Valves, tanks, and pumps are integral components of many industrial and commercial systems. Proper maintenance of these elements is crucial for ensuring efficiency and prolonging the lifespan of the system as a whole.
In this article, you will read about the maintenance requirements of valves, tanks, and pumps. This article also discusses maintenance strategies for keeping an industrial or commercial hydro system running smoothly.
Valves
Valves are mechanical devices that control the flow of fluids in both liquid and gaseous forms. They allow operators to regulate the flow of fluids, as well as isolate certain parts of the system for maintenance or repair.
Valves come in different types, including gate valves, globe valves, ball valves, and butterfly valves. Each type of valve has specific features and maintenance requirements, but some general tasks apply to all valves.
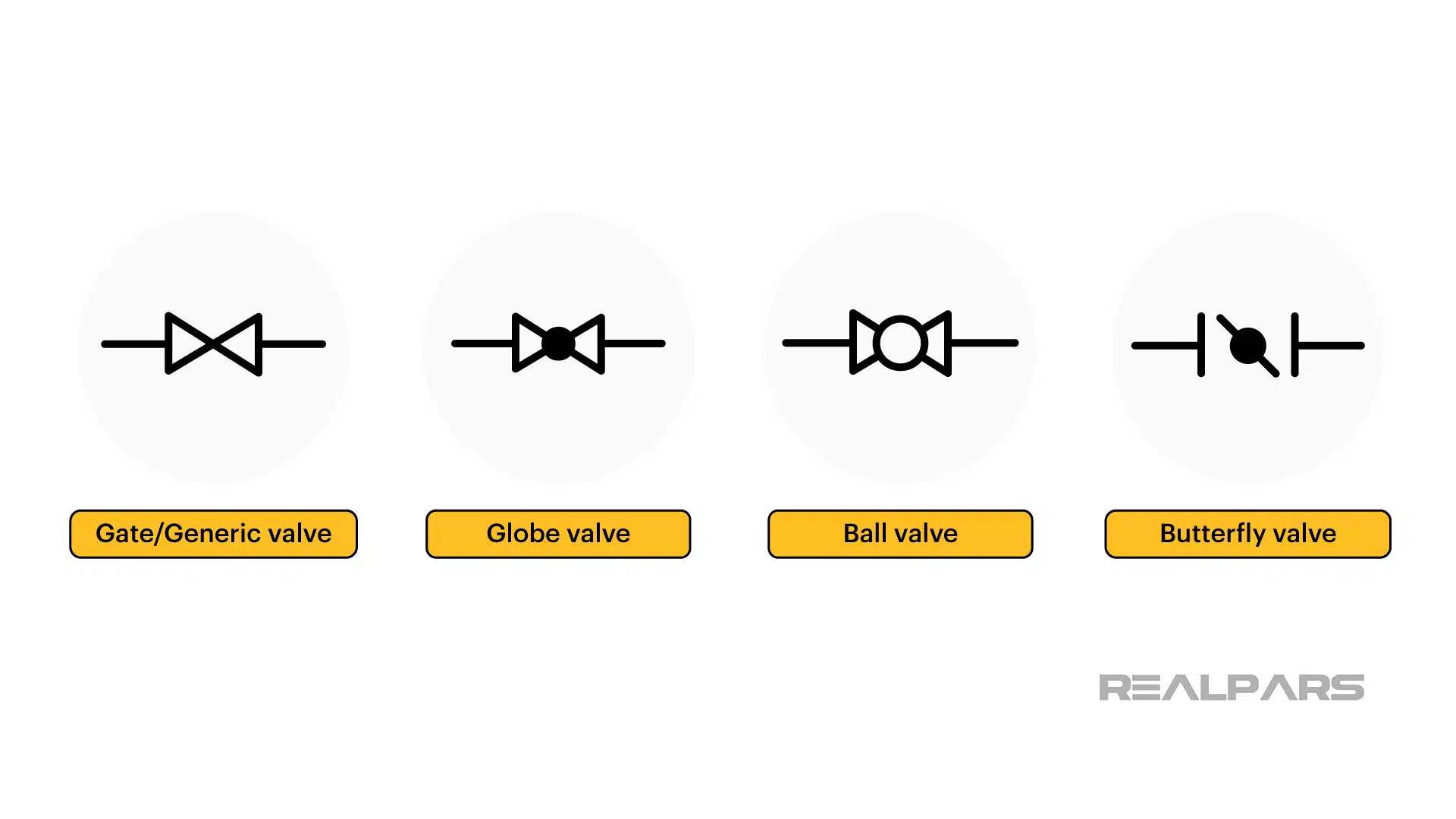
One of the main issues that can affect the performance of valves is mineralization, rust, and corrosion. These problems can occur due to a variety of factors, such as exposure to corrosive substances, high levels of humidity, or a lack of maintenance.
