In a previous article, I covered the ABCs of OPC Unified Architecture, or OPC-UA, and described how this TCP/IP-based protocol allows automation engineers to share data at the control system level in real time with high reliability and efficiency.
Now, I will present how OPC-UA can provide benefits to the pharmaceutical industry. Before I begin this OPC-UA case study, you might be wondering how you get up to speed on OPC-UA and more fully understand its benefits.
There is an amazing RealPars course, OPC-UA: Learn the Basics, that offers comprehensive lessons on this topic. Check it out.
Sensors
In the pharmaceutical industry, data is a key component of the manufacturing process. No matter where in the world the pharmaceutical manufacturing plant is located, there is a government body that regulates the process of delivering drug products to the marketplace.
Manufacturing data is critical to providing proof that good manufacturing practices were followed during the manufacturing process and that the composition and purity of the product meet the required parameters.
Gathering process data
How is process data gathered? As with any process, we install sensors in the process to provide critical data from the operation.
I will use a standard oral solids dosage process or OSD process, as an example. OSD processes are ones that take powdered ingredients, mix them, and press the mixture into tablets.
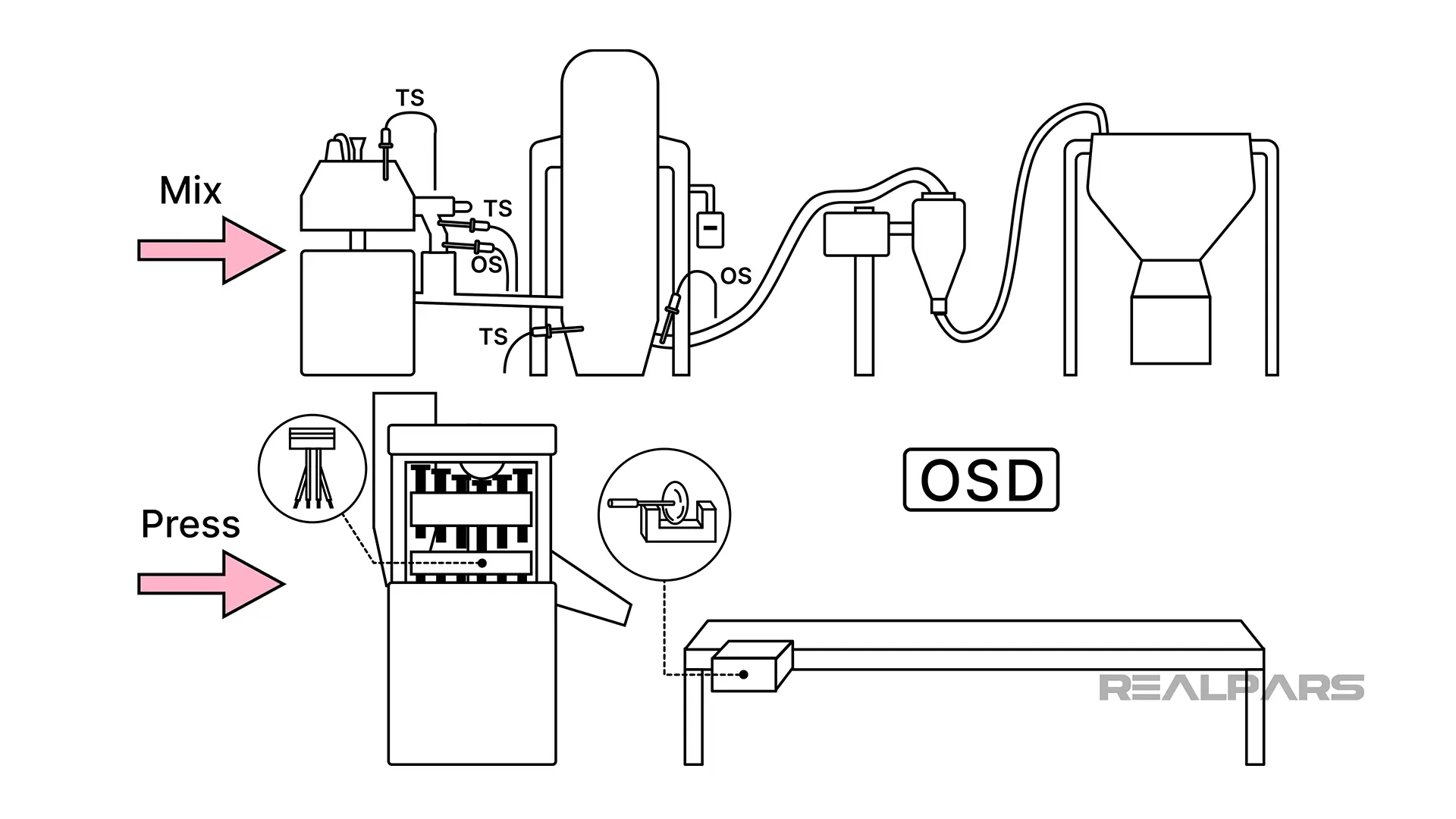
To paint a clearer picture of the OSD process, consider how we’re making a pill from powdered ingredients. It’s akin to baking, but instead for medicine. Initially, envision a sizable mixer, much like a dough mixer one might find in a bakery.
