In this article, we’re going to talk about a very common instrument found in the industry today, the Pressure Gauge.
It would be difficult to walk through any industrial or food processing plant or manufacturing facility without seeing a pressure gauge of some type.
What is a pressure gauge?
A pressure gauge is an instrument for measuring fluid intensity in a pressure-powered machine. This fluid intensity is specified by the force that the fluid would exert on a specific unit area.
Typical pressure gauge intensity measurement units are pounds per square inch (psi), or newtons per square meter called the pascal.
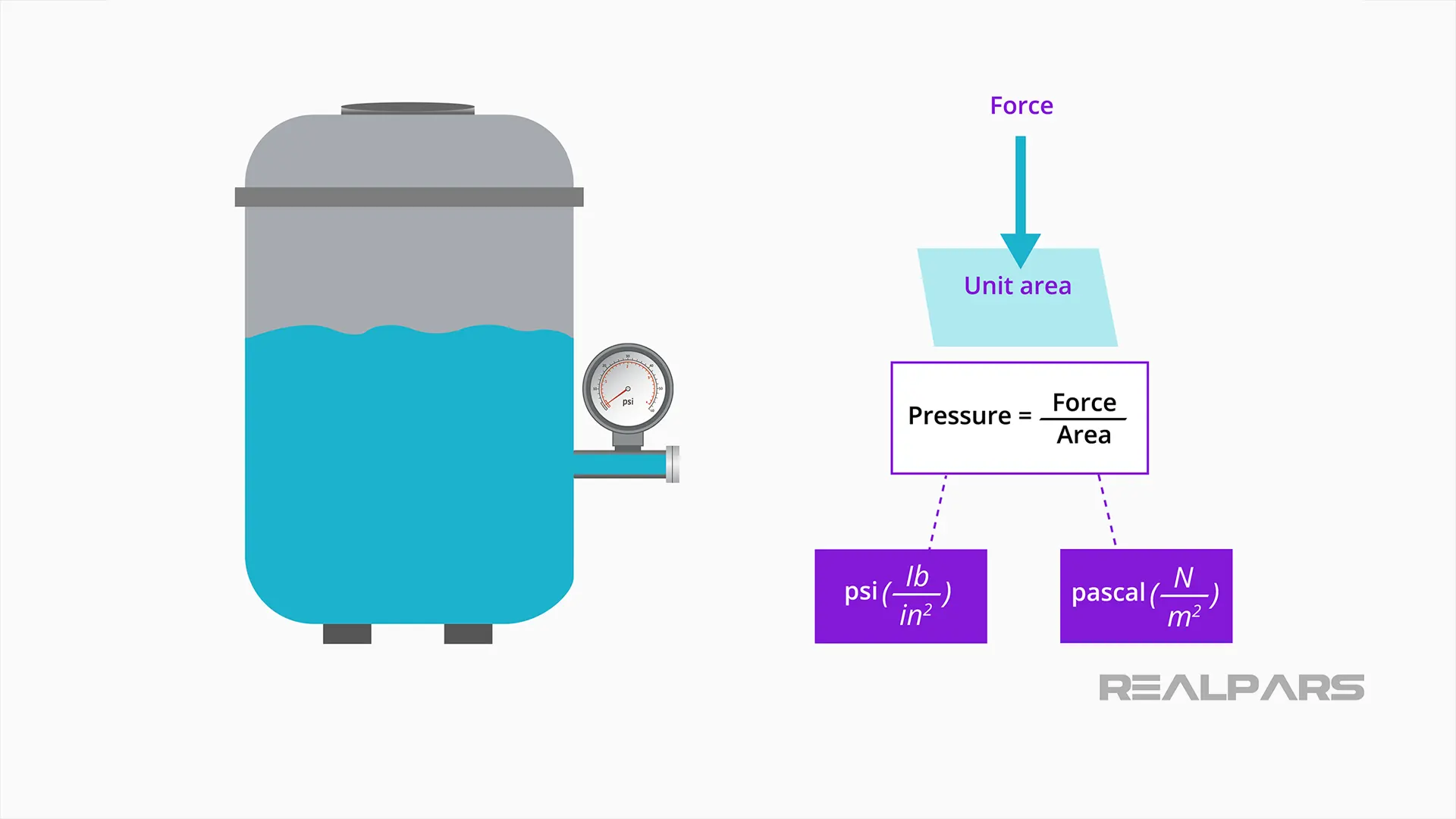
Types of pressure gauges
Categorizing Pressure gauges has become more challenging with the introduction of electronic transducers and devices.
