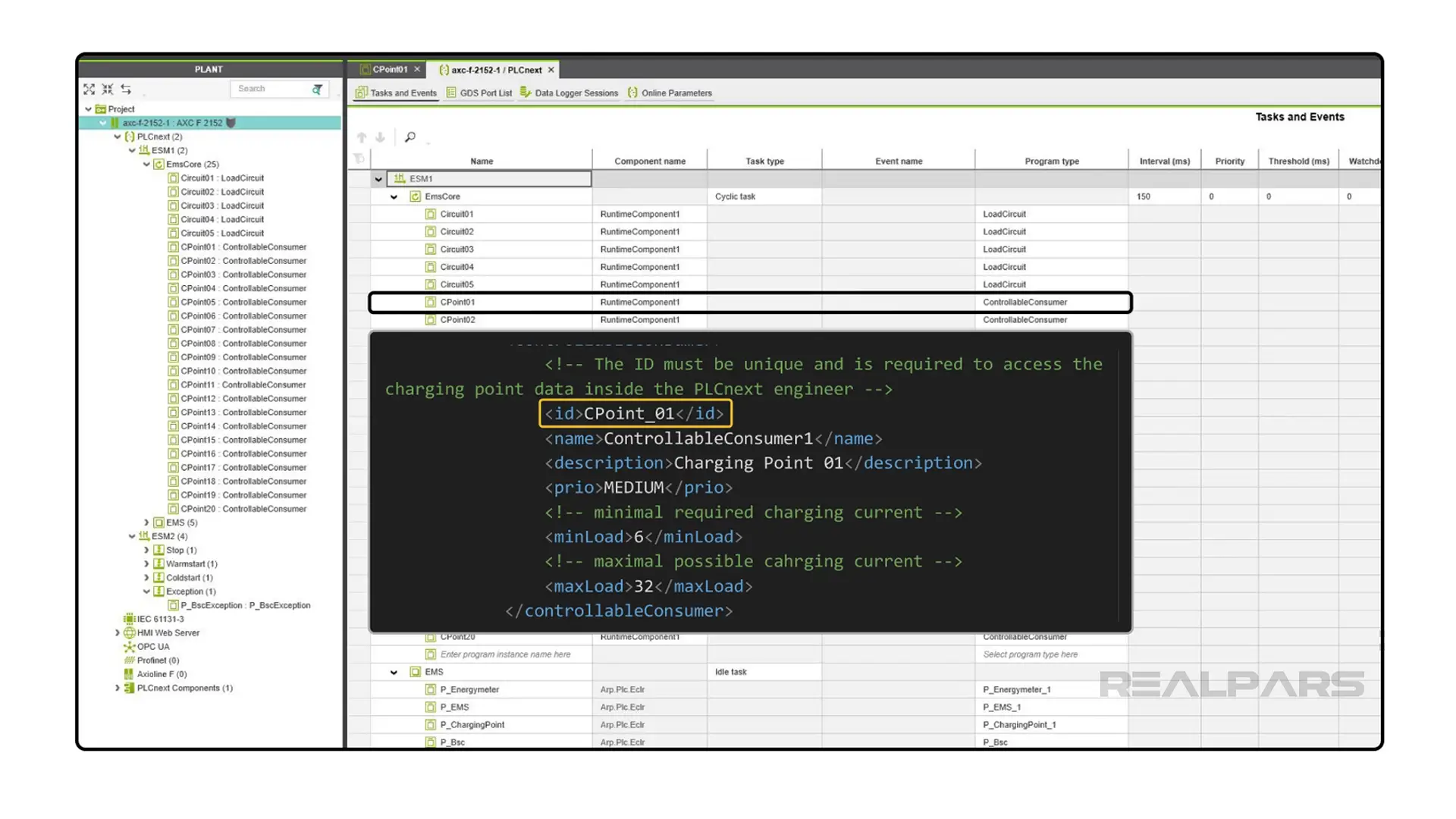
Here’s where we take advantage of the Global Data Space or GDS feature of PLCnext Technology.
GDS allows different software components, tasks, and devices to exchange data seamlessly within a PLCnext Engineer application.
GDS Ports provide a means for accessing and manipulating data within the Global Data Space enabling data exchange between different software modules or devices connected to the PLCnext controller.