Into this, we pour the powdered ingredients, accompanied by a slight amount of liquid. This mixer, named the Rapid Mixer Granulator, combines everything until we attain a consistency similar to wet dough.
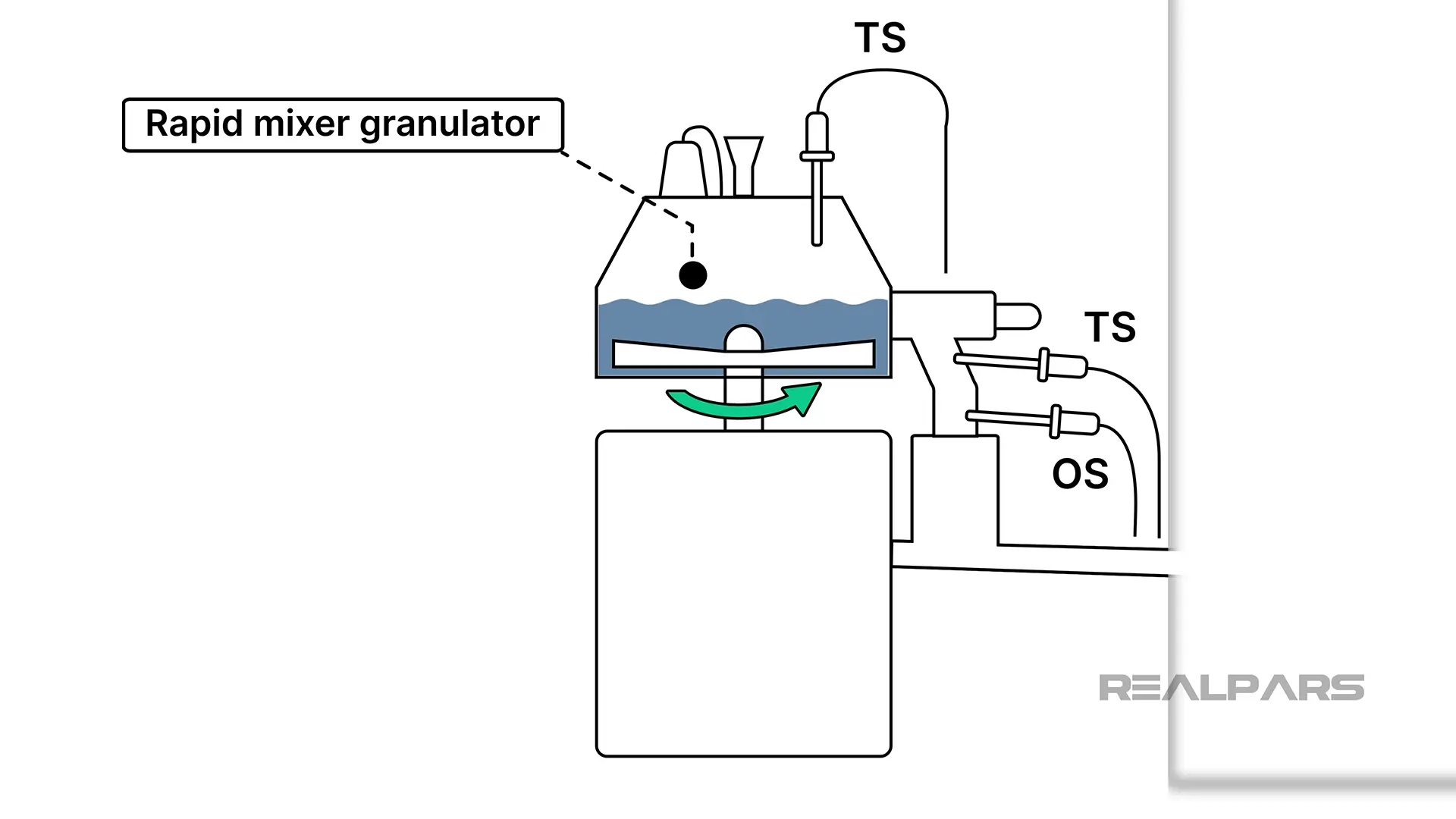
Subsequently, this wet dough requires drying. Picture it being transferred to a hefty drying apparatus, namely the Fluid Bed Dryer. After a set duration, we don't retrieve wet dough but minute, grainy fragments that resemble breadcrumbs.