Historically, pressure gauges were mechanical devices with analog scales. Today we have pressure gauges with pressure-sensing transducers operating electronic digital readouts.
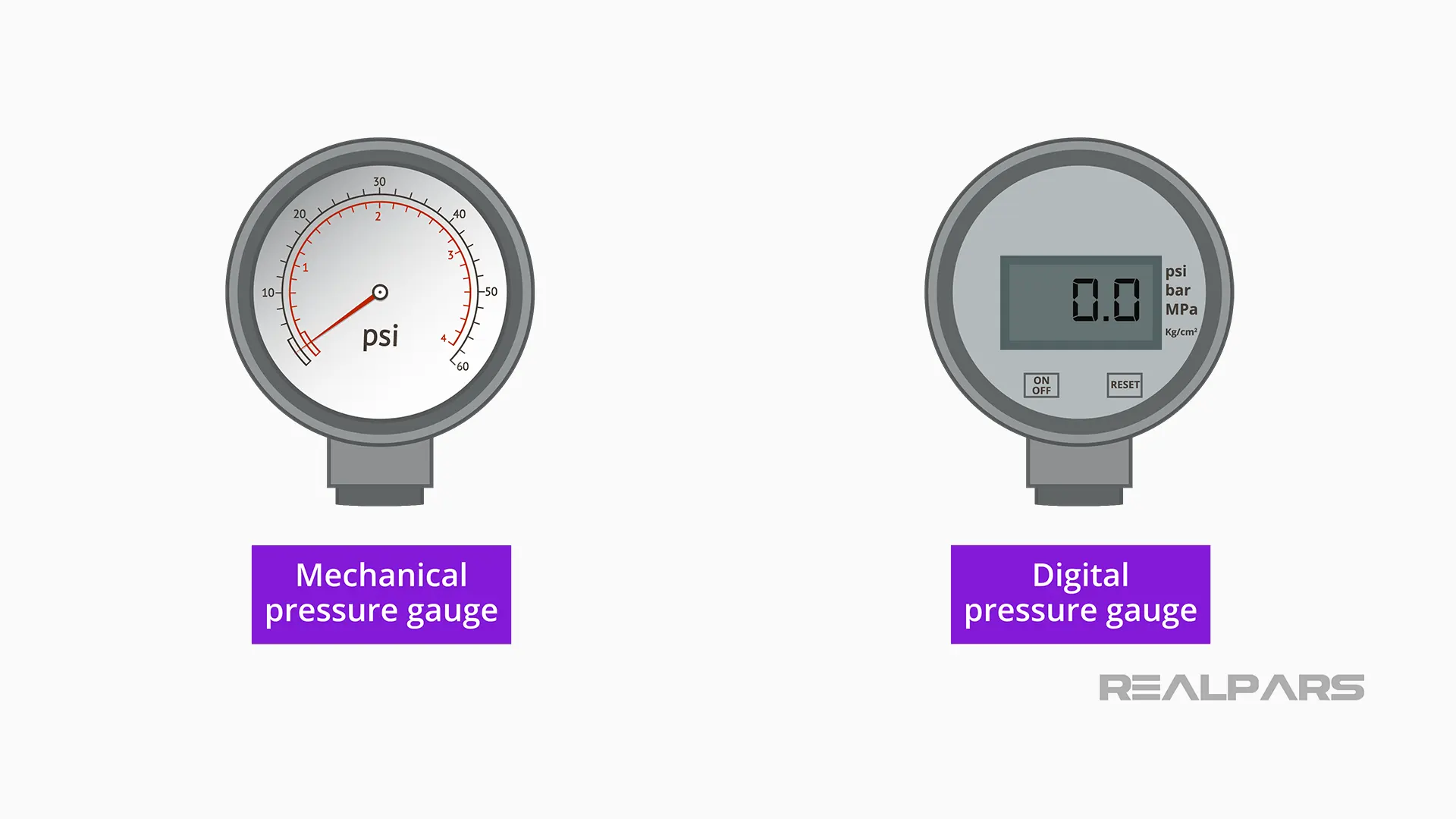
Mechanical pressure gauges
There are many types of mechanical pressure gauges. Three of the most common types are:
1) Diaphragm
2) Bellows
3) Bourdon Tube
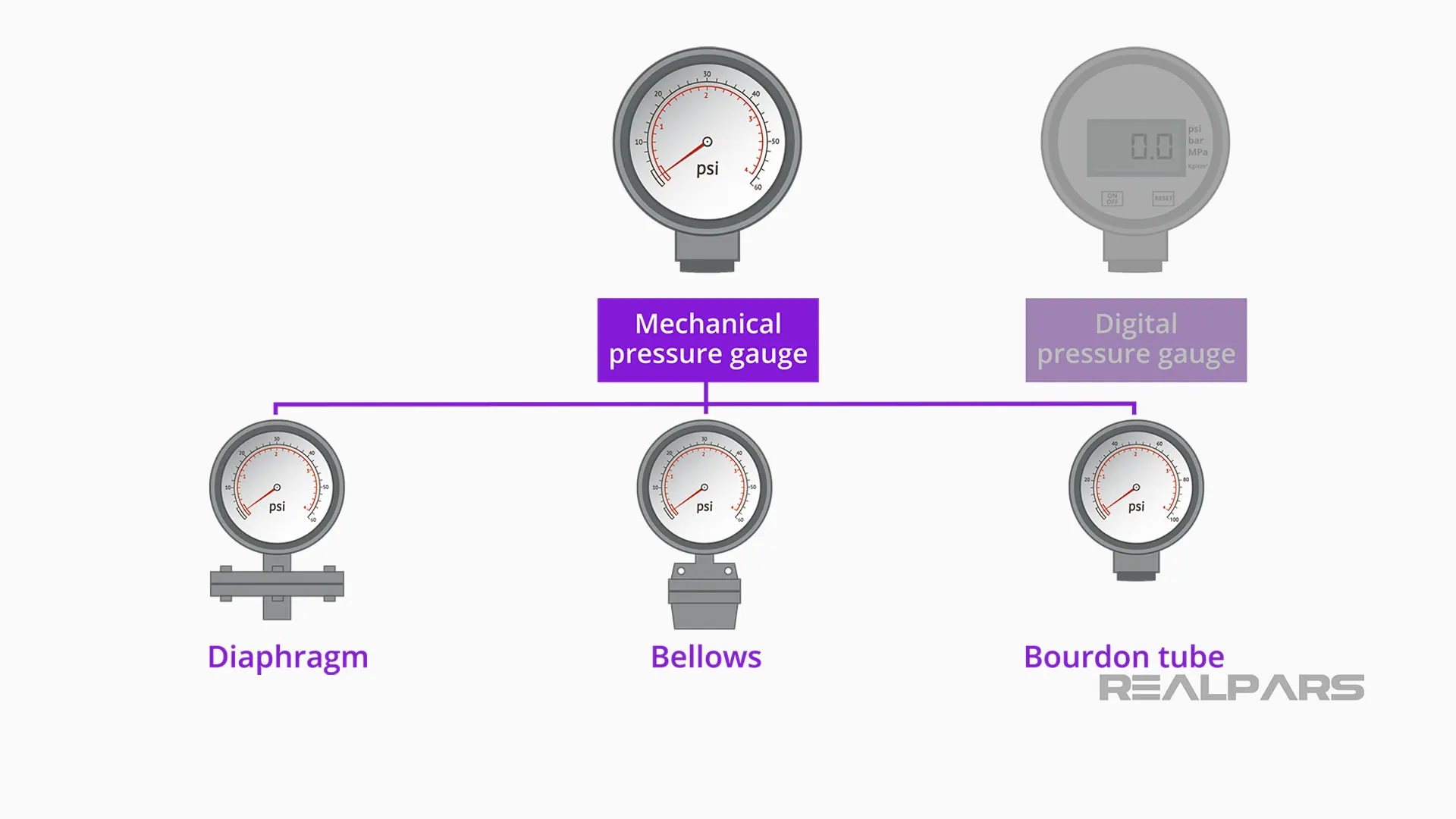
1) Diaphragm
A diaphragm pressure gauge uses the deflection of a flexible thin membrane called the diaphragm to measure the pressure of the fluid in a system.
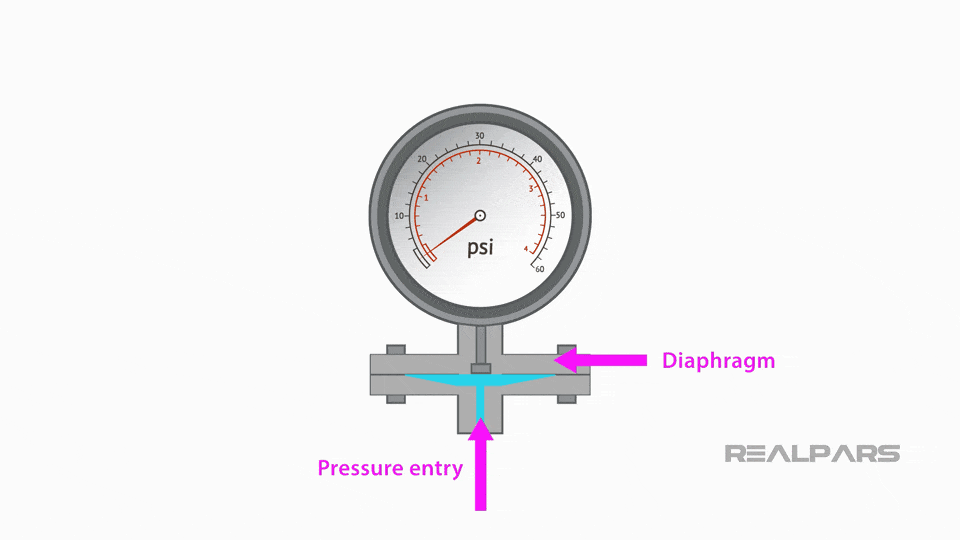
2) Bellows
A bellows is a corrugated expandable device made up of corrugations or ribs called convolutions.
