In this article, we’re going to explore the differences between Solid State and Relay outputs on PLC Digital Output Modules. We’re also going to talk about the pros and cons of each.
The purpose of a PLC Output module is to operate or control a physical device based on field device conditions connected to an input module and decisions made by the PLC program.
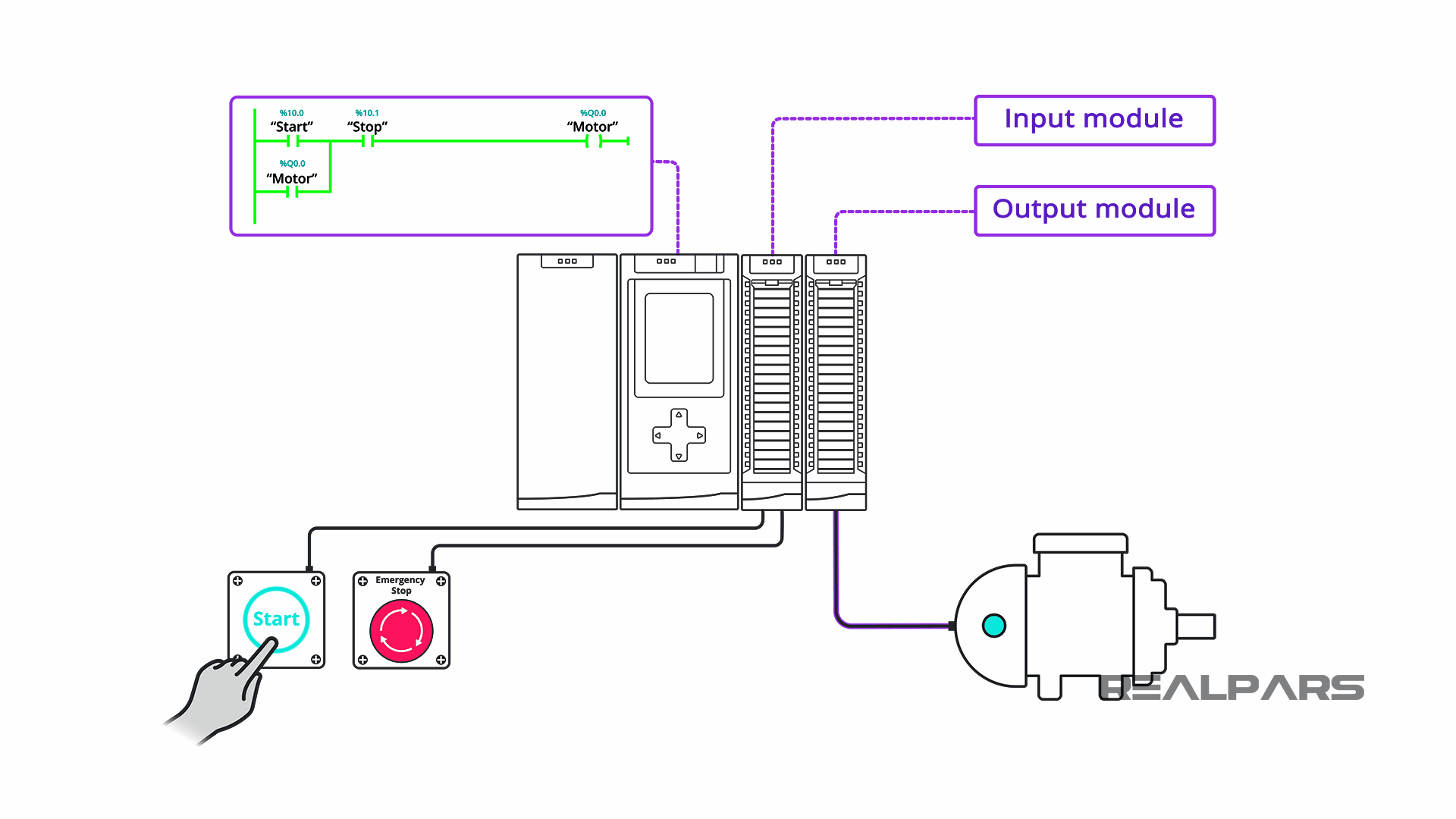
Digital vs Analog
Before we get into Solid State and Relay PLC outputs, let’s clear up the difference between a Digital Output Module, or DO, and an Analog Output module, or AO.
Digital or Discrete devices have only 2 possible conditions. As examples, these 2 possible conditions could be On or Off, Open or Closed, or Energized or De-energized.
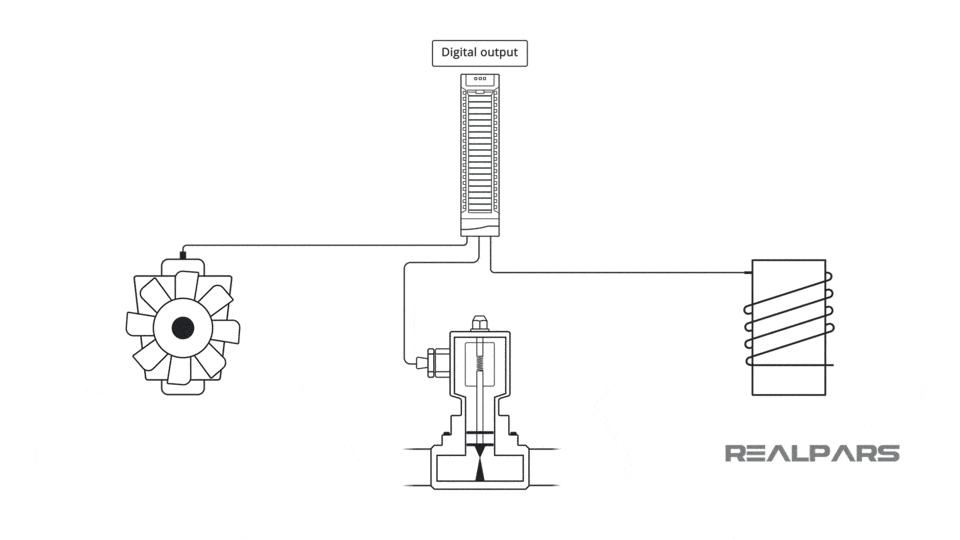
Analog devices are a bit more complicated because they have an infinite number of possible conditions.
To illustrate, we said earlier that a fan is a digital device if it can be turned either on or off. But, what if the fan can be adjusted for any speed from Off to On? In that case, the fan is an analog device because it has an infinite number of possible speeds.