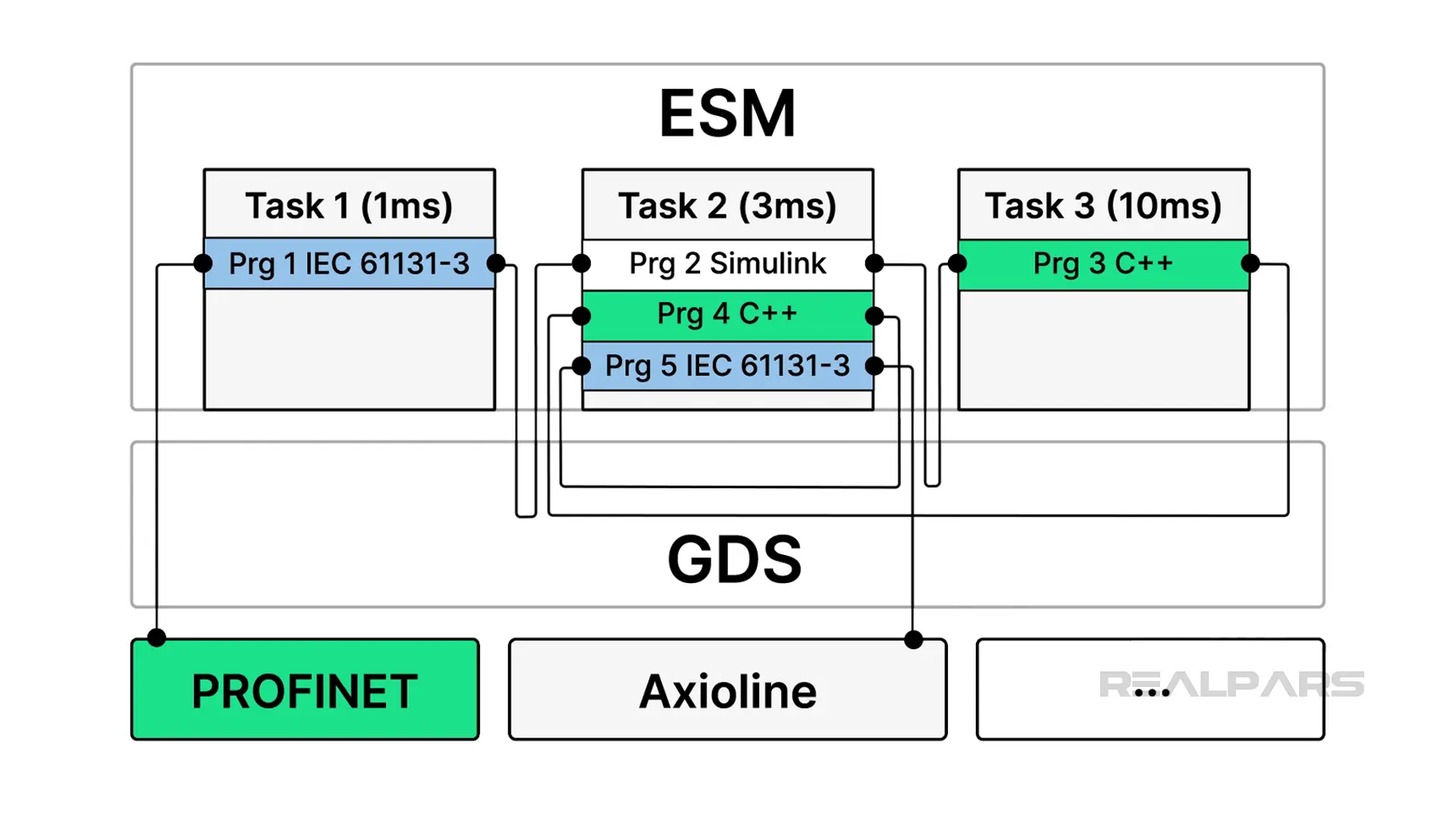
In our example, the facility structure definition XML file is stored inside a GDS Port for PLCnext Engineer access.