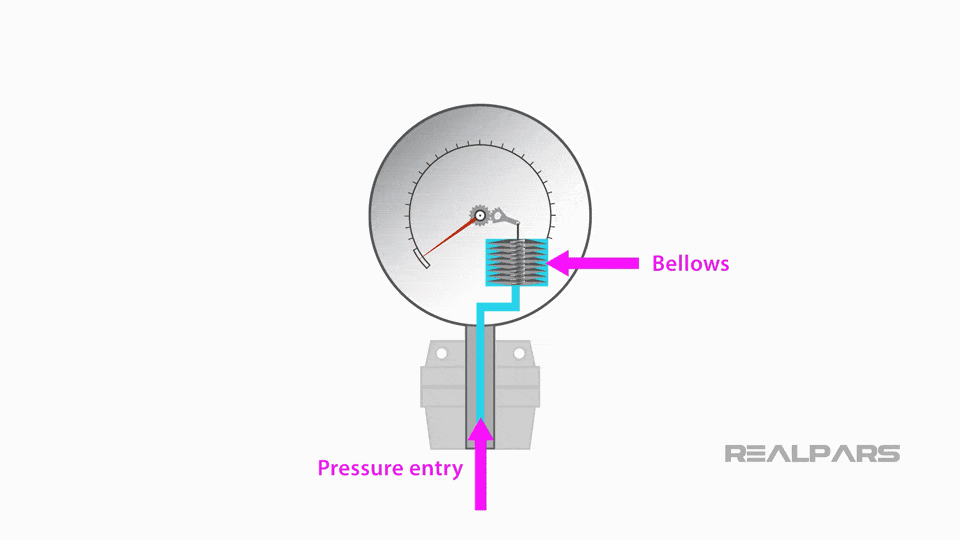
The bellows are usually brass or stainless steel and very sensitive. Pressure is supplied to the bellows causing it to expand which in turn, moves a pointer.
3) Bourdon tube
Of those three mechanical pressure gauges, by far the most common is the Bourdon Tube type. So, let’s have a closer look.
Bourdon tube – C type
The most common type of Bourdon tube gauge is the C type in which the tube is shaped to resemble the letter C. Notice the cross-sectional shape of the tube. The tube is opened at one end and sealed at the other.
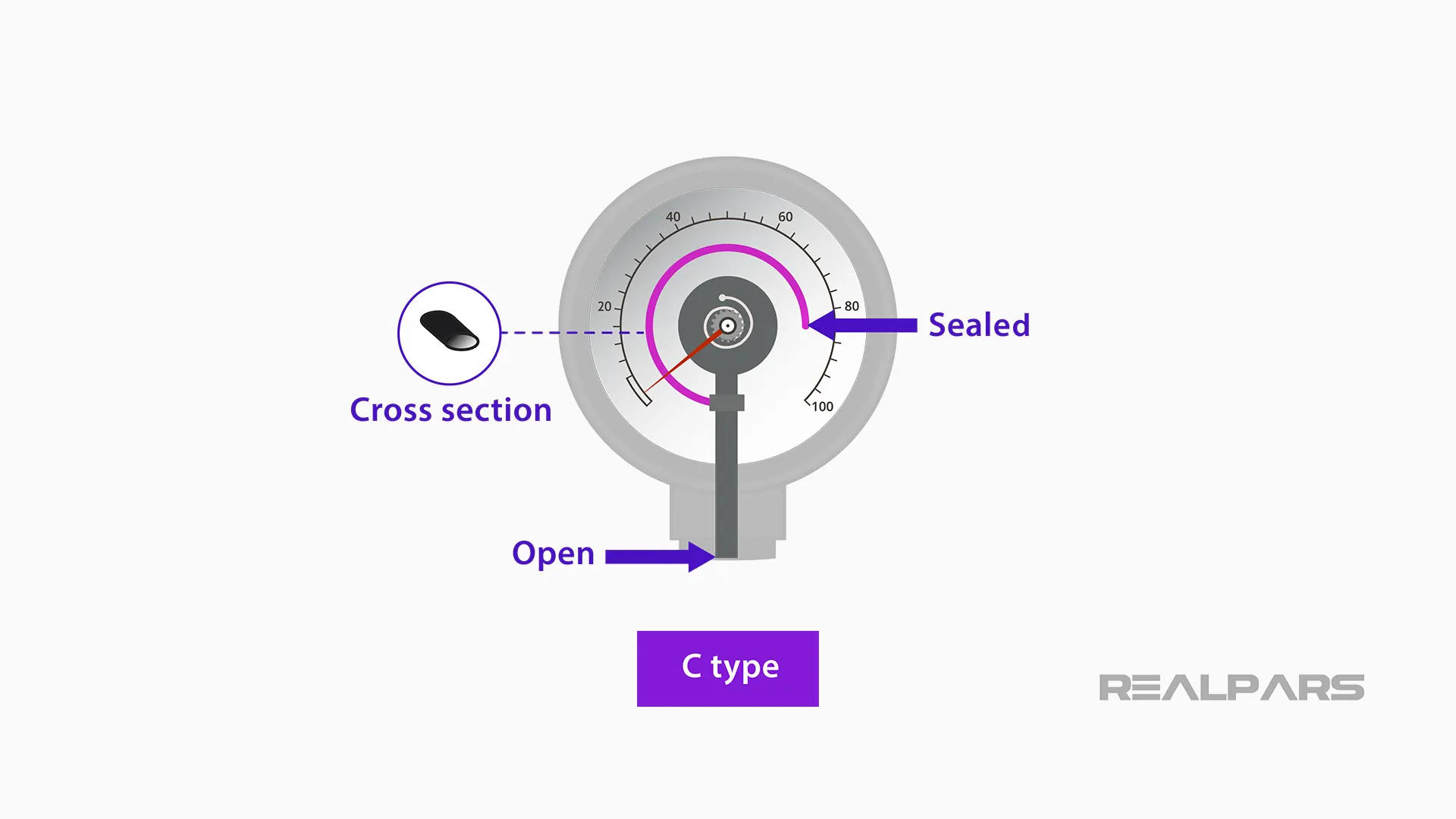
A change in pressure causes a deflection in the tube that is proportional to the applied pressure.