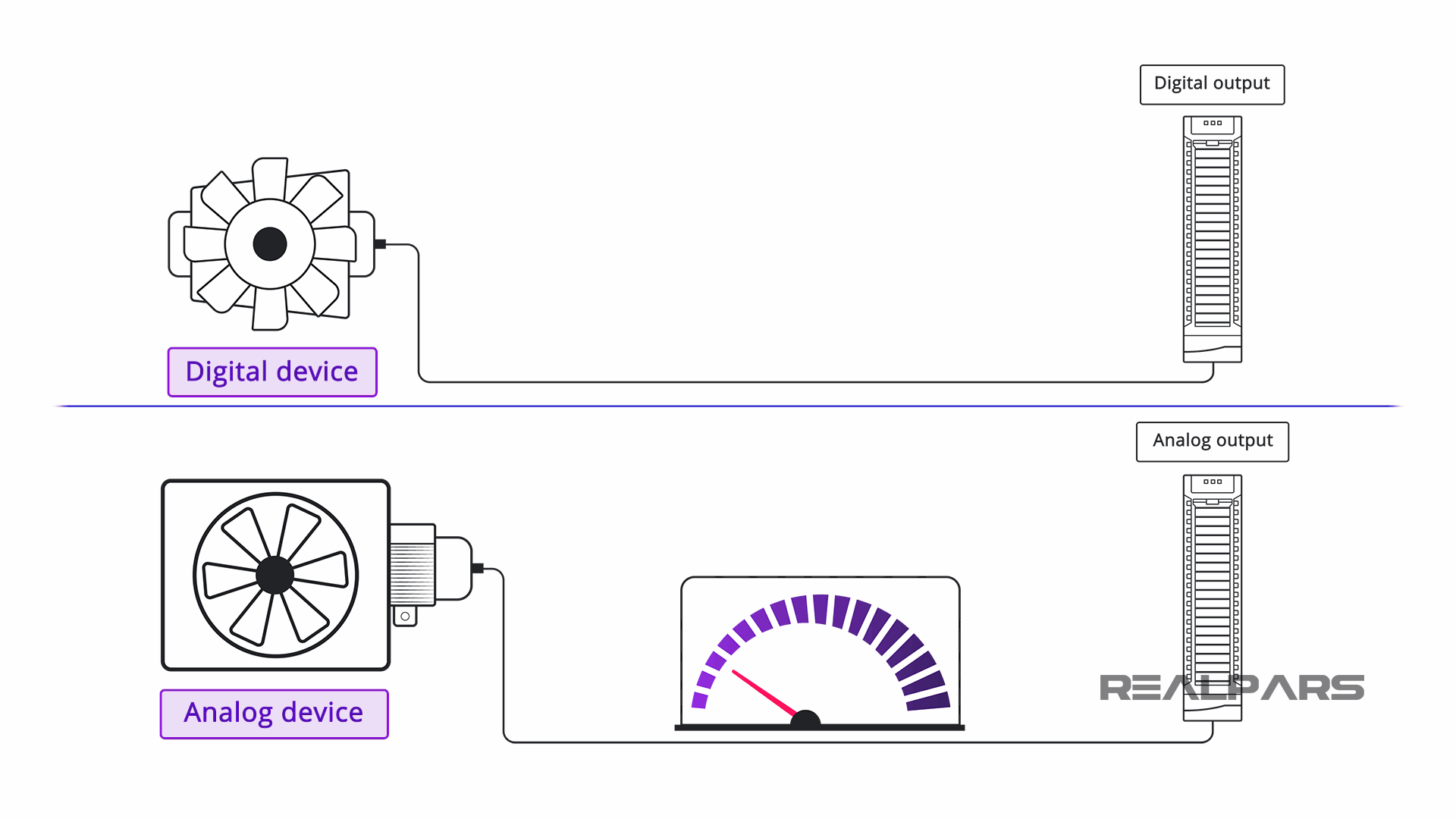
PLC digital output module types
Ok, now that we’ve clarified the difference between digital and analog devices, let’s dig deeper into PLC Digital Output Modules.
There are 2 types of PLC Digital Output Modules:
1) Relay
2) Solid State
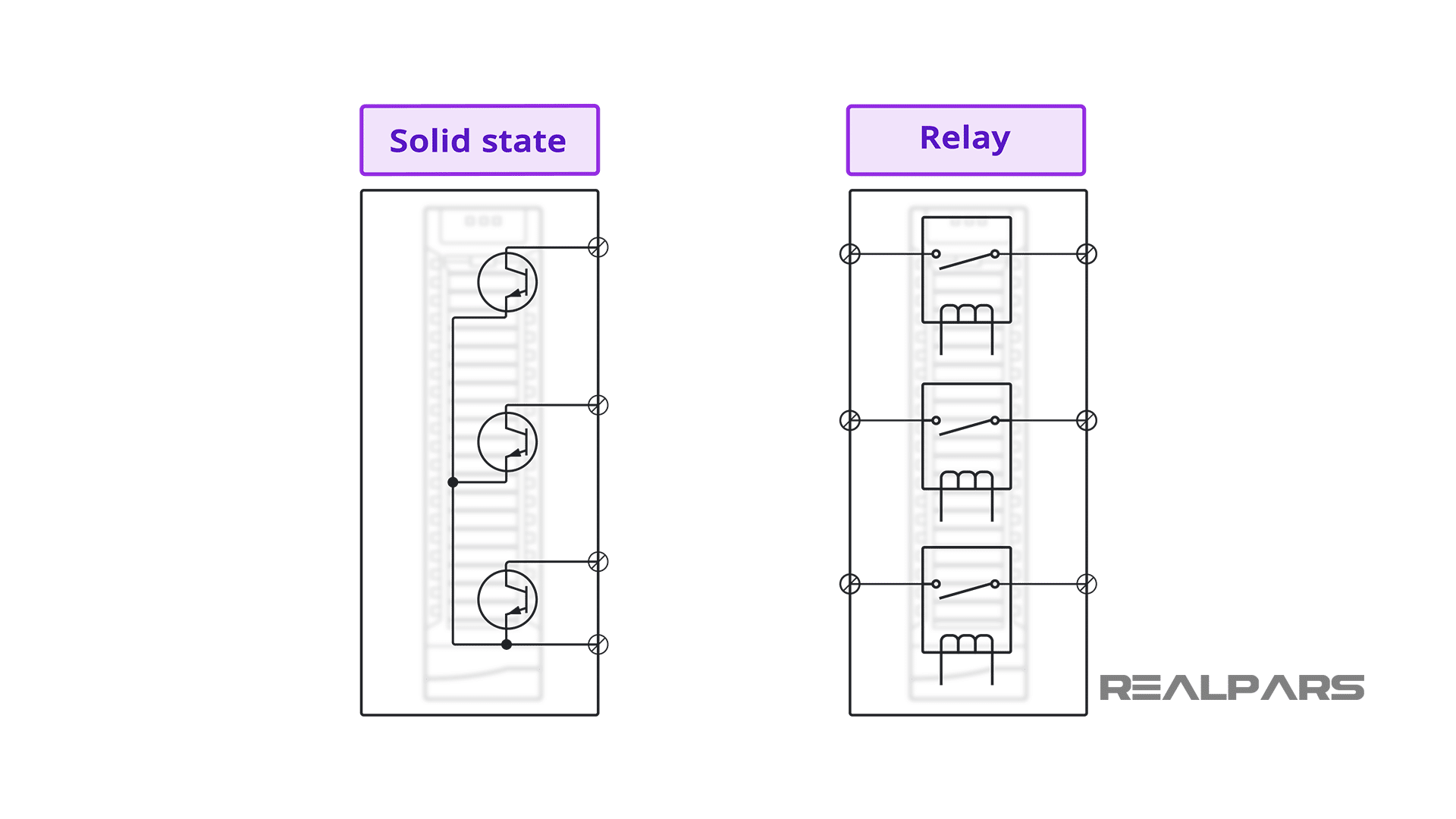
1) Relay output module
When PLCs were first introduced, the only outputs were relay type with a separate relay dedicated to each output.
As with any typical relay, the PLC output module had physical coils and relay contacts contained inside.
The contacts were operated by applying a voltage to the relay coil. The contacts were connected to an external supply to turn on or off a discrete device. Not much has changed except today’s modules have miniaturized relays and contacts.
