In the free world, business is driven by many factors, including creating value and equity for owners or shareholders. This requires providing useful products at a competitive price and minimizing costs and disruptions in the supply of labor and material resources used to create those products.
In the past 20 years, US manufacturers have lowered costs by moving manufacturing capacity to countries that traditionally have much lower labor costs. Even with shipping costs, the overall market price for the finished goods was made more competitive.
Some raw materials were sourced from other countries, either because of plentiful supply or cost. In the process, US manufacturers had created dependencies on other countries for key components.
For example, in 2004, a tsunami that affected Thailand caused an interruption in the supply of hard disk drives that severely affected some computer hardware suppliers. Recently, political differences have led some countries to add steep tariffs to these products or choose not to supply them at all.
Other issues have risen, many of which were accentuated by the COVID pandemic.
Interruptions to supply chains due to lockdowns and work stoppages, especially to medical components and ingredients and semiconductors, crippled many industries and companies. Costs in other countries for raw materials and labor were also rising at the same time.
Some of the decisions made earlier were being reconsidered, and a movement was born to Get Manufacturing Back to the USA. This shift in thinking has the intention of bringing manufacturing back to the U.S. for economic and operational benefits.
Having domestic control over supply chains and cutting dependencies on other countries will provide greater opportunity and economic growth for the USA.
Automation is proving to be a key asset in helping businesses re-shore successfully. Automation helps to decrease costs, increase efficiency, and improve product quality. Companies are realizing there is great value in being able to say their products are Made in the USA!
Is your company thinking about reshoring? Download our free guide: Is Your Factory Reshoring-Ready? A Step-by-Step Automation Guide.
Automation: The key to reshoring success
With the reshoring of manufacturing, companies will need to strive to offset higher labor costs. Automation strategies, such as robotics, the Internet of Things, and Artificial Intelligence can provide this offset by improving efficiency and reducing the need for manual labor.
Robotics can provide precision parts placements at higher rates of speed than is possible with human labor.
IoT provides detailed real-time data from the plant floor to application servers in the cloud. It is there that AI can optimize production schedules and make operational decisions to minimize costs and maximize throughput.
We have several courses on these topics. If you want to learn more, check out realpars.com/courses and filter for the skills you want to learn.
Automated systems help to minimize downtime. Downtime is a cost to the manufacturer both in labor and lost production.
Automation tools, such as coordinated predictive maintenance applications, such as condition-based monitoring, help ensure factories run efficiently by eliminating costly equipment failures that cause downtime.
A recent study by GE showed that companies in the Oil & Gas sector who are using modern predictive maintenance tools have reported up to 35% reduction in unplanned downtime.
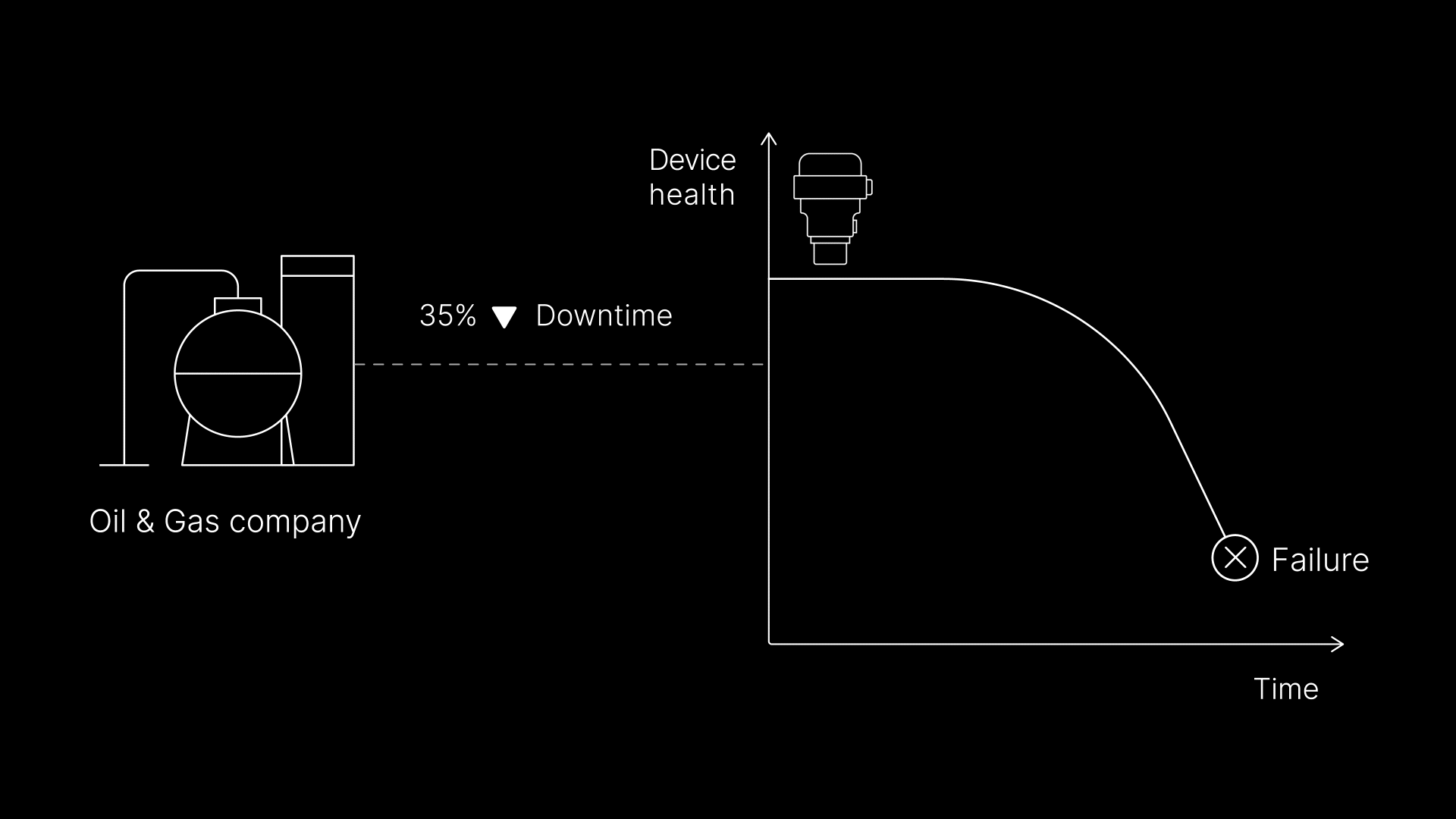
With the application of these advanced technologies comes the need to train teams on how to deploy, operate, and maintain these new technologies. This is essential in order to maximize the benefits of automation.