To prevent these issues, it is important to follow a regular preventative maintenance schedule.
This can include tasks such as:
– Cleaning and lubricating valve stems and seats regularly
– Inspecting gaskets and seals periodically; replace them when required
– Tightening bolts and nuts
– Testing valve operation and performance
– Using protective coatings or rust inhibitors to prevent corrosion
Neglecting proper valve maintenance can result in reduced system efficiency and unexpected downtime due to valve failure.
By proactively addressing issues such as mineralization, rust, and corrosion, you can help ensure that your valves are always operating at peak efficiency.
Tanks
Tanks are container vessels used to store liquids, gases, or other materials. They are commonly used in a wide range of industries, including oil and gas, chemical processing, water treatment, and food and beverage.
Tanks can be made from a variety of materials, including steel, plastic, fiberglass, and concrete. The type of material used will influence the maintenance requirements of the tank.
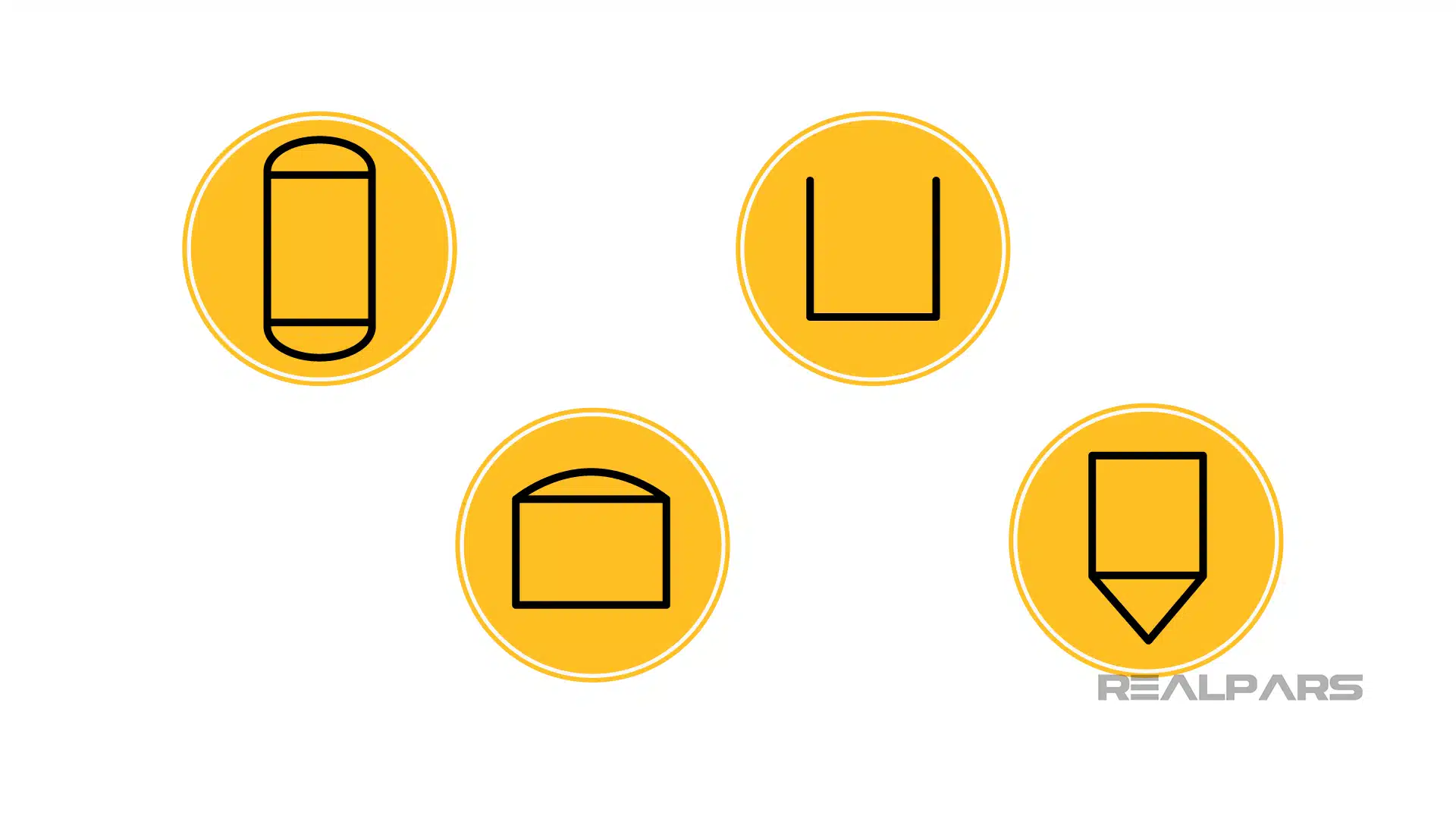
Proper tank maintenance is essential for ensuring the integrity and safety of tanks and hydro systems. This can include tasks such as:
– Regular maintenance inspection of tanks for signs of corrosion, damage, or leaks
– Using paint, rust-inhibiting primer, or other appropriate protective coatings to prevent corrosion
– Leaving the coating to cure before putting the tank back into service; it should also be sterilized for disinfection
– Regularly topping up bleach to eliminate algae; using opaque tanks is another way to prevent algae growth
– Inspecting plumbing components that deliver fluids in and out of the tank for leaks, corrosion, or damage