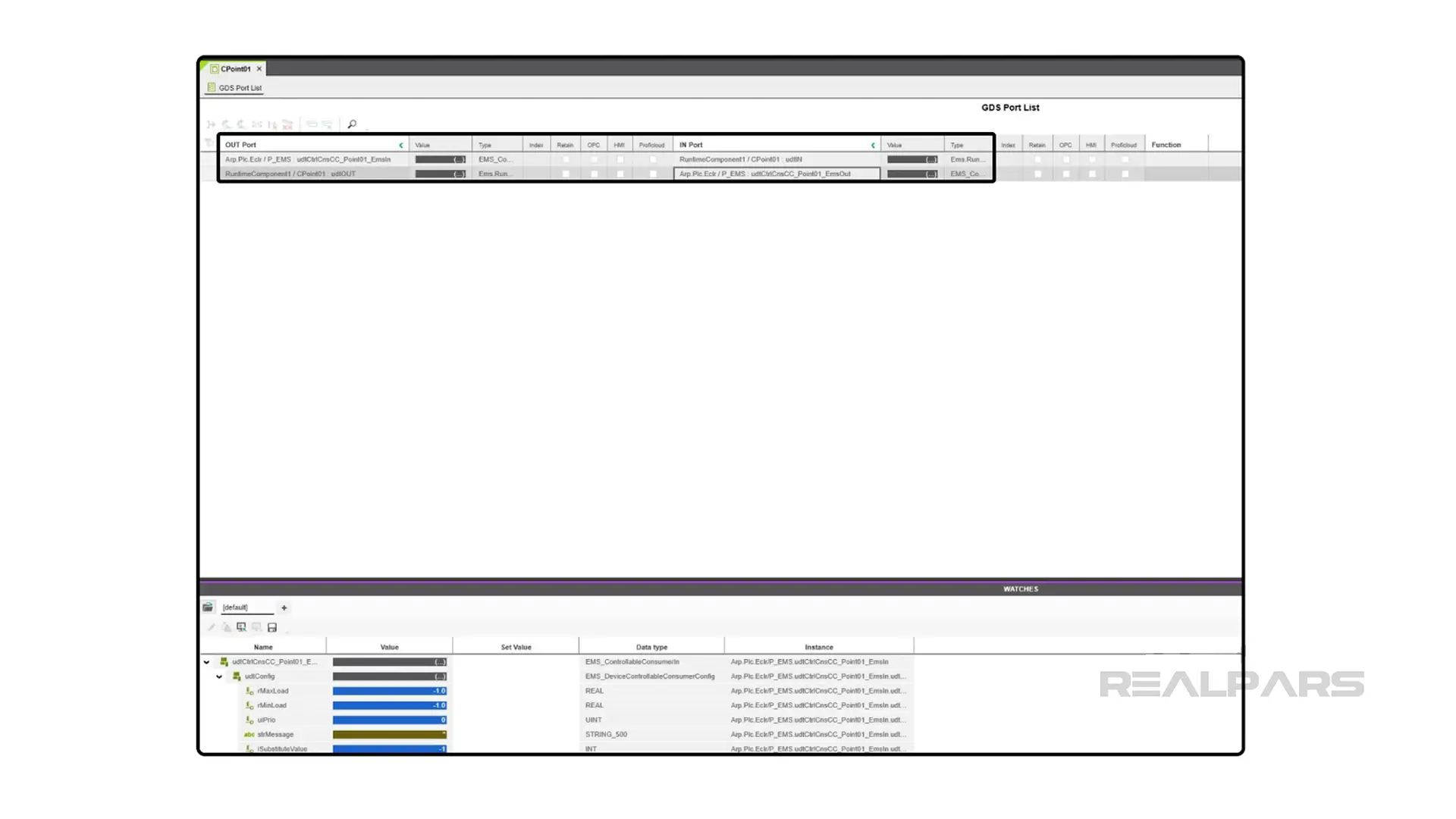
Next, the project is downloaded and run on the AXC F 2152 controller. After restarting the EMS App the parameters from the XML file are stored inside the GDS ports of the program instances.