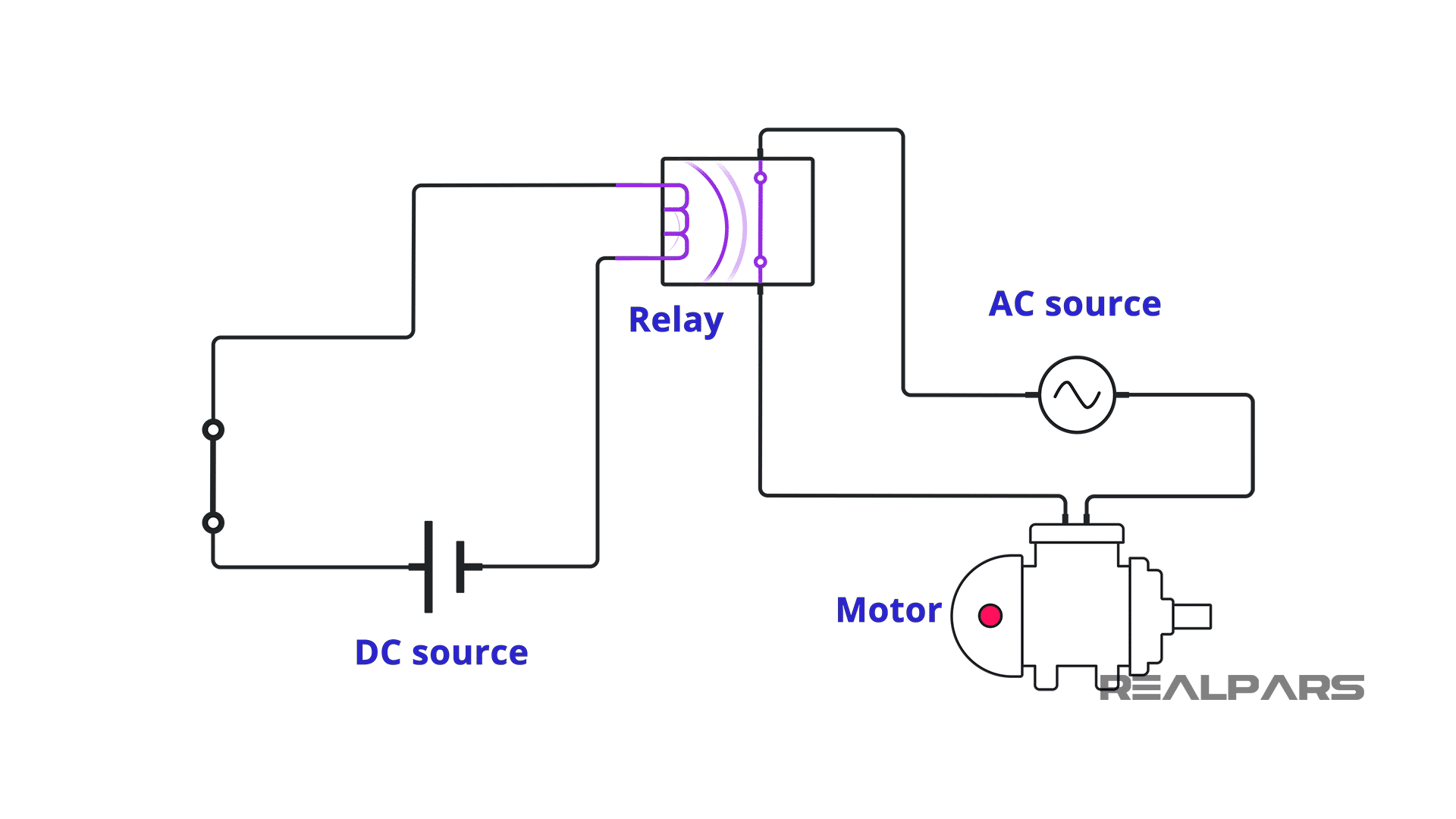
Allen Bradley 1756-OW16I
Let’s look at an example of an industrial PLC relay output module. The Allen Bradley 1756-OW16I has 16 individual relay outputs.
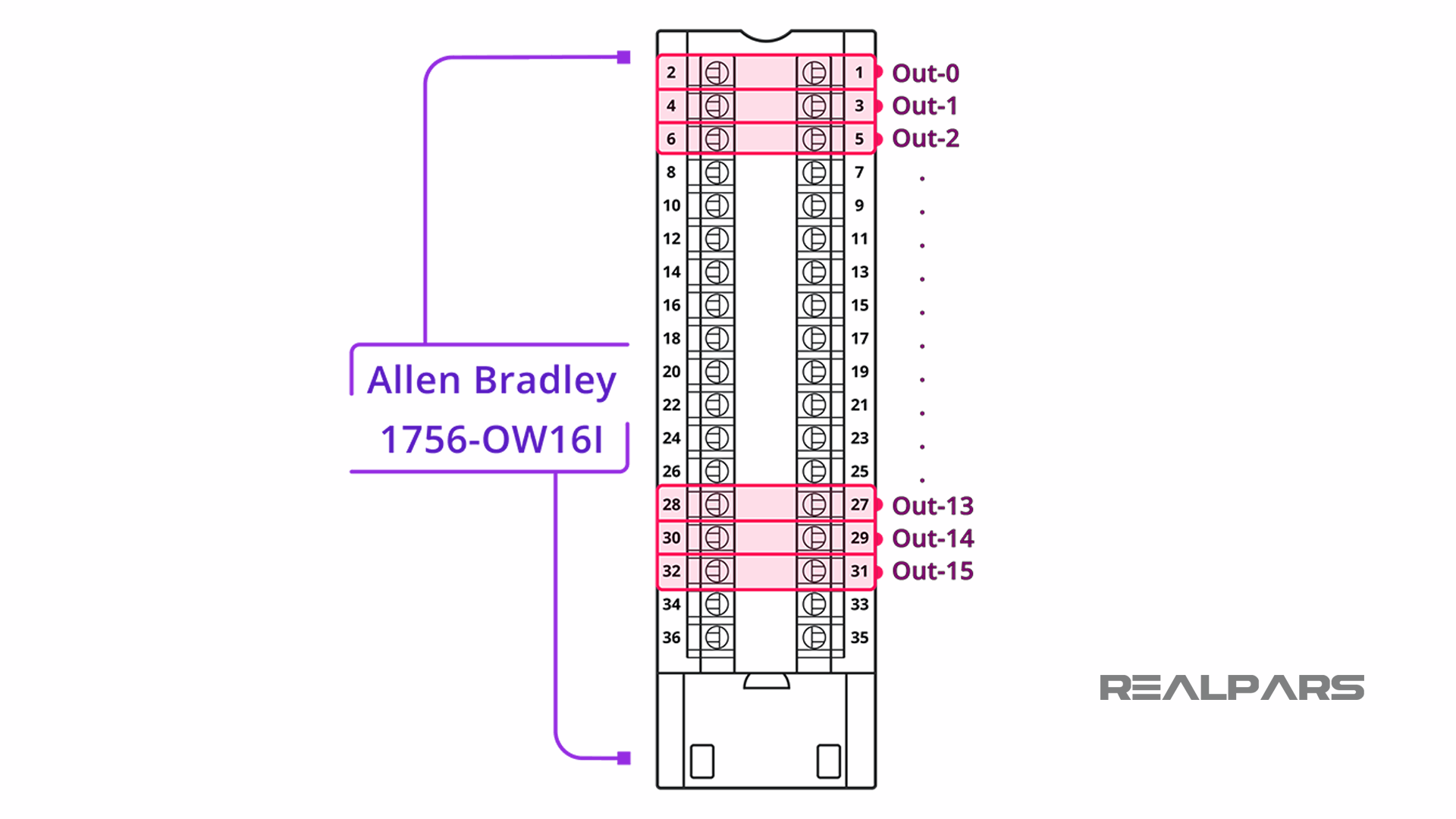
We can use one output to operate an AC load and another output to operate a DC load as relay contacts are voltage-independent. That’s one advantage of relay type as solid-state type output modules are not voltage-independent.