Neglecting proper tank maintenance can result in leaks, contamination of stored materials, and decreased system efficiency. Preventive maintenance should be done to prevent any such problems.
Pumps
Pumps are mechanical devices used to move liquids and gases through a hydro system. They are used in a wide range of industries, including oil and gas, chemical processing, water treatment, and manufacturing.
There are many types of pumps, including centrifugal pumps, positive displacement pumps, and rotary pumps. Each type of pump has its specific features and maintenance requirements.
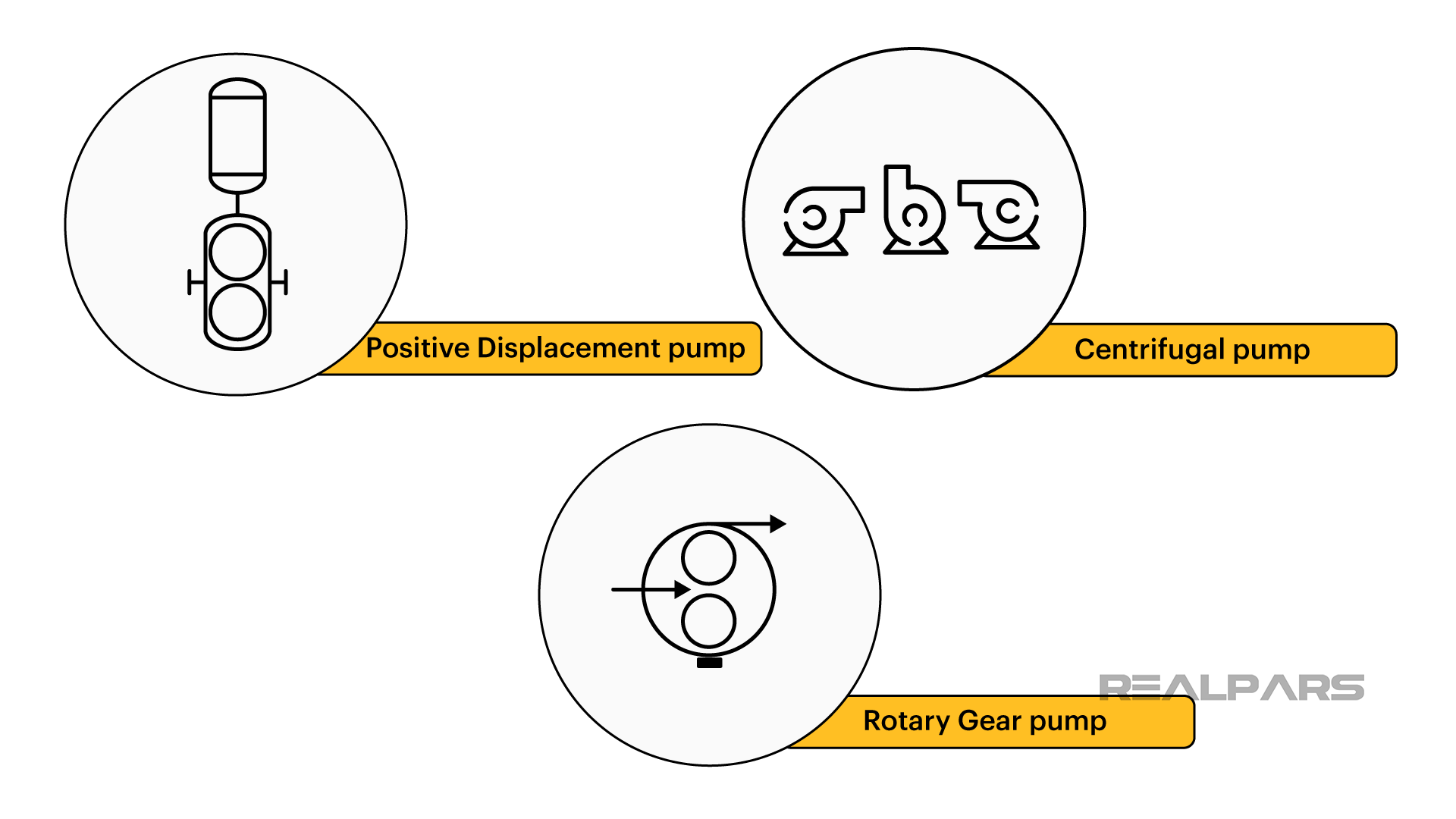
The accurate and efficient operation of pumps is ensured by regular and proper maintenance. This can include tasks such as:
– Cleaning and lubricating pump components
– Inspecting and replacing worn or damaged parts
– Testing pump performance and operation
– Maintaining correct pump alignment
Neglecting proper pump maintenance can result in reduced efficiency of your hydro system and unexpected downtime due to pump failure. Perform the maintenance activities promptly to maintain efficiency and uptime.
Maintenance strategy
A maintenance strategy is a plan for how to regularly inspect, maintain, and repair the elements of a system.
An effective maintenance strategy can help to reduce downtime, prolong the lifespan of equipment, and improve overall system performance.
There are several key considerations for developing a maintenance strategy:
– Identify the critical system components: These are the elements that are essential for the system to function properly. These components should be given priority in the maintenance strategy.