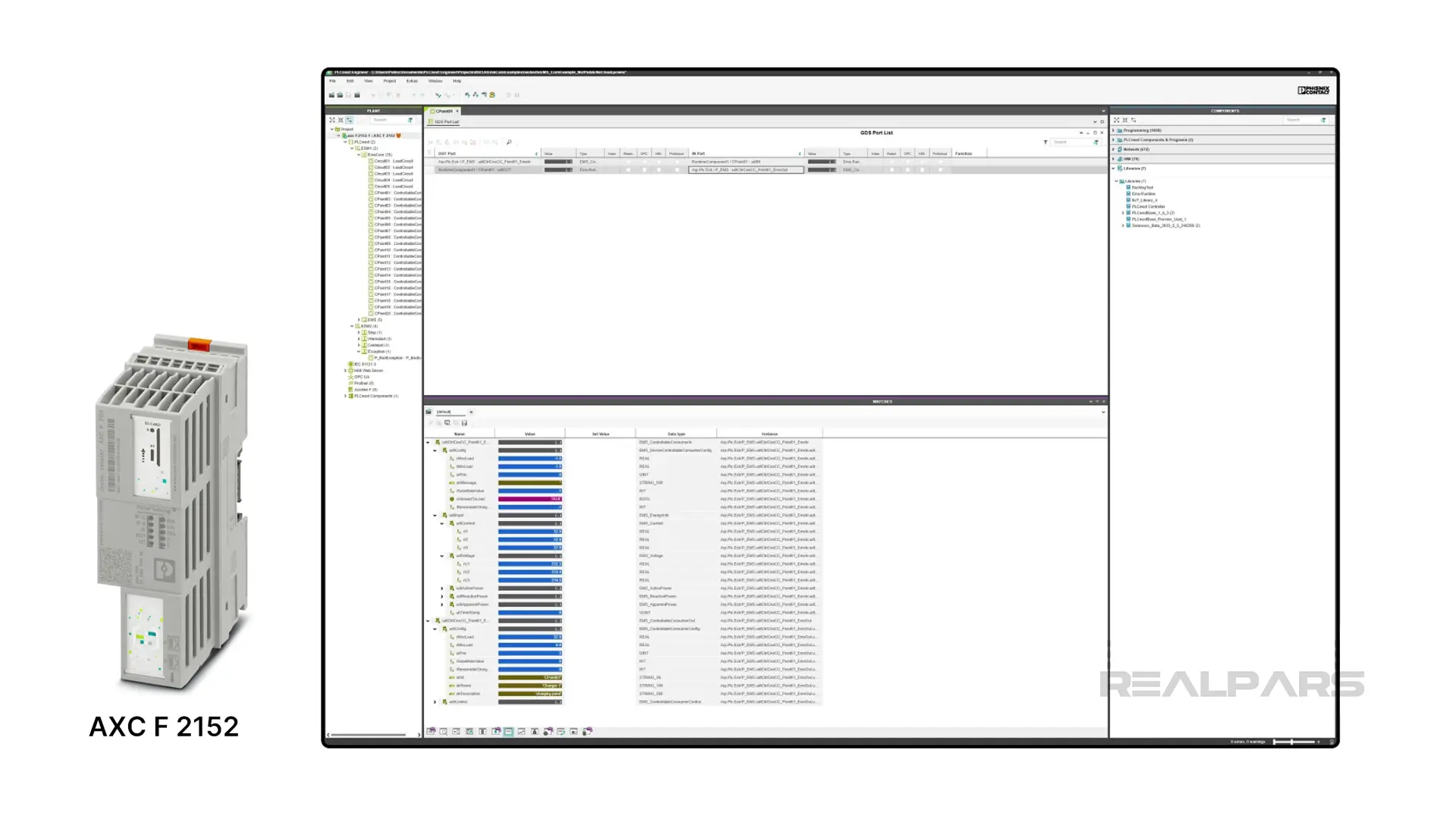
Advanced Features and Training
In addition, the Solarworx library is used, as it contains manufacturer-independent drivers for energy-measuring devices for both PV inverters and residential wall-mounted charging stations.