These granules then undergo size uniformity checks, passing through the Cone Mill, a machine comparable to a monumental grinder, ensuring each grain is consistent in size.
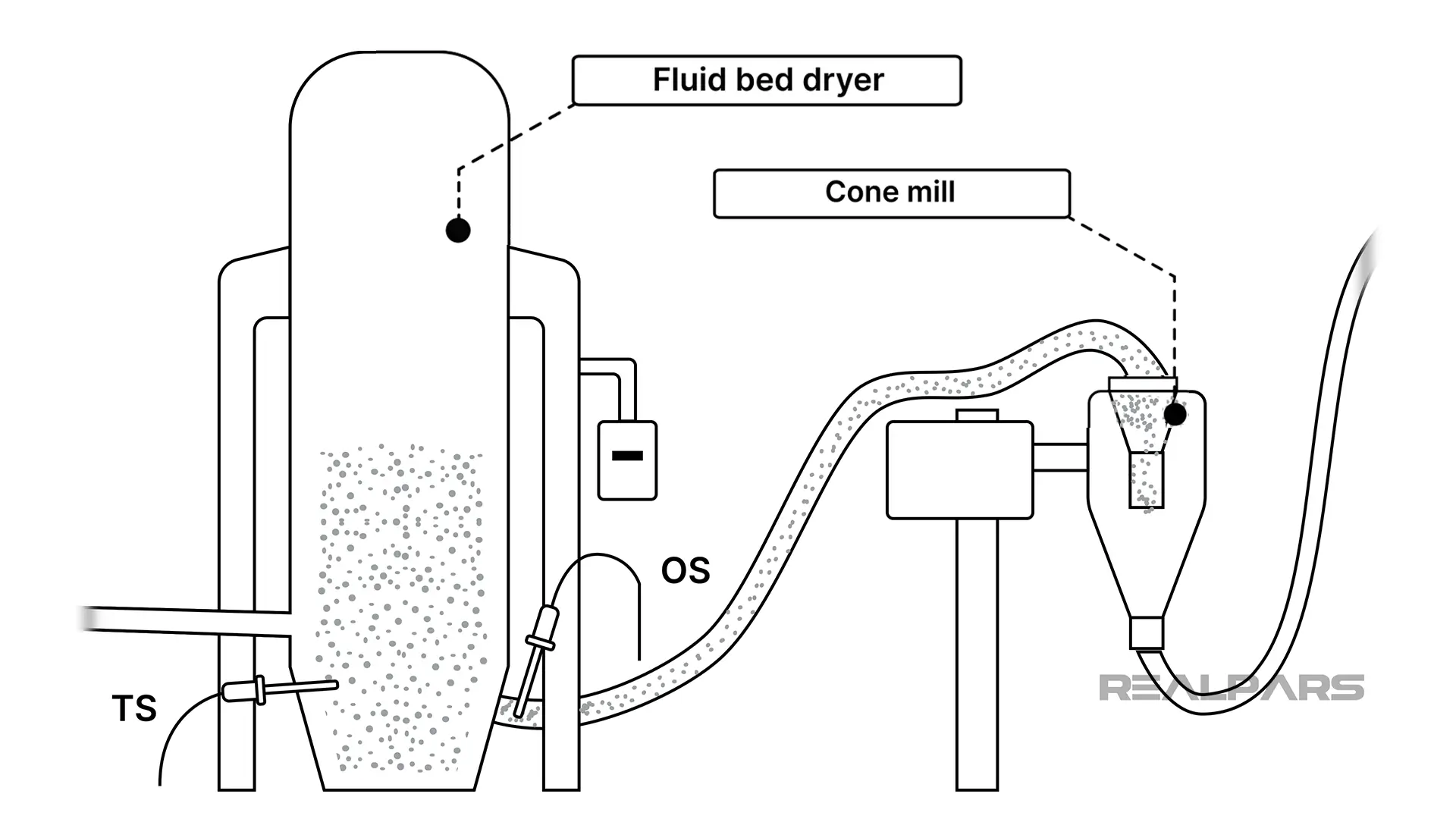
Concluding the process, we introduce the grains to the Octagonal Blender, reminiscent of a grand rotating mixer, ensuring thorough mixing of each grain.