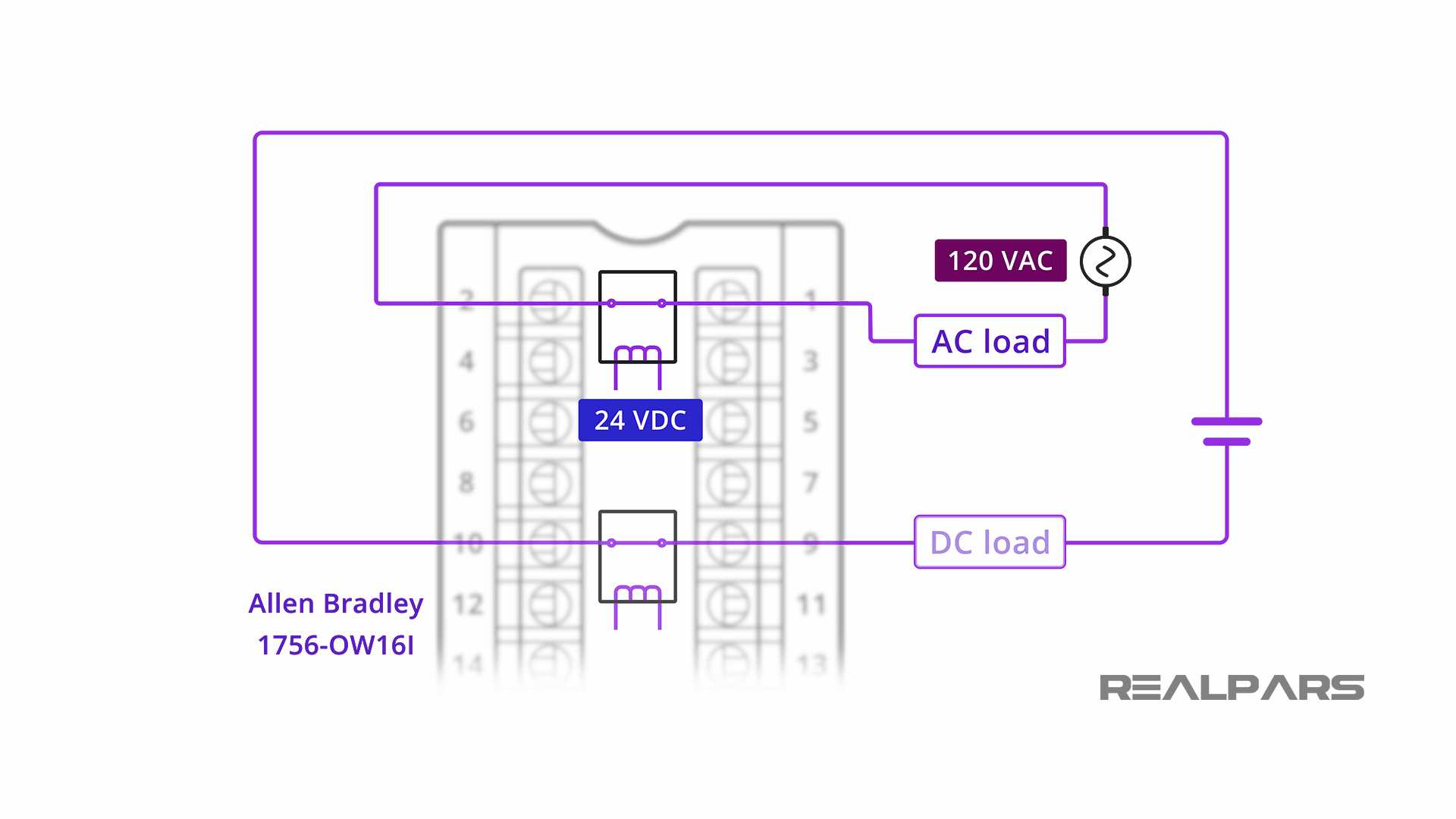
Allen Bradley 1756-OX8I
Relay Output modules are available with Single Pole Double Throw, or SPDT outputs as well, as seen on the Allen Bradley 1756-OX8I module.
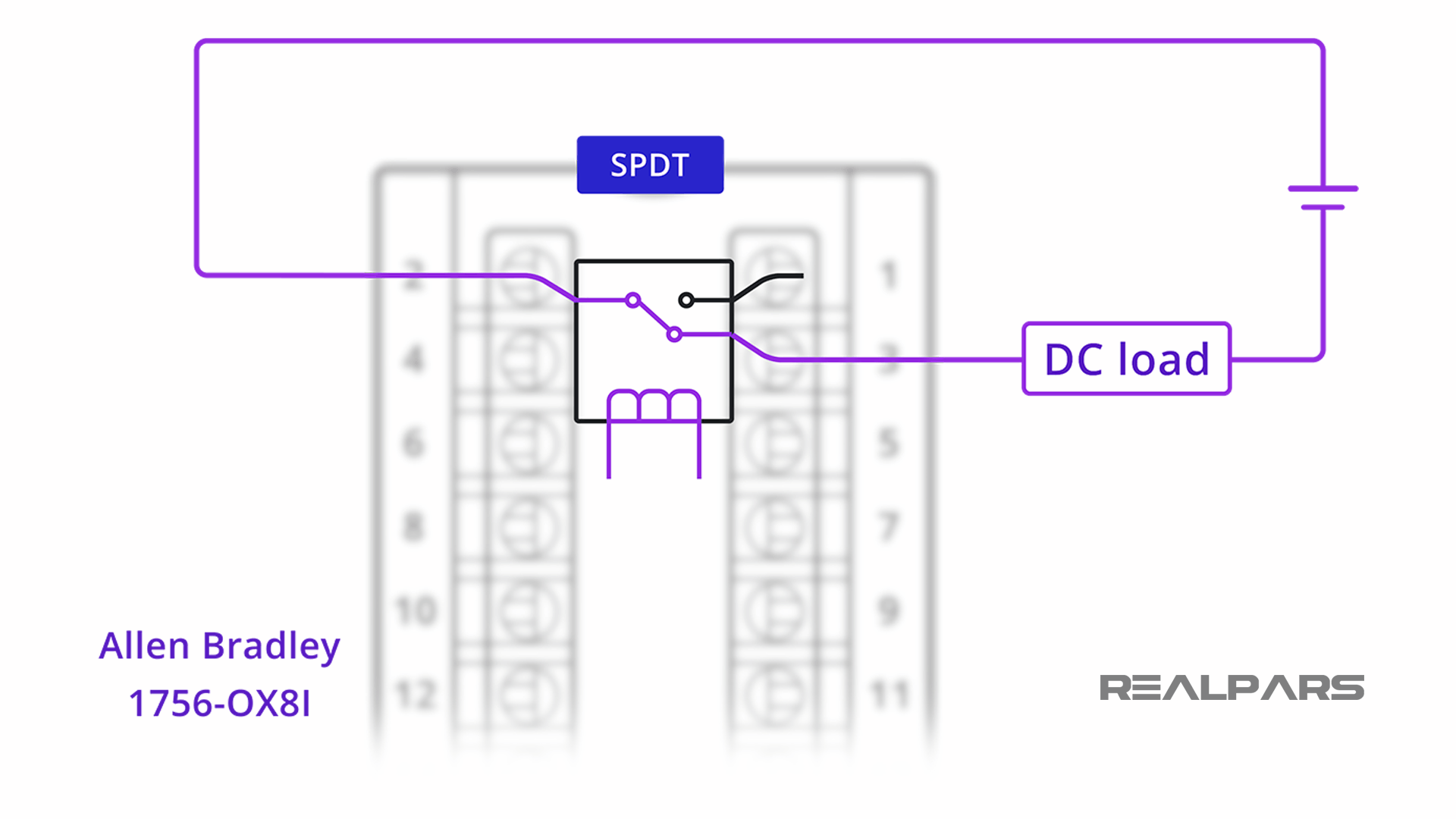
2) Solid-State output modules
Solid-State output modules are often referred to as Switching modules. Output devices are turned on or off by using solid-state devices such as a Bipolar Junction Transistor (BJT) or a Triac.

2-1) Transistor output modules
As we said earlier, the transistor output module is voltage-dependent and can only operate DC loads, unlike a relay output module that is happy to operate AC or DC loads.