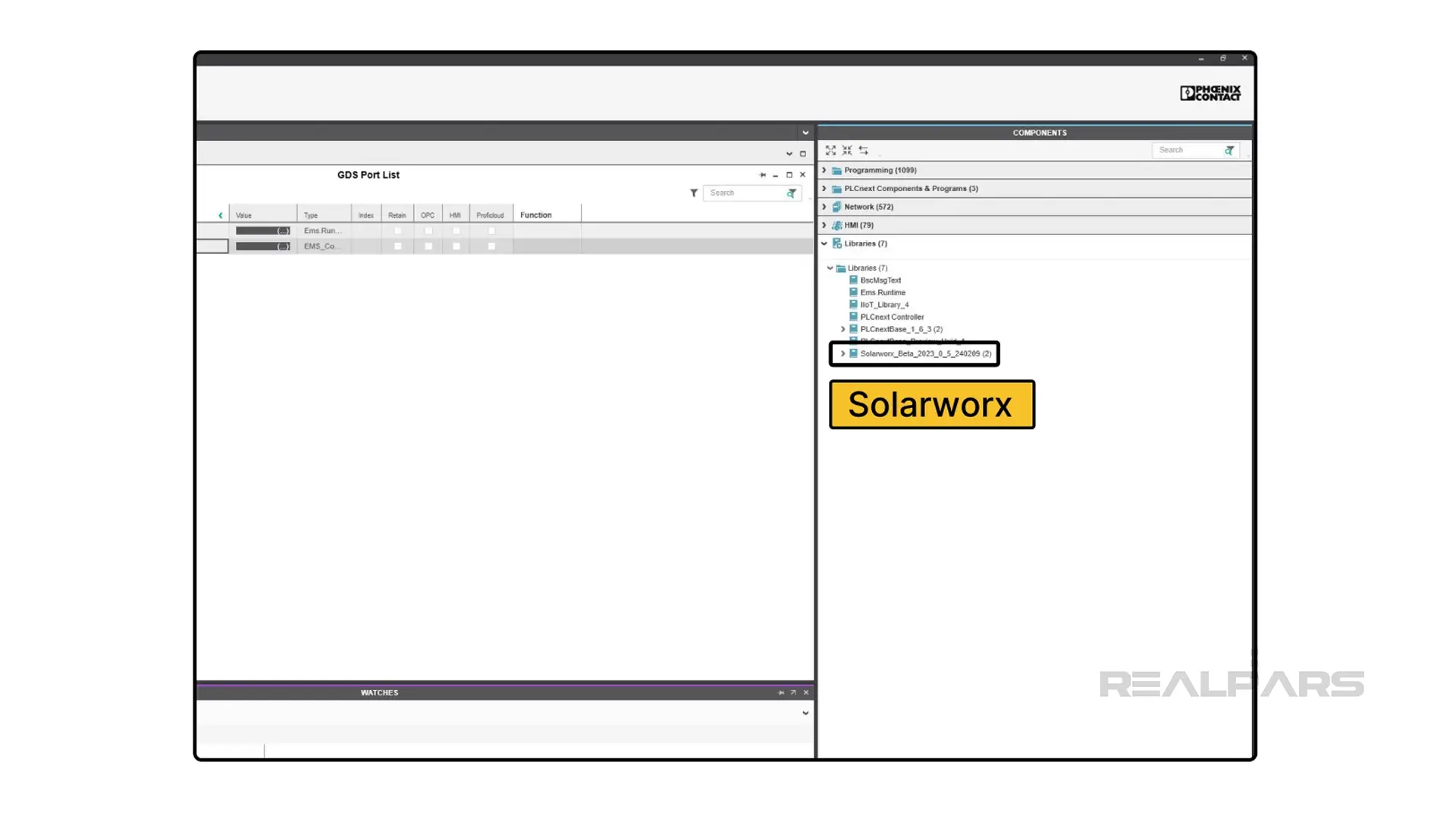
In addition to what we’ve shown you, the MINT EMS can provide on-premise Smart control of Energy flows providing many more basic features such as:
- Dynamic Load Management
- Manufacturer-independent interfaces
- Charging/discharging management of storage devices
- Optimized use of existing infrastructure
- Support for any number of assets
Looking at the big picture, PLCnext Engineer together with the Energy Management and Solarworx apps manages the EV Chargers based on information from the consumer data provided in the Facility Description XML File.