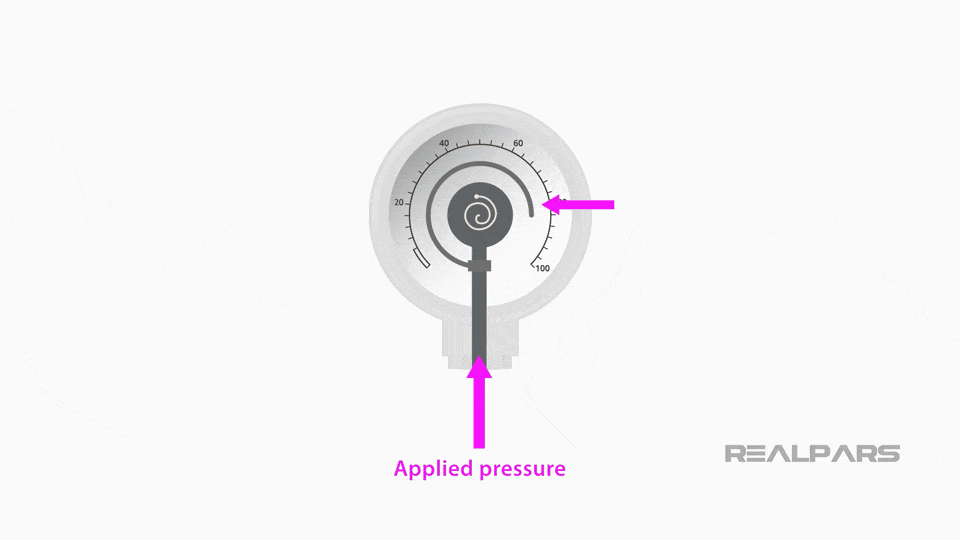
The actual movement of the tube is converted into a pressure indication on a calibrated faceplate. The maximum movement of the pointer is usually 270 degrees.
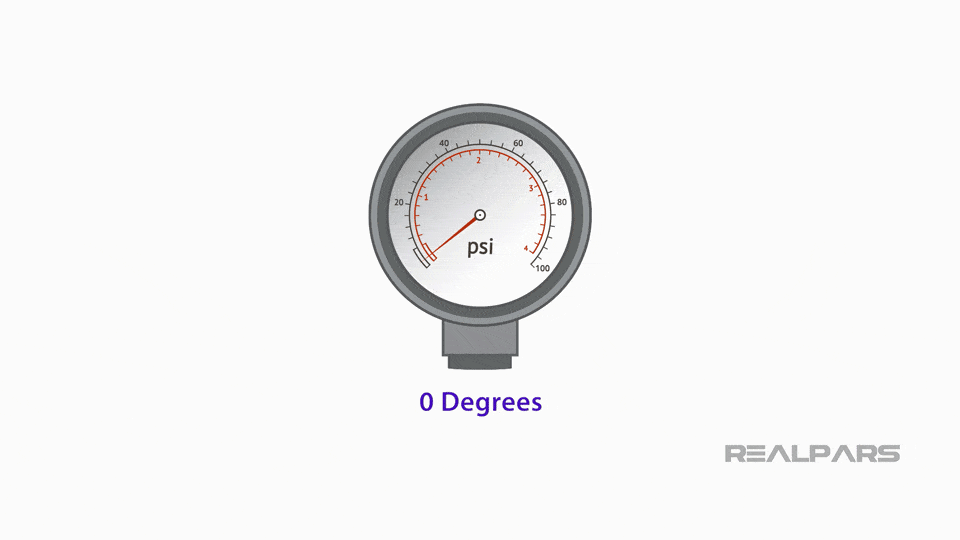
Ok… digging a little deeper we see that a typical bourdon tube pressure gauge has a rack and pinion driven by an adjustable link and lever. As the tube straightens due to a pressure increase, the sealed tip will move.
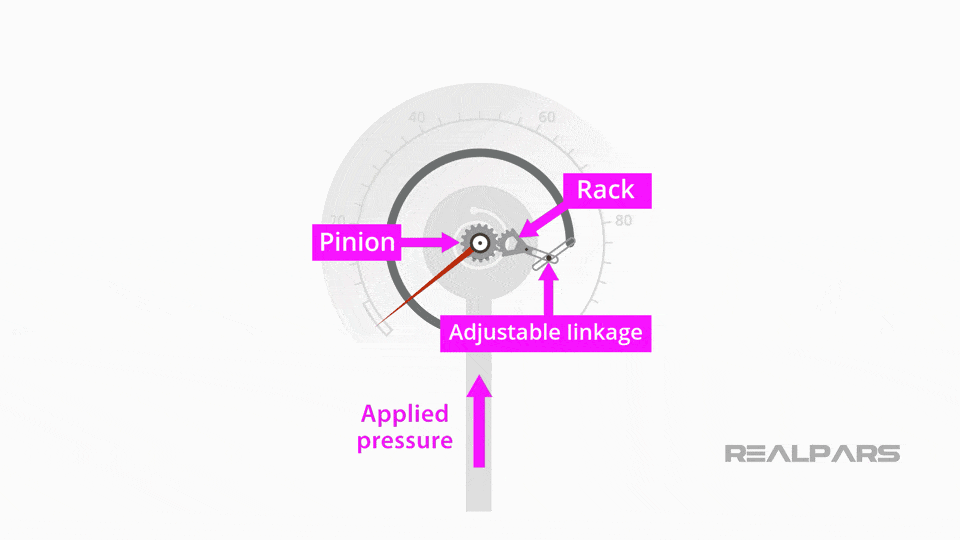
A link attached to the tip of the C tube transfers the motion to a sector gear. The sector gear meshes with a pinion that turns a shaft that is connected to a pointer. The motion of the shaft causes the pointer to move on the calibrated graduated scale.
Zero and multiplication error
As with most instruments, routine adjustments are required on Bourdon Tube pressure gauges.
The two errors that require adjustments are:
– Zero Error
– Multiplication Error
– Zero error is the error of the same amount and in the same direction throughout the entire pressure range regardless of the input pressure.
– Multiplication Error is the error when the total movement of the mechanism does not equal the total change in input.