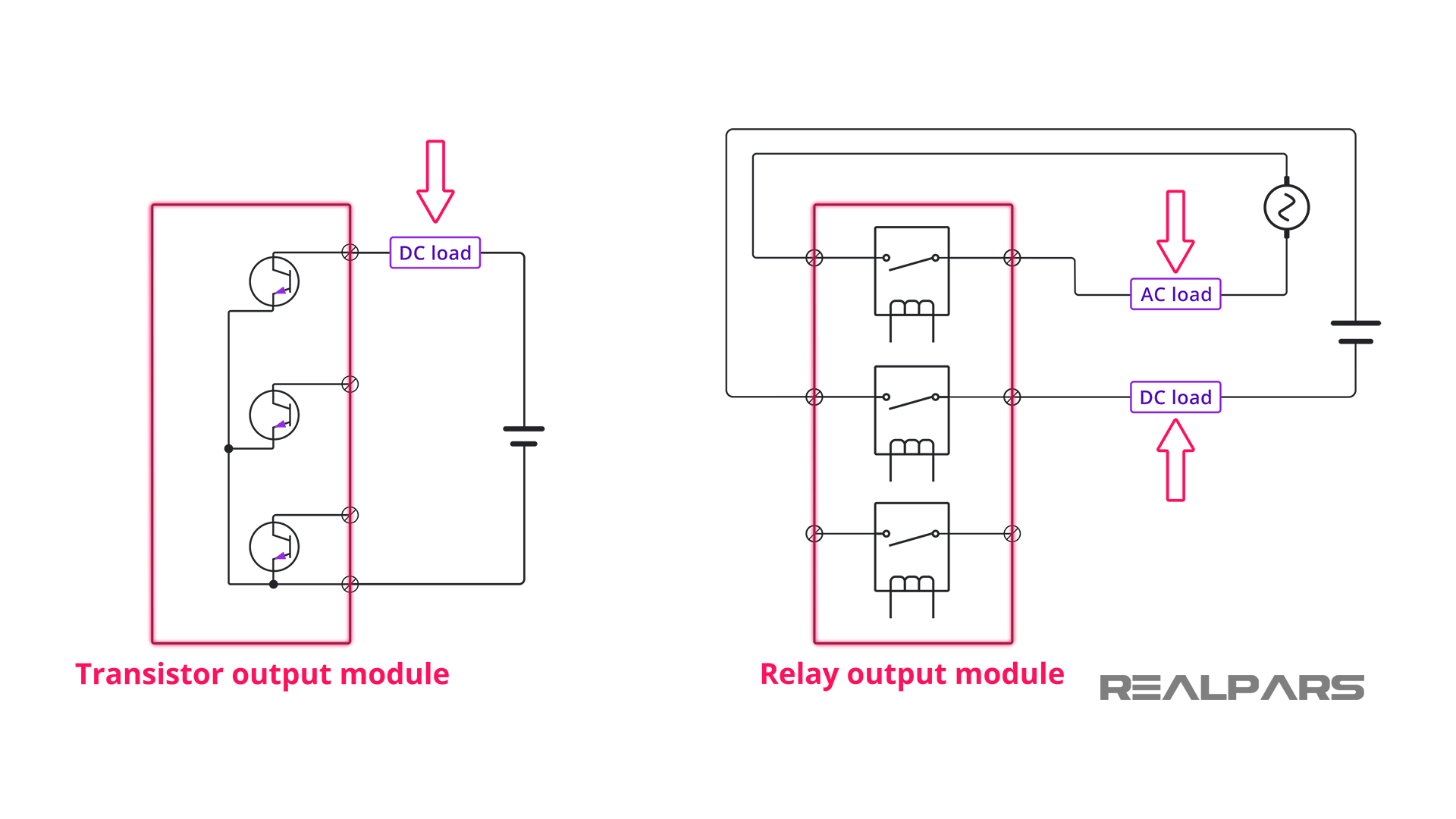
It’s important that the load power supply is connected with the correct polarity as the module can be either the Sinking type or Sourcing type.
Sinking and Sourcing are terms used to describe the load current flow relative to the output module.
We’ll take you through an in-depth explanation of Sinking and Sourcing in another article.
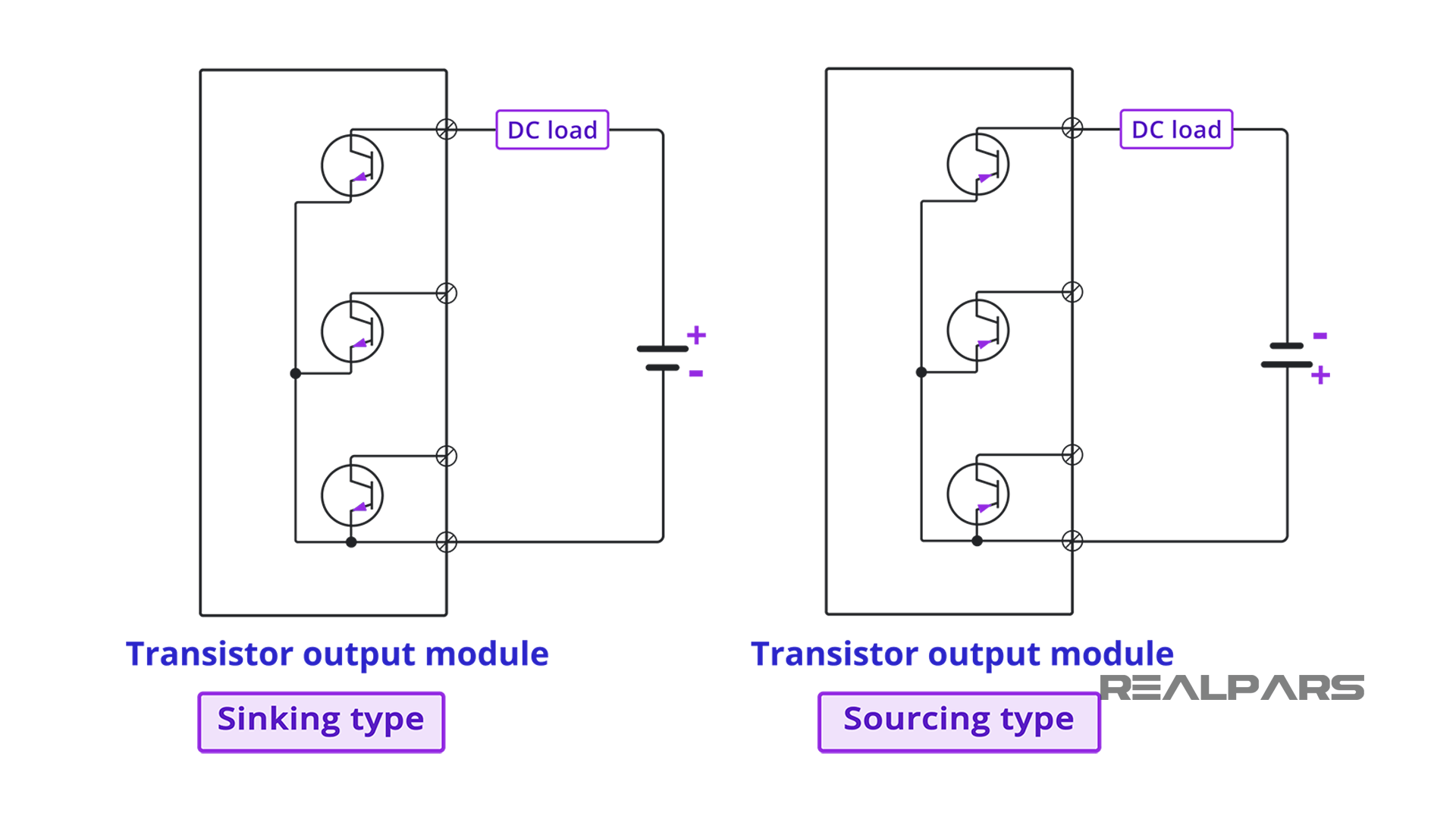
Siemens 6ES7322-1BP50-0AA0
The Siemens 6ES7322-1BP50-0AA0 is a 64 output Transistor Output Module. As with all transistor output modules, it can control DC loads only.
Let’s look at how one of the outputs operates. When the PLC signal is applied, the BJT will turn on and provide a current path for the load.