– Determine the frequency of maintenance: This will depend on the type of hydro system, the environment it operates in, and the manufacturer’s recommendations.
In general, it’s best to err on the side of caution and schedule maintenance more frequently rather than less often.
– Establish a maintenance schedule: This can be a calendar-based schedule, or it can be based on usage or operating hours. It’s important to establish a clear schedule to ensure that maintenance tasks are completed regularly.
– Assign responsibilities: It is important to have a clear understanding of who is responsible for completing each maintenance task. This can help to ensure that tasks are completed promptly and that any issues are addressed promptly.
– Keep accurate records: It’s important to keep a record of all maintenance activities, including the date the task was completed, the person who completed the task, and any issues or problems that were identified.
This information can be useful for identifying trends and identifying potential problems before they become major issues. Historical records are useful in implementing predictive maintenance strategies.
In the case of hydro systems, it is important to follow the recommendations for maintenance. Any existing industry standards also need to be adhered to.
Building an efficient hydro system
Proper maintenance of valves, tanks, and pumps is essential for ensuring the efficiency and longevity of industrial or commercial hydro systems.
By developing and implementing an effective maintenance strategy, operators can reduce downtime, improve system performance, and prolong the lifespan of their equipment.
Whether you’re working with a small, simple hydro system or a large, complex one, following these best practices can help you achieve optimal results.