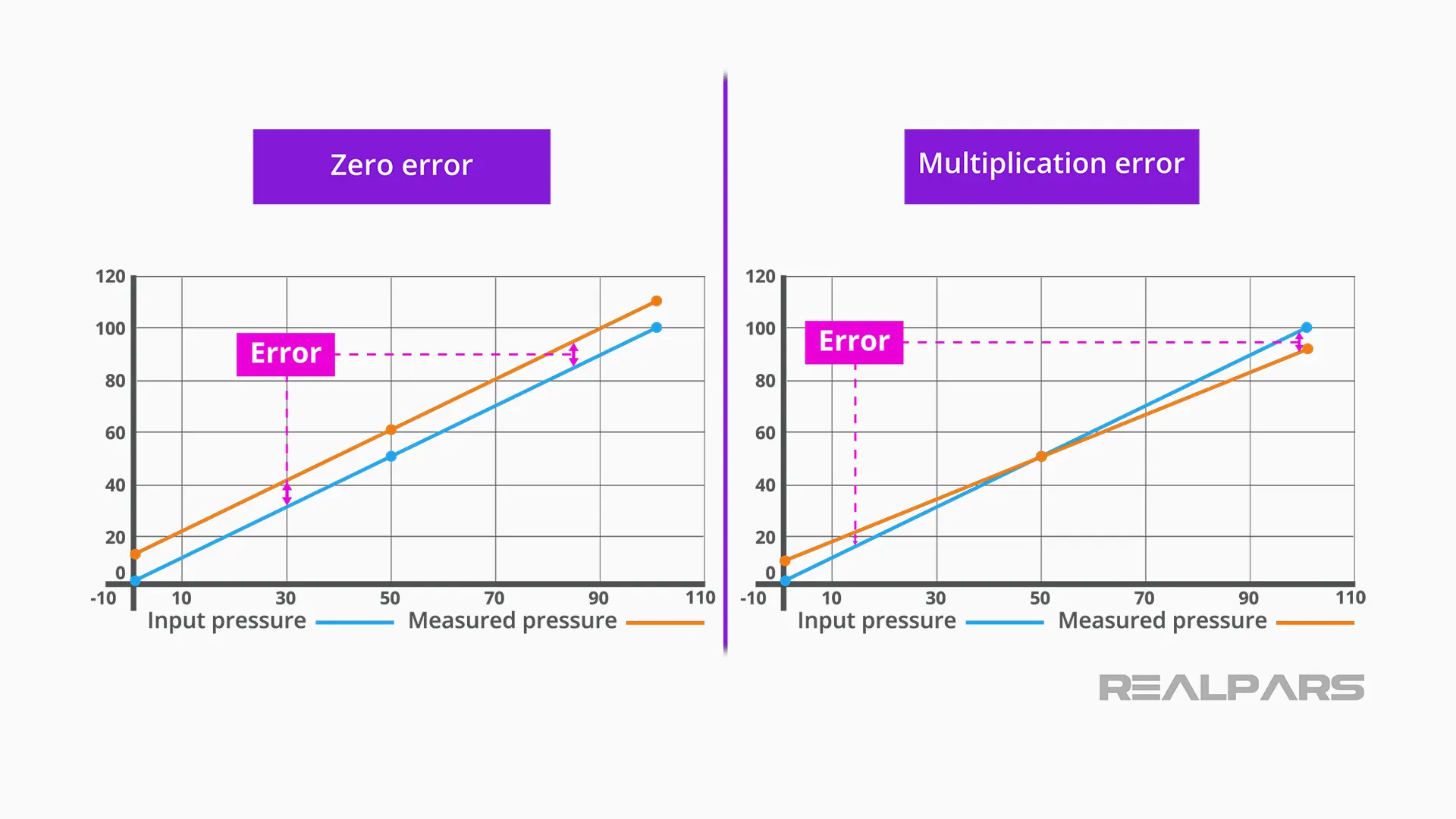
Let’s illustrate with examples. We have a pressure gauge with a calibrated scale of 0 to 100 psi. We’ll apply pressure and watch the readings to determine what type of error exists.
1) With 0 psi in, the gauge indicates 10 psi.
2) With 50 psi in, the gauge indicates 60 psi.
3) With 100 psi in, the gauge indicates 110 psi.
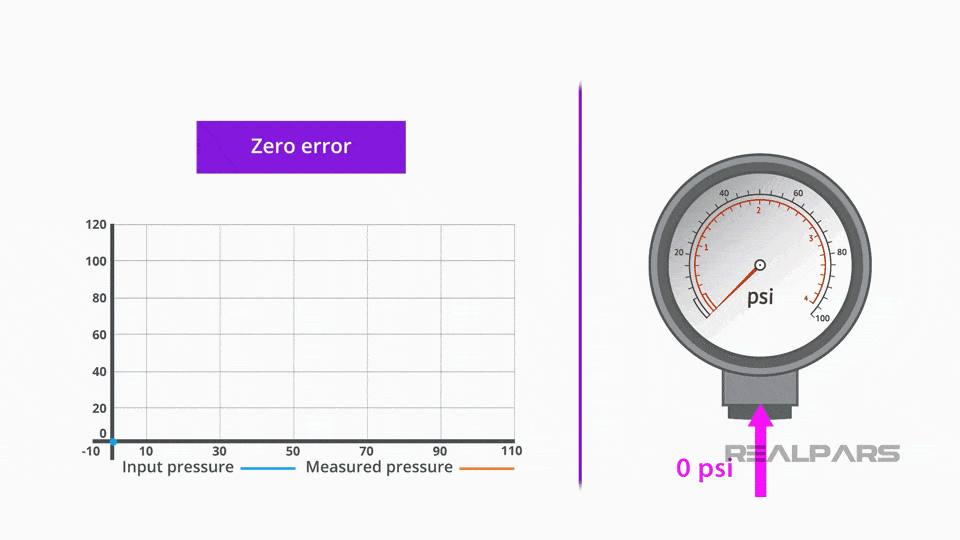
This pressure gauge has a Zero Error because it has a 10 psi error regardless of the input pressure.
Ok… Let’s repeat. We’ll apply pressure and watch the readings to determine what type of error exists.
1) With 0 psi in, the gauge indicates 10 psi.
2) With 50 psi in, the gauge indicates 50 psi.
3) With 100 psi in, the gauge indicates 90 psi.
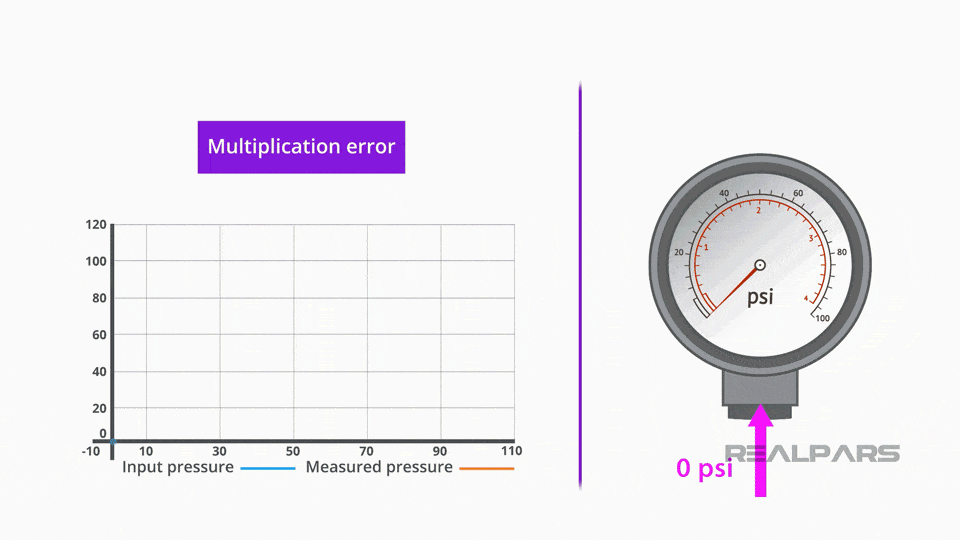
This pressure gauge has a Multiplication Error because the total movement of the mechanism does not equal the total change in pressure input.
Calibration procedure
Calibration is normally done on a workbench using a pressure sourcing device such as a deadweight tester.