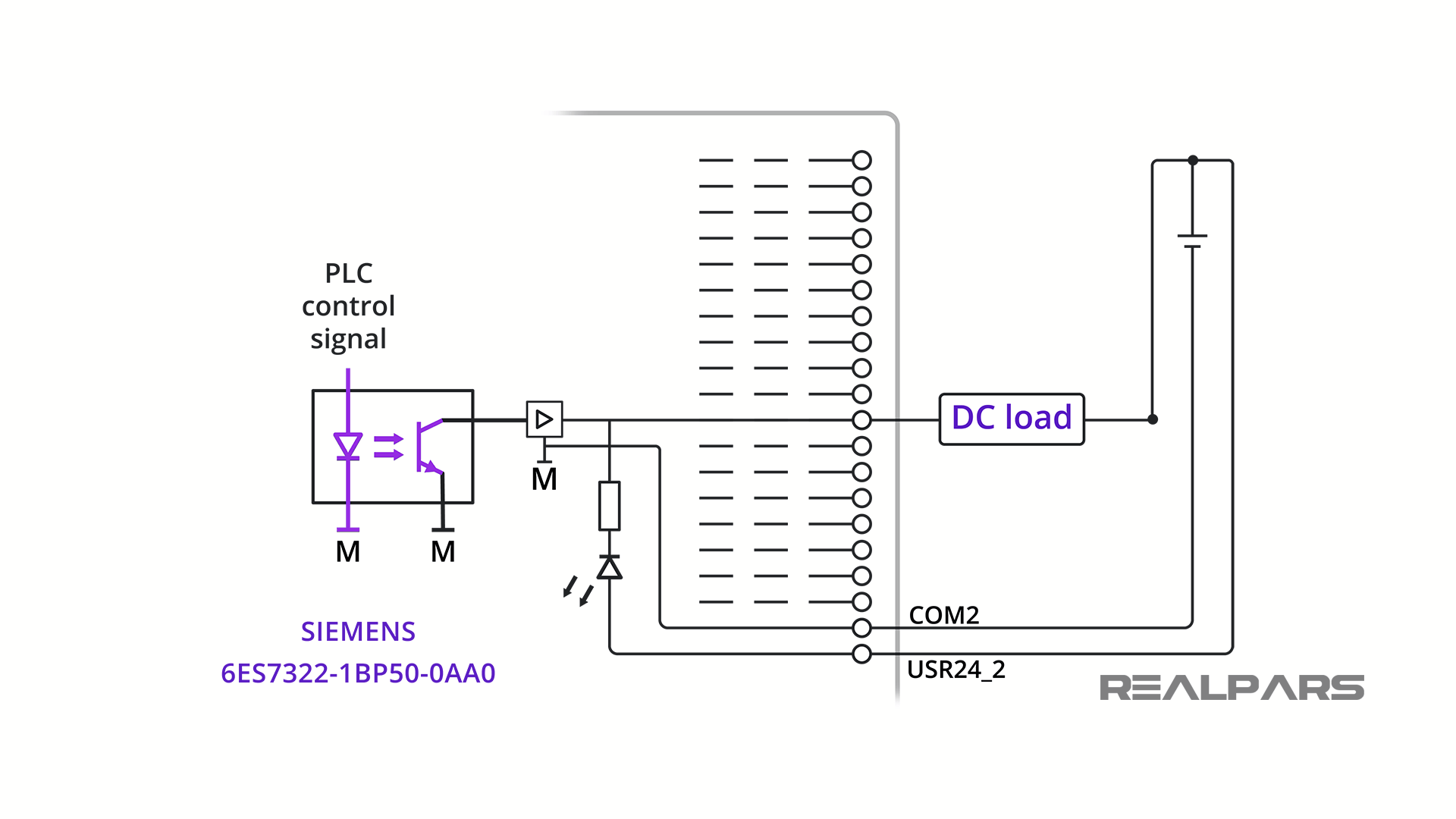
Phoenix Contact AXL SE DO 16/1
The Phoenix Contact AXL SE DO 16/1 is a 16 output Transistor Output Module. This module has additional features of Overload and Short Circuit protection of outputs and Peripheral voltage.
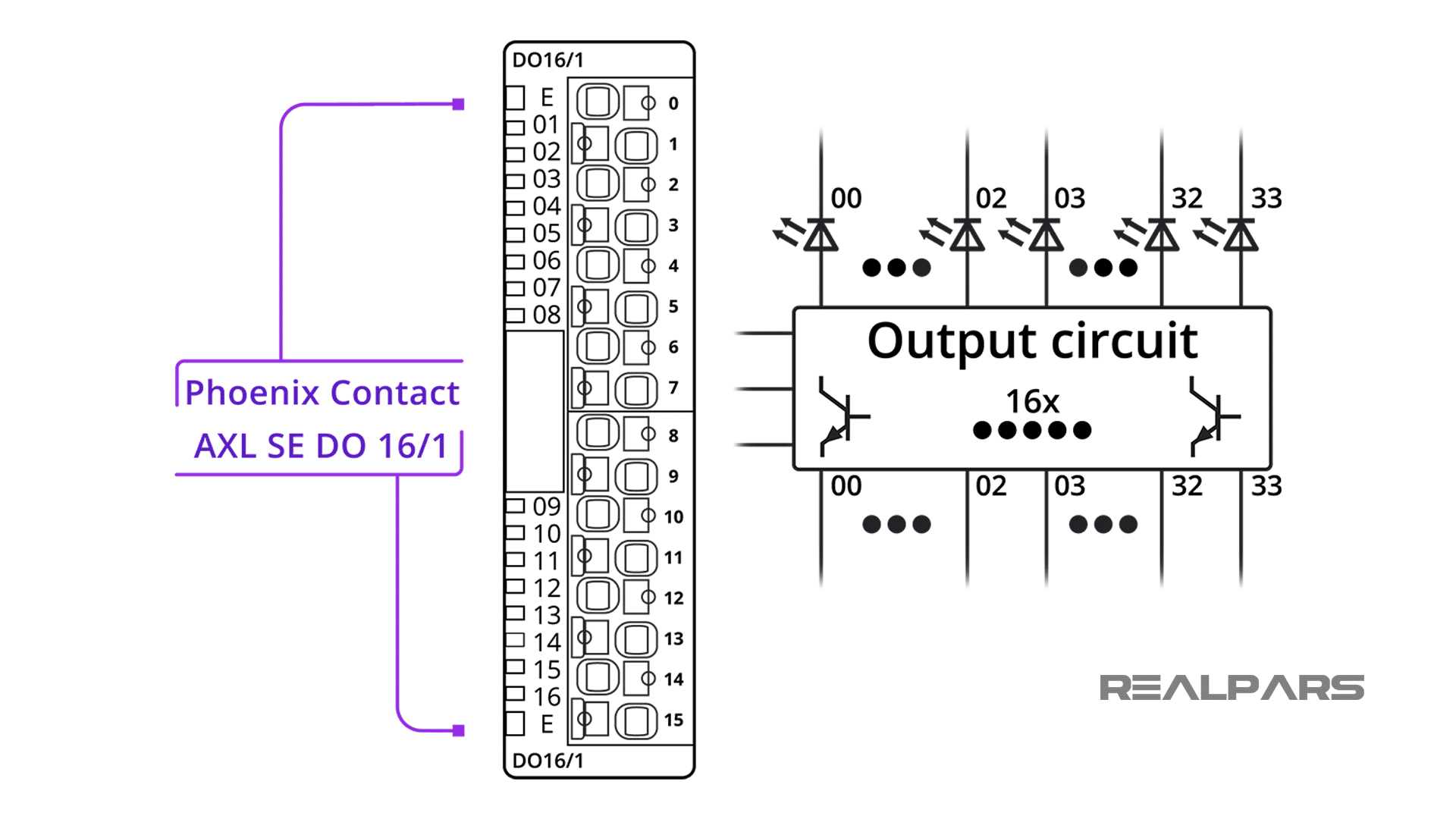
2-2) Triac output module
Siemens 6ES7522-5FF00-0AB0
The Siemens 6ES7522-5FF00-0AB0 is an 8 output Triac Output Module.
A Triac output module is capable of controlling AC loads where transistor output modules can control DC loads only. When the PLC signal is applied, the Triac will turn on and provide an alternating current path for the load.