Monitoring with specific sensors
The discussion of specific types of sensors in this type of process, along with detailed OPC-UA functionalities, will help provide an in-depth understanding for those who want to better understand the finer aspects of pharmaceutical pill manufacturing and monitoring.
To do this efficiently, we first need to have several sensors that monitor the manufacturing process.
- Resistance Temperature Detectors, called RTDs, or thermocouples, are often chosen for their precision in the narrow temperature bands typical for pharmaceutical processes. Monitoring pill-making temperature is vital as minor deviations can affect pill dissolution rates and efficacy.
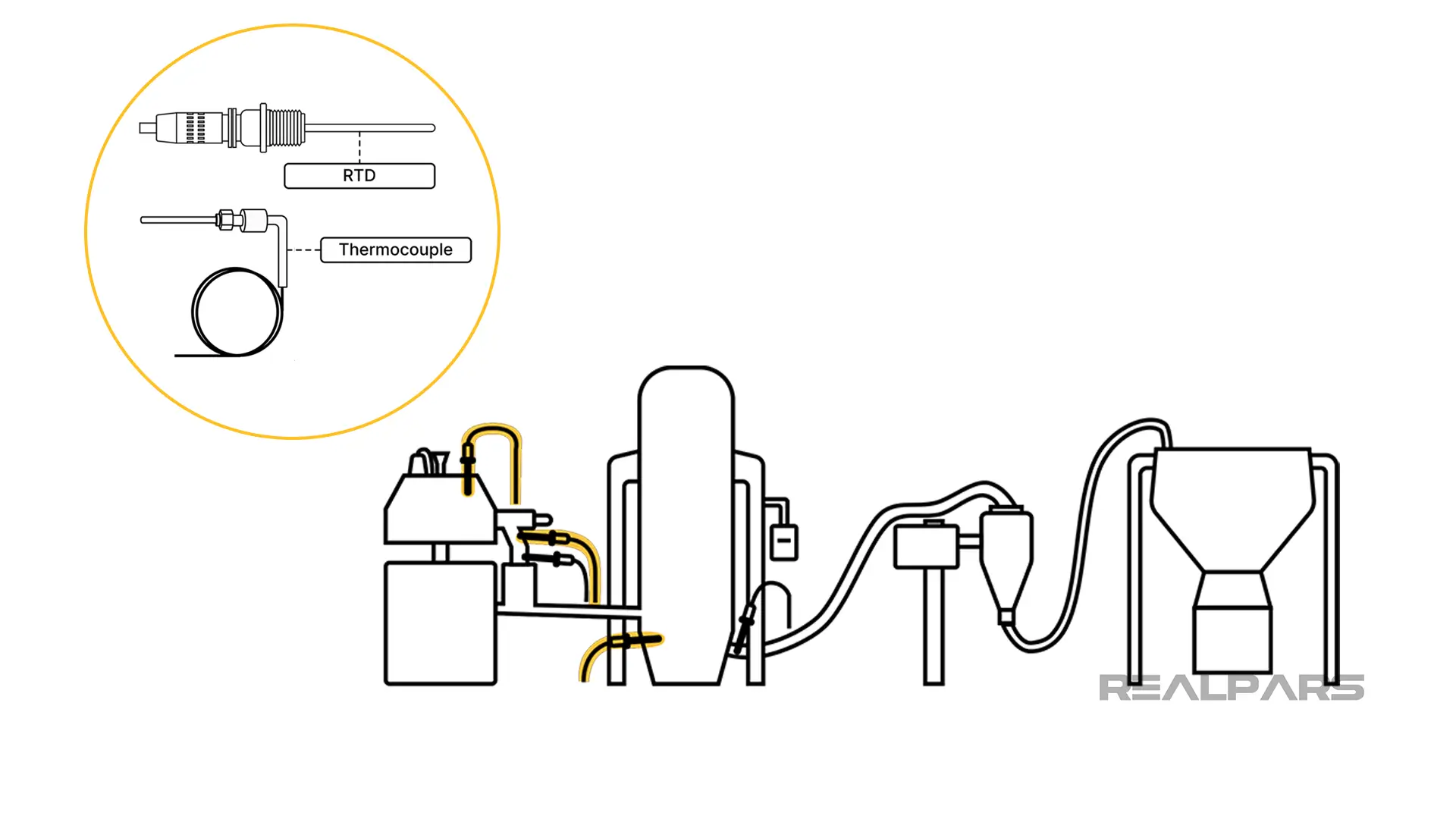
- Capacitive pressure sensors are commonly used for monitoring pill compaction in the tablet press. The correct pressure ensures that each pill has uniform consistency and does not break apart easily.