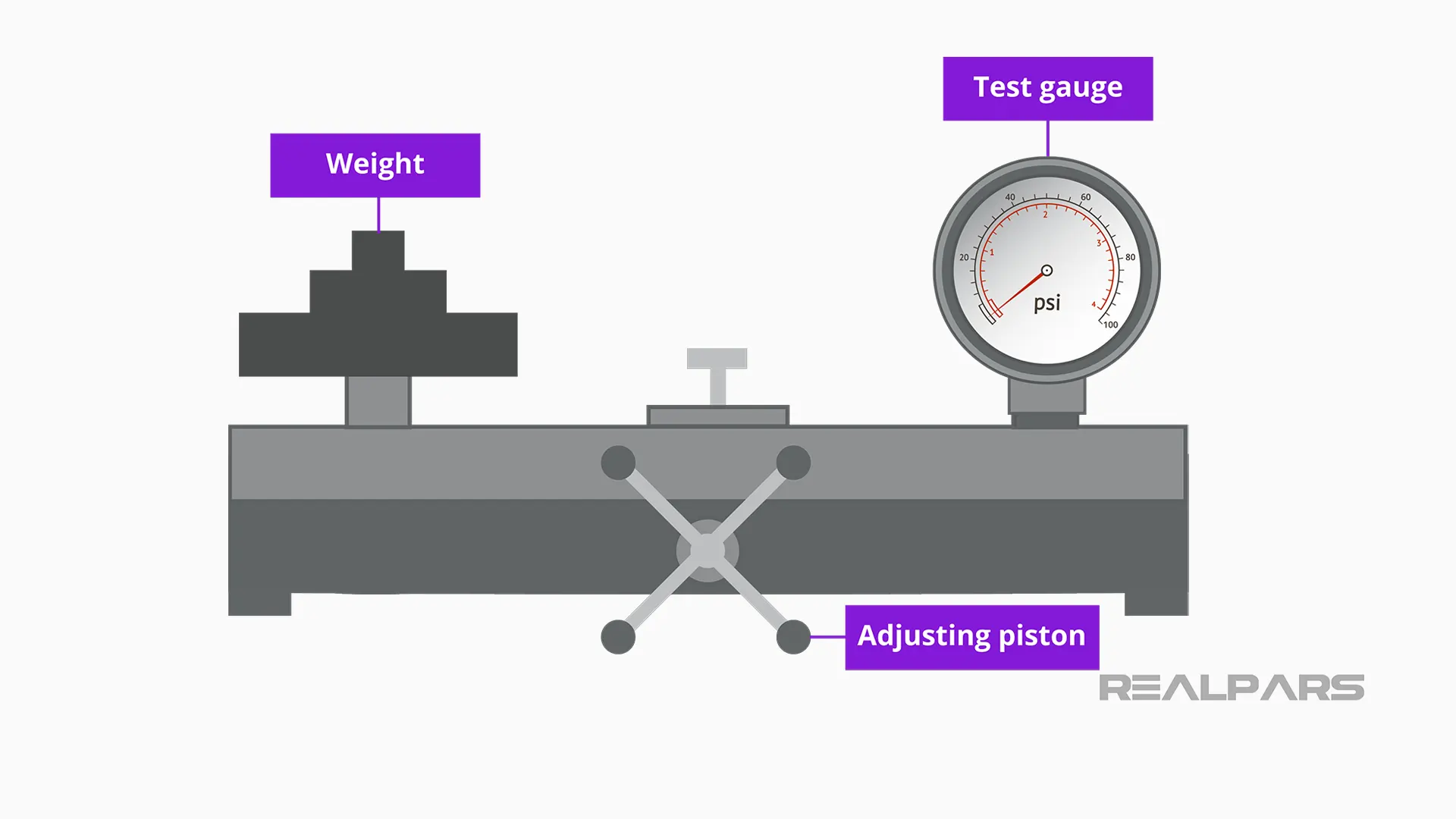
– Zero error is corrected by repositioning the pointer on the shaft or by changing the tension in the spring.
– Multiplication error is corrected by changing the length of the levers.
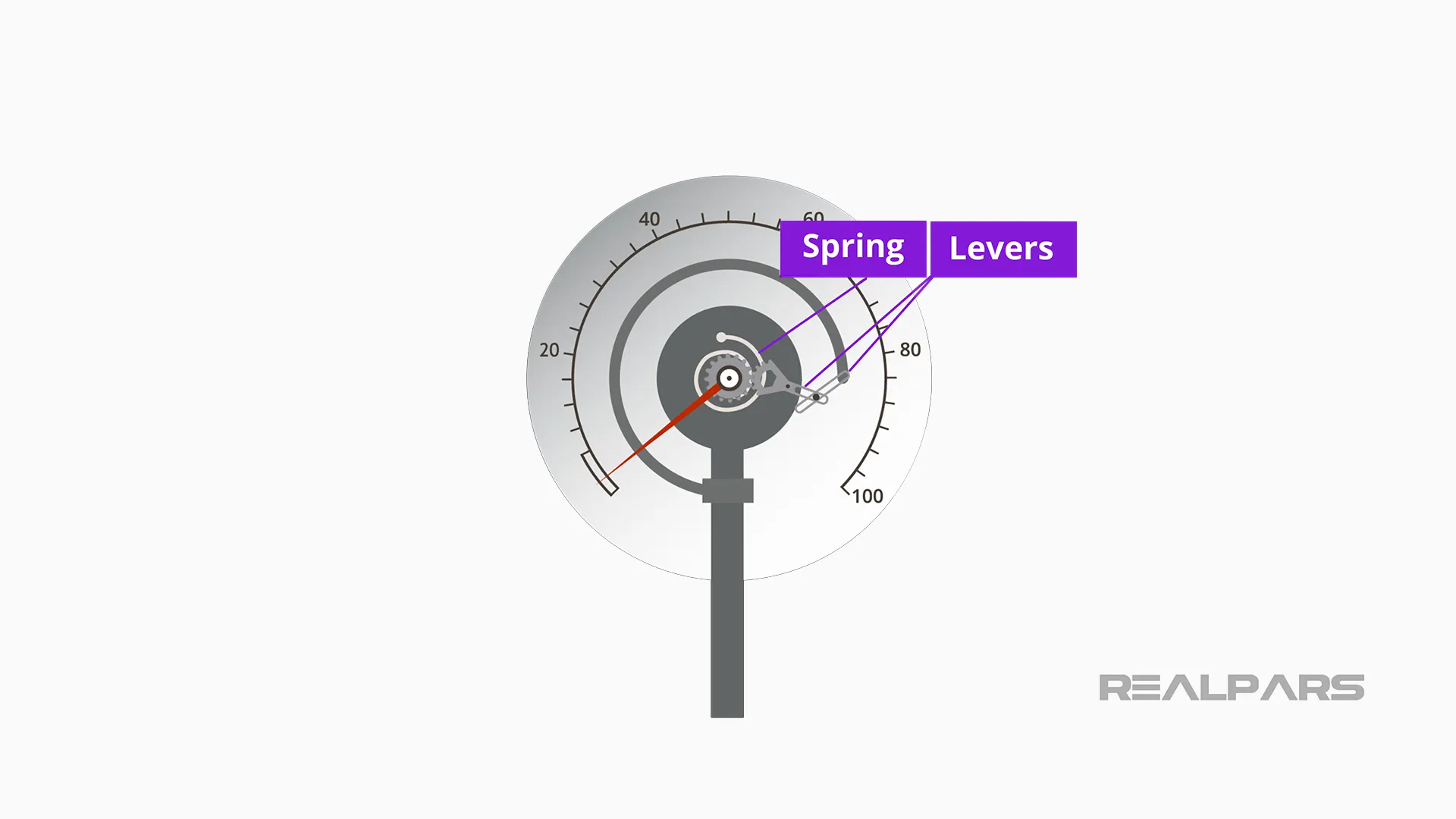
Generally speaking, a mechanical pressure gauge will have an analog readout or analog scale.