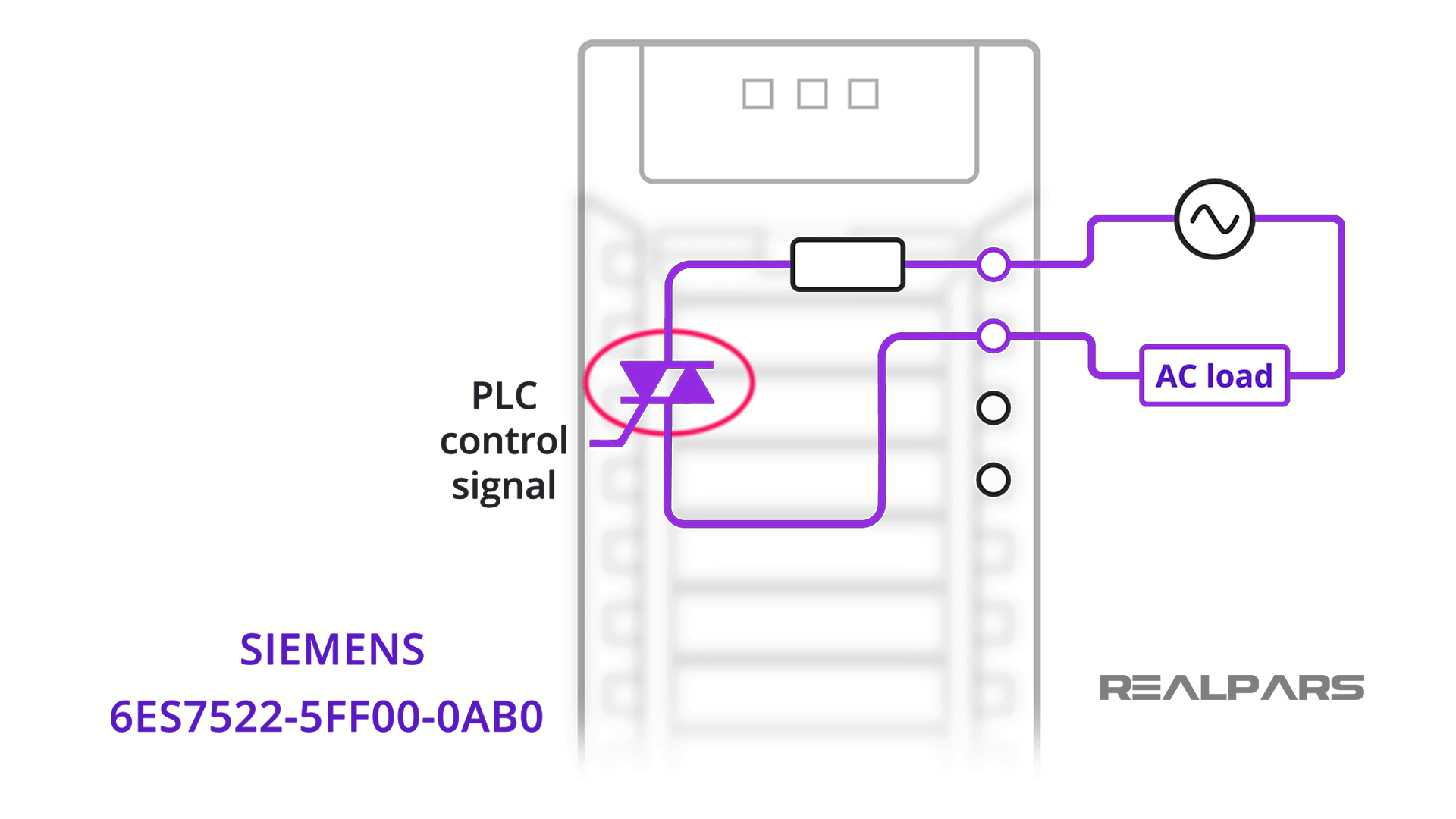
Output module comparisons
After exploring the operation of the relay and solid-state output modules, the obvious question is Which module is best for my application? Here are a few characteristics of each to help you make that decision.
Relay
– Relays generally have a higher current rating than transistors, but, as with any mechanical device, it will wear out with time.
– A relay module can operate AC or DC loads, or both.
– Relays provide electrical isolation between the load and the PLC.
– Relays are slow-acting with typical response times of 10 milliseconds or greater.
Closed relay contacts are almost zero ohms thus ensuring no voltage loss.
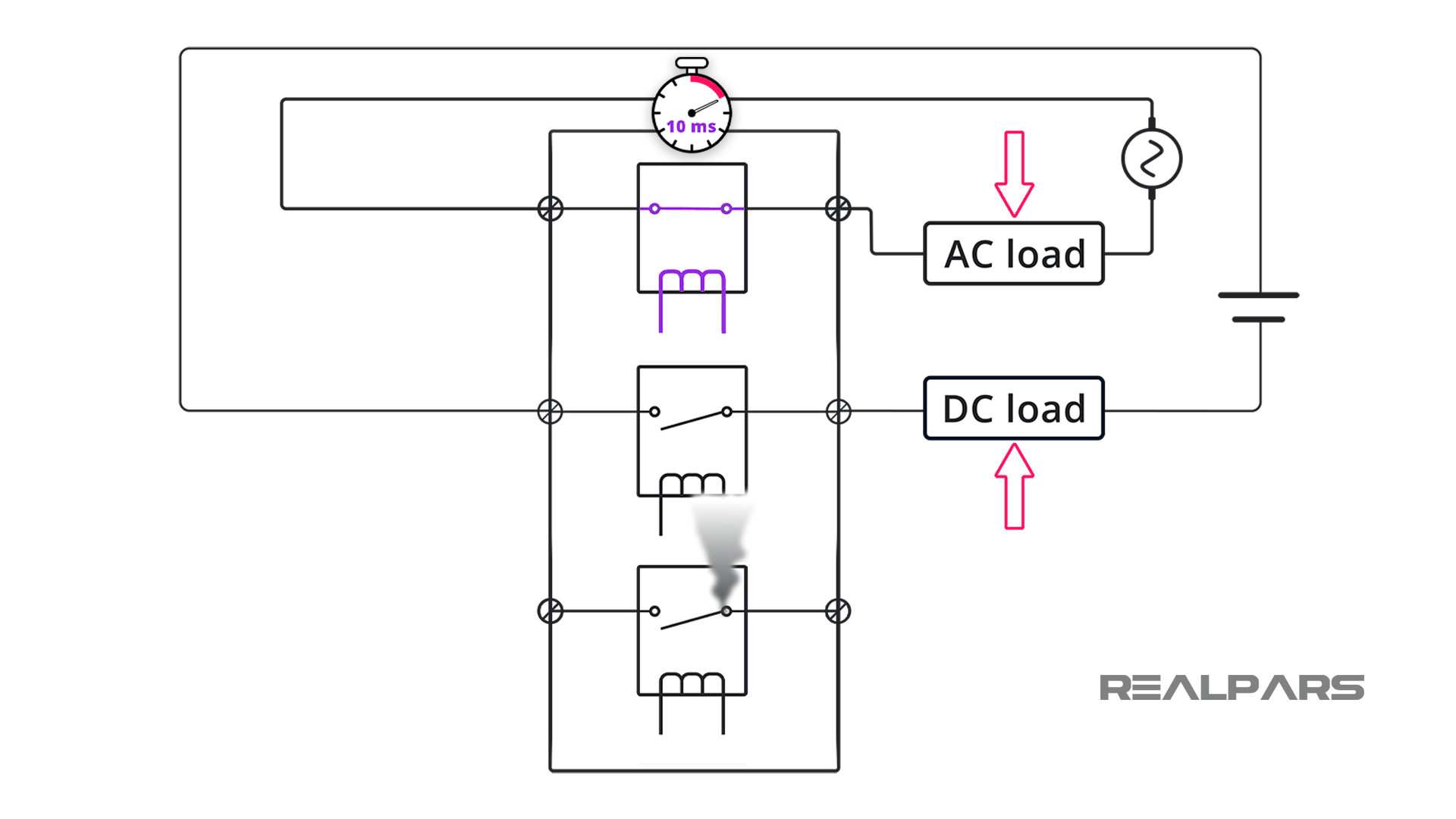
Transistor
– Transistor output modules are for DC applications only.
– Transistors typically cannot switch a large load current as can a relay.
– A transistor is fast because there are no mechanical parts. Their response time is much faster than relays.
– Because a transistor is not a perfect switch, there is always a small voltage drop across it when turned on.
– In some transistor modules, there is a leakage current even when turned off.