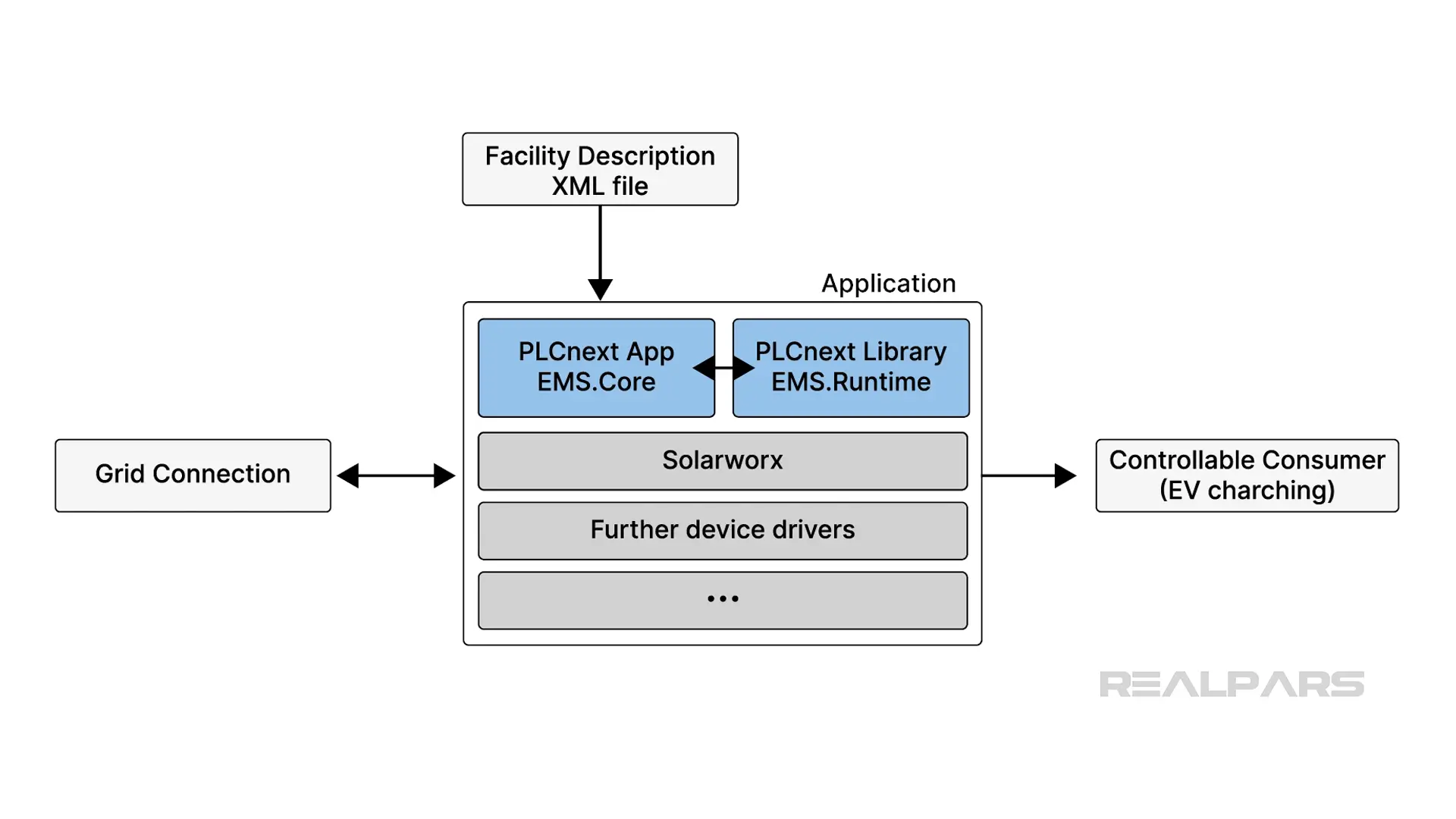
But, if you want, MINT can do even more.
Remember earlier we talked about how great solar power is, as long as the sun is shining.
The MINT incorporates AI via a PLCnext App to best utilize the solar potential. This AI functionality also plans and executes EV Charging Station energy shifting based on prediction, generation, consumption, and EV charging behavior.
The EMS.Cloud.Optimizer is a powerful tool providing features such as:
- Peak Shaving where the system learns load curves to adjust individual station energy flow.
- Optimized Charging to adjust charging accordingly based on weather forecasts.
- Optimized Charging to adjust charging accordingly based on the EV charging behavior.
- Dynamic pricing based on the prediction of spot market prices, controllable consumers, and optimized charging processes.
- Battery storage and discharge optimization during high price times
System integrators can take advantage of the built-in HMI feature of PLCnext engineer to develop their own customized HMI or use an HMI template provided.