Many of today’s pressure gauges are equipped with a pressure transducer that converts pressure into an electrical signal. This electrical signal is then often used to operate a digital display.
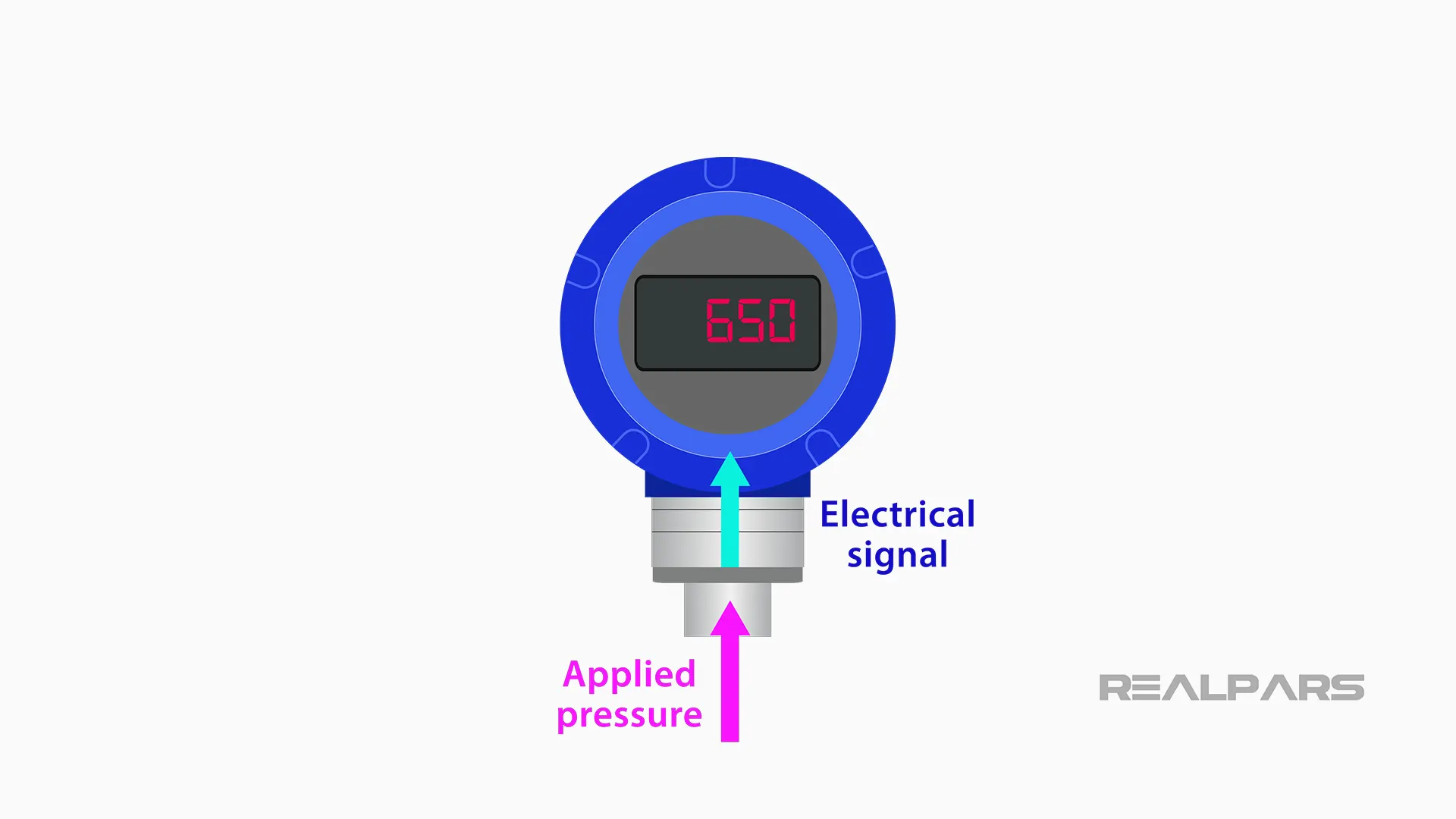
Mechanical pressure gauge accuracy
The American Society of Mechanical Engineers ASME B40.1 Standard defines the accuracy grades of dial-type gauges. Requirements differ from one industry to another and the ASME B40.1 would be your guide for proper selection.
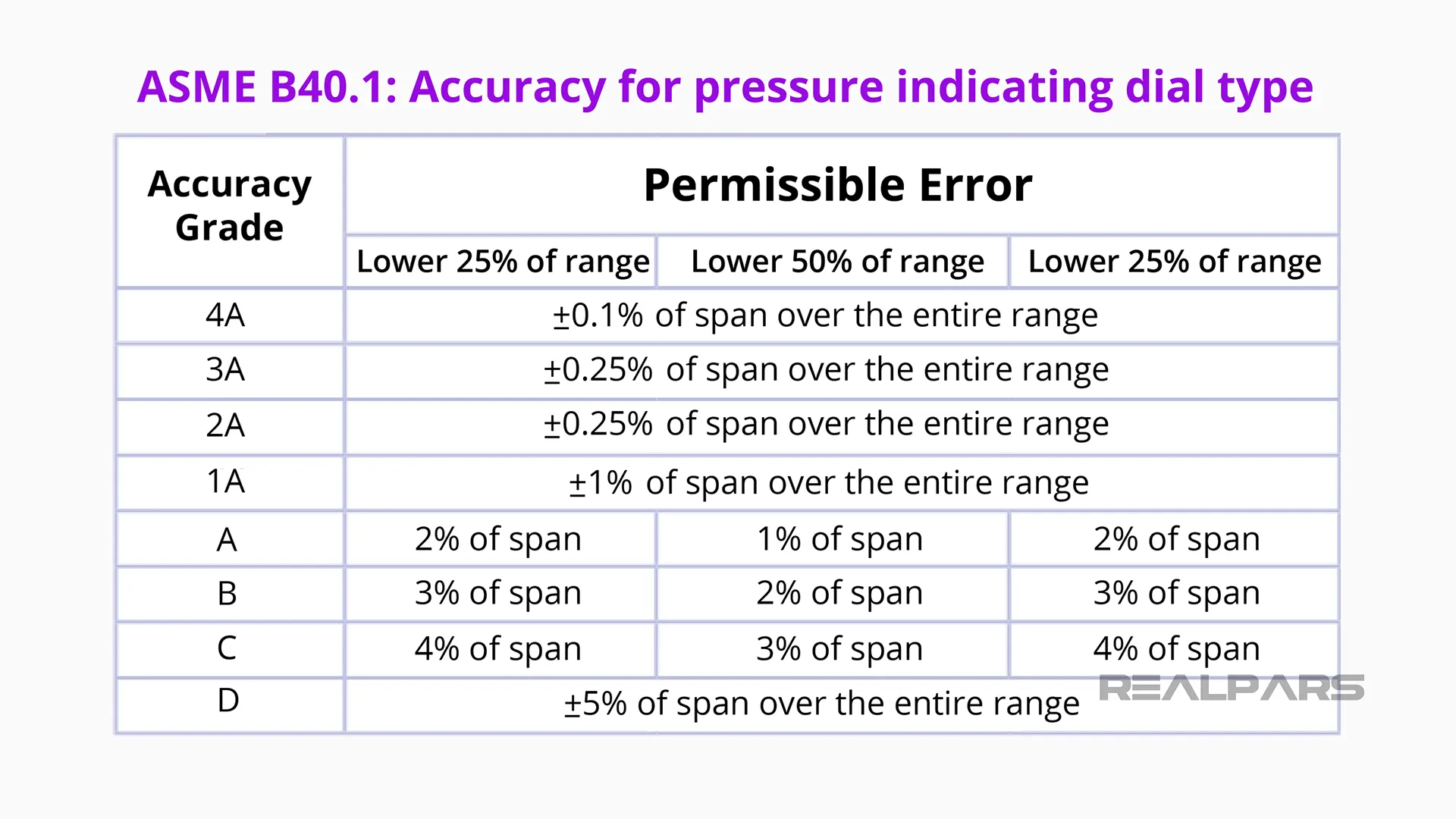
For mechanical pressure gauges, accuracy is usually defined as a percentage of the entire span of the range. For example, a mechanical pressure gauge with a 1A Accuracy Grade has an accuracy of ±1%.