Employing these automation tools and providing world-class training for your employees can transform your factory into a competitive powerhouse.
Explore a RealPars Business Membership for on-demand training in PLC programming, predictive maintenance, and more to get your team reshoring-ready.
Overcoming reshoring challenges
In addition to its many benefits, reshoring manufacturing will come with many challenges. Among those are a high initial investment in technology and overcoming the skills gap in the workforce.
Companies need to acknowledge the upfront costs of reshoring and providing the level of automation that will provide long-term benefits like efficiency, reduced downtime, and improved quality.
A detailed and realistic digital transformation strategy can provide a solid roadmap for the adoption of the appropriate level of automation and determine a capital strategy needed to make this transformation possible.
A very real and well-documented roadblock is the shortage of workers trained in automation technologies. This challenge can be overcome only through training programs that focus on the in-demand skills required to operate a modern, automated manufacturing plant.
Our free guide, Is Your Factory Reshoring-Ready? A Step-by-Step Automation Guide, can help you navigate these challenges and start your reshoring journey.
Steps to make your factory reshoring-ready
The first step to make your factory reshoring-ready is to assess your current operations to determine where there may be inefficiencies and bottlenecks in your current supply chain and production processes.
Many professional organizations have prepared checklists and procedures for determining readiness.
Steps you can take include making a list of all of the dependencies your operation has. Look at components, materials, and other processes, such as IT support, accounting, and inventory management that may lie with overseas providers.
Next, evaluate risks and determine costs. Which suppliers are in areas that are politically unstable or pose a domestic threat to the supply chain? Have certain suppliers had quality issues or constant delivery delays? What is the current schedule of tariffs, transportation costs, and costs for inventory holds?
Finally, how do lead times affect your production scheduling? What if a critical part is one day late? Or one week late in arriving? Are there alternate domestic suppliers?
The next step to make your factory reshoring-ready is to determine the many ways that automation can make your operation more resilient and efficient. As discussed earlier, robotics, artificial intelligence, IoT, and data analytics can enhance reliability and efficiency and reduce costs.
The final step is to train and upskill your employees to ensure your technical team, from engineering to maintenance to operations, can effectively operate and maintain these new automation technologies.
Take the first step toward reshoring success. Download our free guide: Is Your Factory Reshoring-Ready? A Step-by-Step Automation Guide.
Conclusion: A new Era for U.S. manufacturing
Automation is one key component of making your re-shoring initiative as cost-effective and transparent as possible. In this article, I have presented re-shoring as a positive way to gain more control over your supply chain risks and reap the many benefits of Made in the USA!
Are you ready to join the Get Manufacturing Back to the USA movement and build a stronger, more competitive future for U.S. manufacturing? Our free guide, Is Your Factory Reshoring-Ready? A Step-by-Step Automation Guide, can help you navigate these challenges and start your reshoring journey.
If you're a plant manager looking to train your maintenance team, visit realpars.com/business. Just add your contact information, and our team will quickly get in touch to discuss how we can support your team's development.