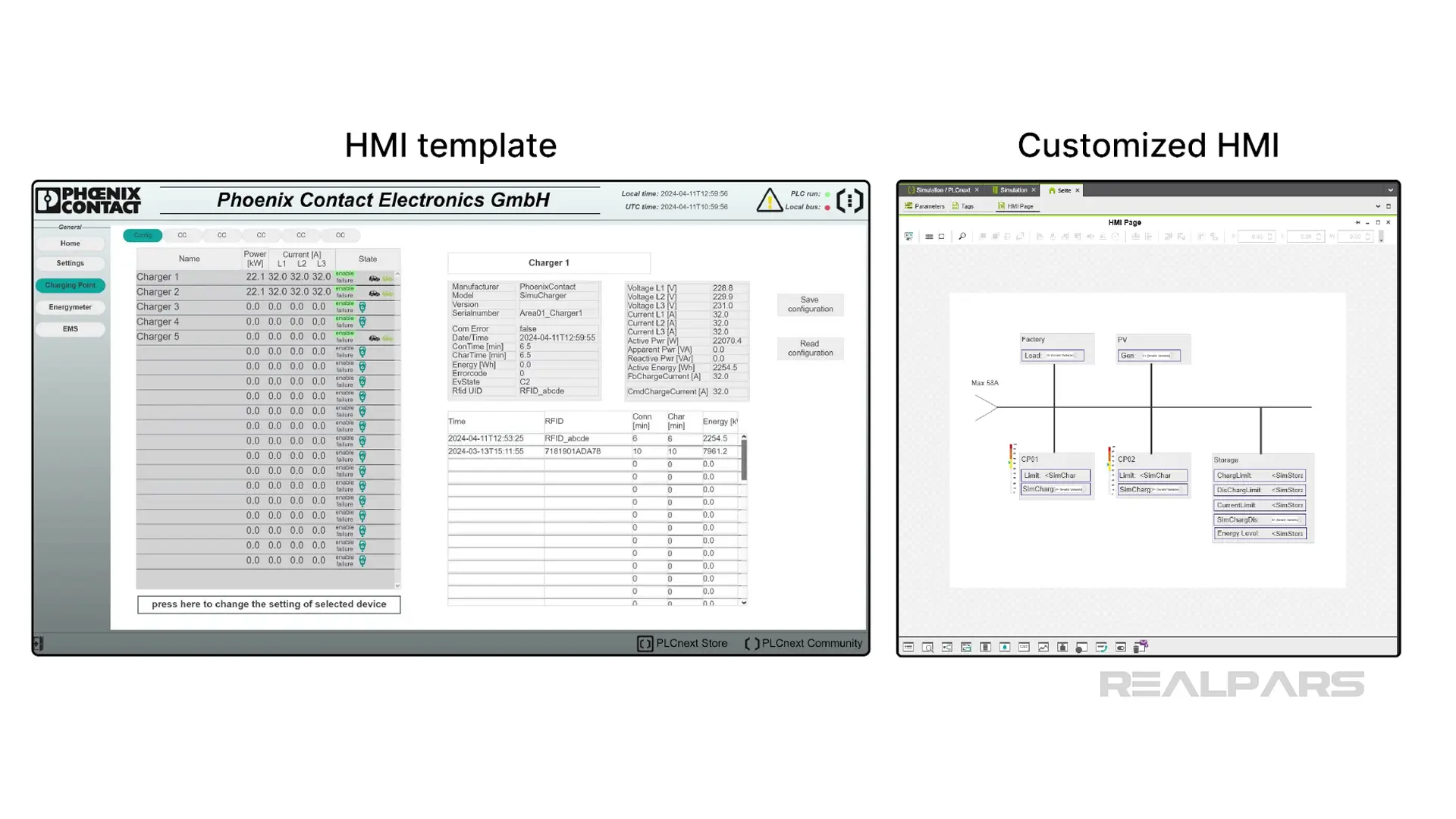
Using the EV Charging Station scenario, we’ve illustrated just a small part of what MINT can do.
Conclusion
So, as the person or System Integrator tasked with setting the parameters of MINT, what do you need to know?
First of all, you’ll need a solid background in PLCnext Technology. In particular, you should know your way around the PLCnext Engineer programming software. While actual higher-level language programming ability is not required, a good grasp of the GDS is essential.
If necessary, you should also know how to set up and navigate the built-in PLCnext Engineer HMI feature.
RealPars offers courses that can meet your needs. The courses are:
- PLCnext Ladder Logic Programming for Beginners
- PLCnext eHMI Design: Create & Optimize Interfaces, and
- Using C++ Projects with PLCnext Technology
These courses have been developed in partnership with Phoenix Contact. At the end of each course, you will receive a certificate of completion from Phoenix Contact.
Also, if you want to learn more about MINT, keep an eye out for our upcoming courses on this topic, which will be launched soon.