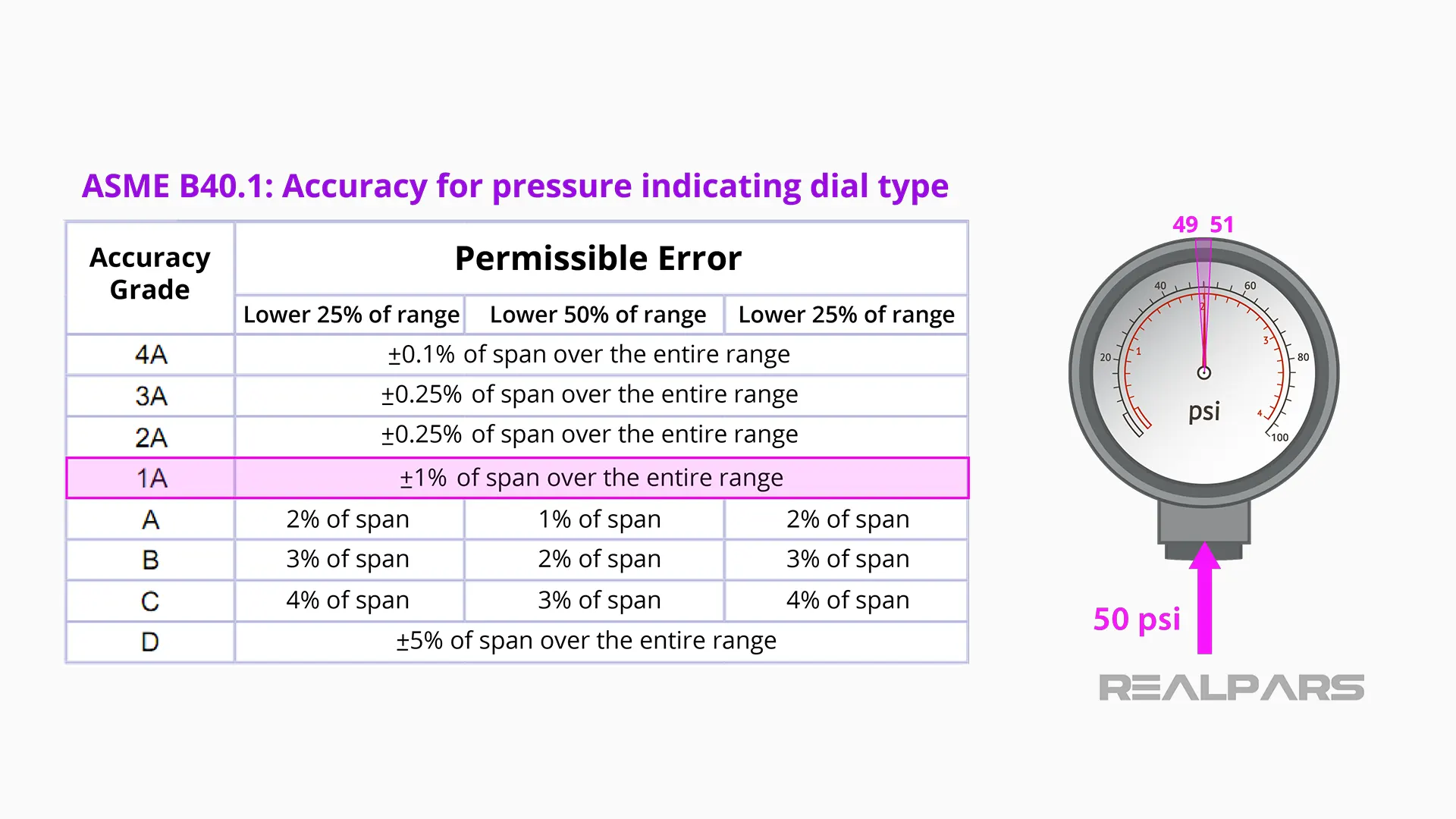
With a reading of 50 psi on a 0 to 100 psi pressure gauge, the actual input pressure can be anywhere between 49 psi and 51 psi.
If you want to learn more about pressure transducers and calibrators you might want to review our other two articles:
– Pressure Sensor, Transducer, and Transmitter Explained
– What is an Instrument Calibrator?
If you have any questions about pressure gauges or about measuring instruments in general, add them in the comments below and we will get back to you in less than 24 hours.
Summary
Alright… Let’s summarize:
– A pressure gauge provides a method of measuring fluid, gas, water, or steam intensity in a pressure-powered machine.
– Pressure is determined by the perpendicular force applied per unit area of a surface.
– Of the many types of mechanical pressure gauges, the three of the most common types are the Bourdon Tube, Diaphragm, and Bellows
– Routine adjustments are required on Bourdon Tube pressure gauges to correct the Zero Error and Multiplication Error.
– Zero error is the error of the same amount and in the same direction throughout the entire pressure range regardless of the input pressure.
– Multiplication Error is the error when the total movement of the mechanism does not equal the total change in input.
– Many pressure gauges are equipped with a pressure transducer that converts pressure into an electrical signal used to operate a digital display.
– The American Society of Mechanical Engineers ASME B40.1 Standard defines the accuracy grades of dial-type gauges.
– For mechanical pressure gauges, accuracy is usually defined as a percentage of the entire span of the range.
Got a friend, client, or colleague who could use some of this information? Please share this article.