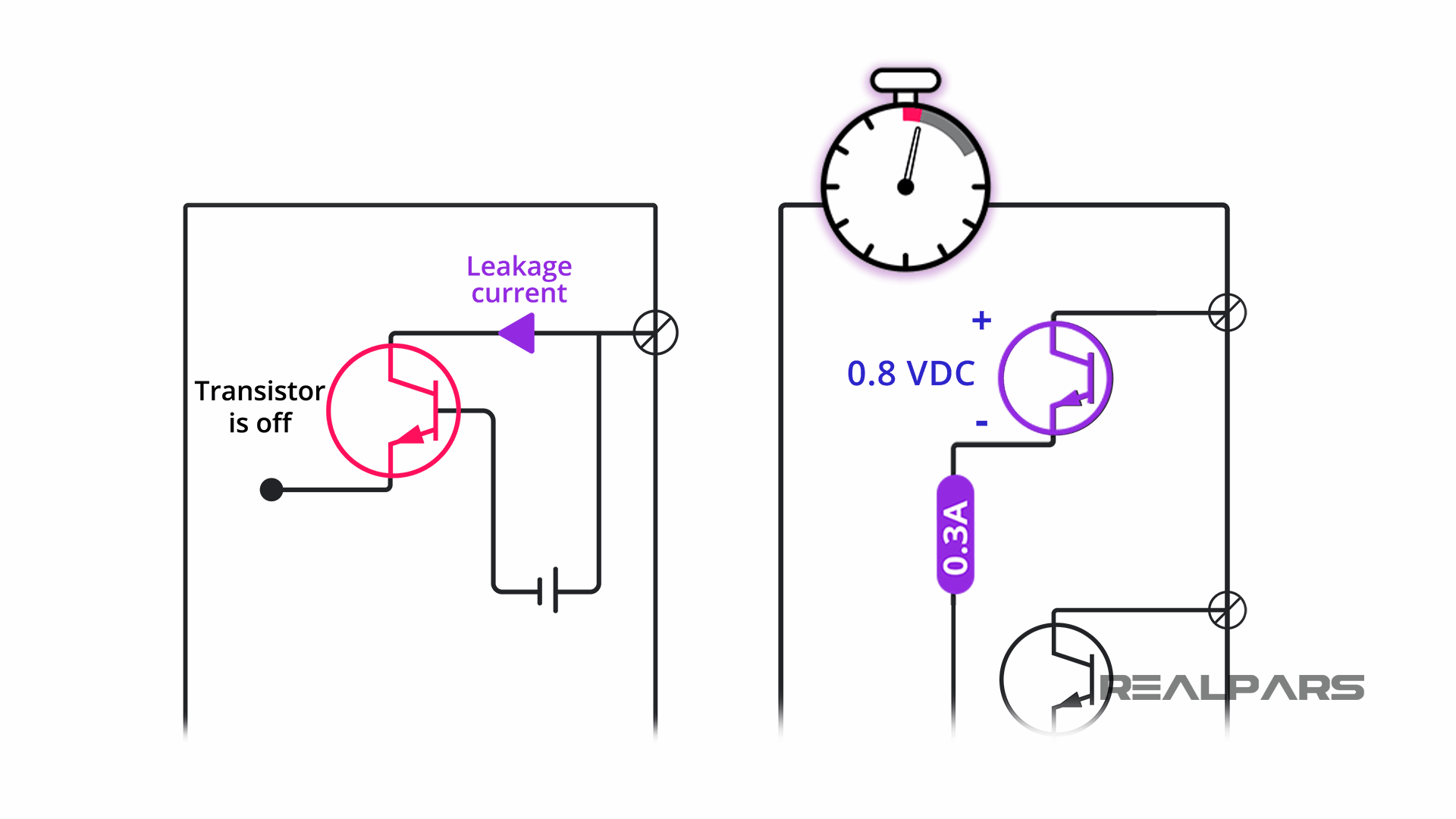
Triac
– A Triac output is used to control AC loads only.
– As with the transistor, a Triac is much faster than a relay.
– Triac outputs are suited to low power AC loads such as lighting, motor starters, and contactors with current ratings of around 1 amp.
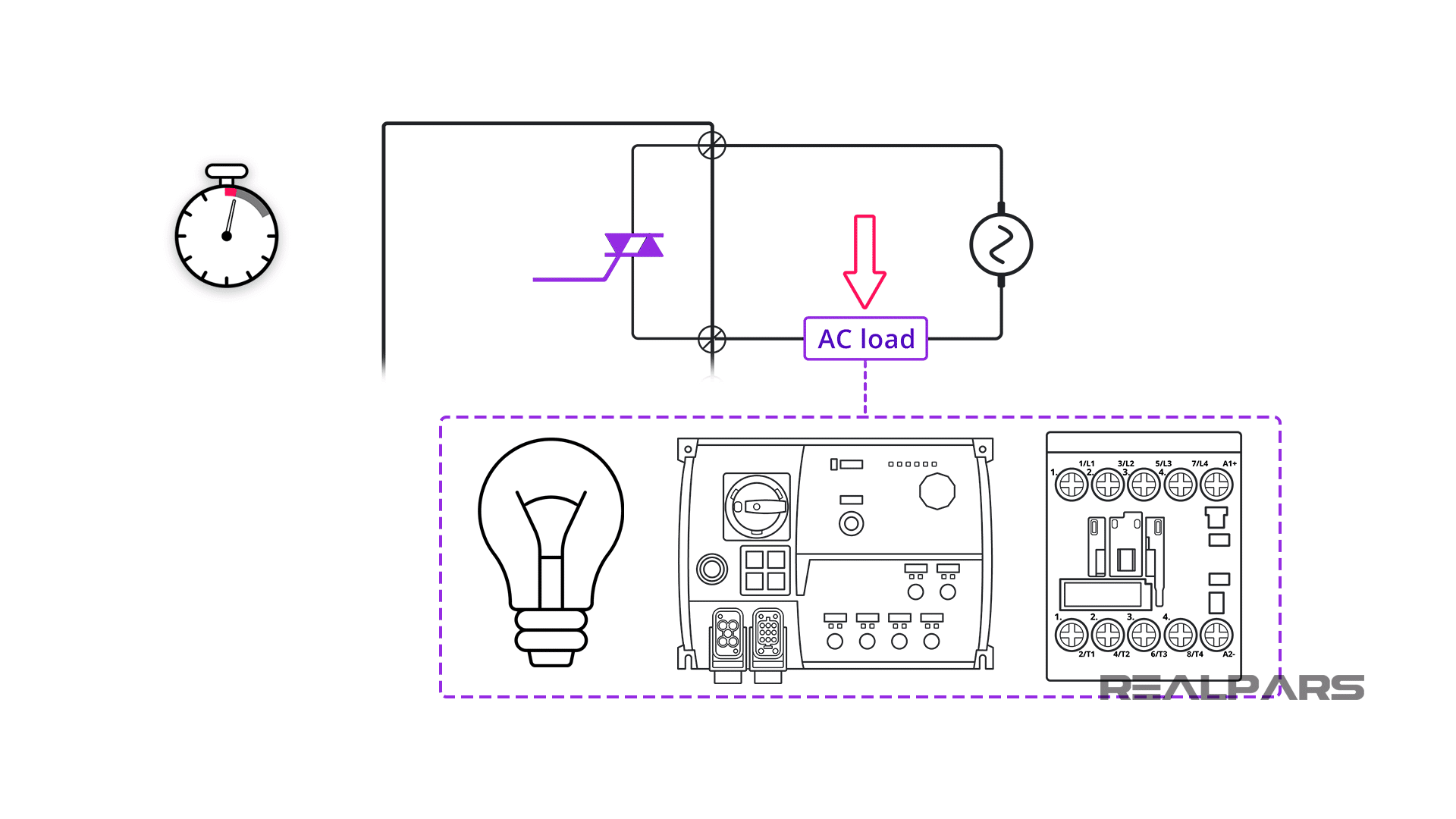
Summary
Ok,…let’s review what we’ve covered in this article
– The purpose of a PLC Output module is to operate or control a physical device based on field device conditions connected to an input module and decisions made by the PLC program.
– Digital or Discrete devices have only 2 possible conditions whereas Analog devices have an infinite number of possible conditions.
– There are 2 types of PLC Digital Output Modules – Solid State and Relay.
– Solid-state modules include Transistor and Triac types.
– Each module type has unique characteristics that need to be considered before choosing for the specific applications.
If you have any questions about the PLC Output module or about the PLC module in general, add them in the comments below and we will get back to you in less than 24 hours.
Got a friend, client, or colleague who could use some of this information? Please share this article.
The RealPars Team