- Magnetic or optical encoders are installed on the product conveyor to monitor belt speed. The rate at which pills are delivered to the packaging line can affect production speed and efficiency.
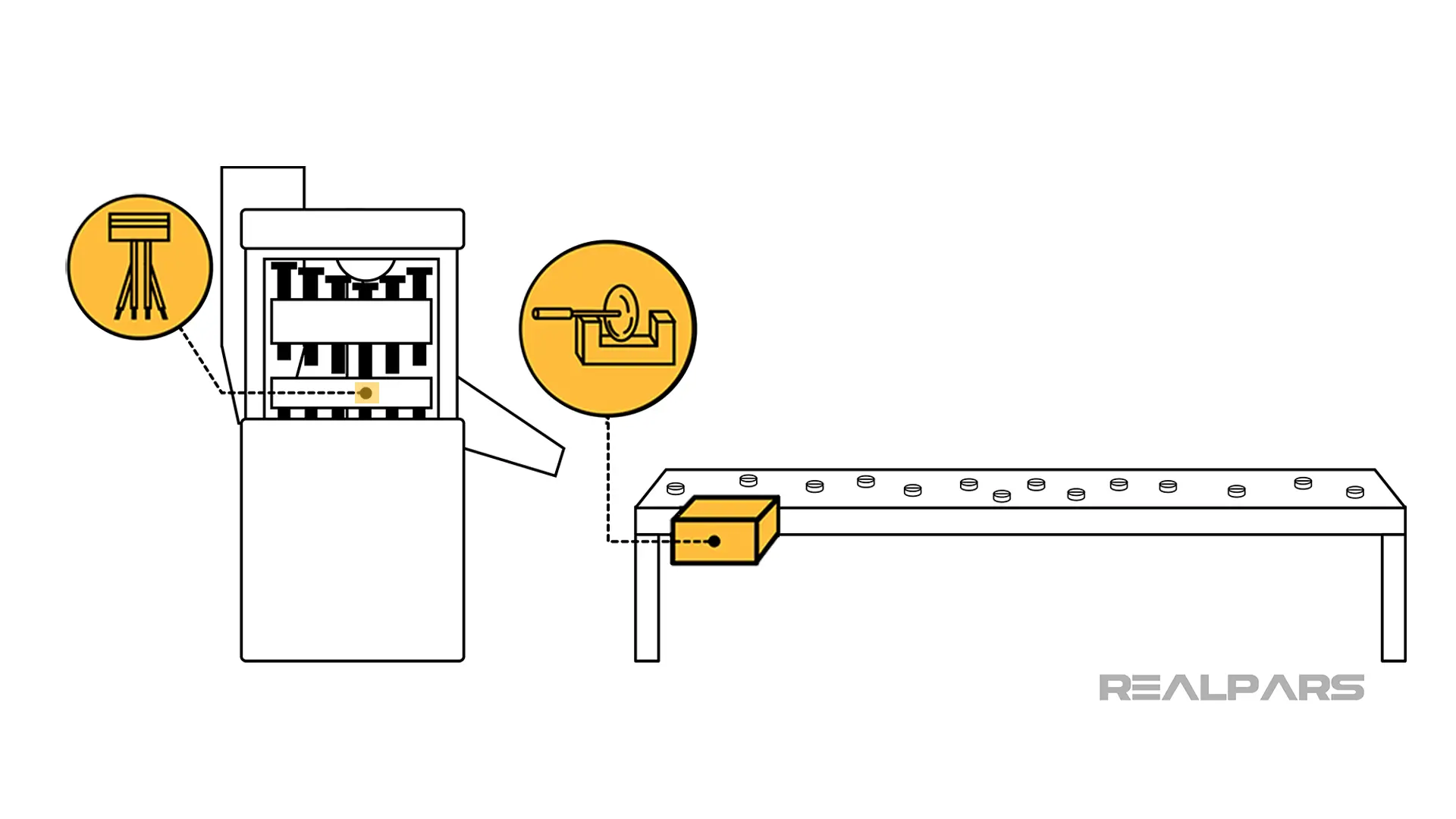
Quality assurance camera
Also of importance are optical sensors that can provide visual evidence of product quality. These cameras are the eyes of the operation.
High-resolution cameras equipped with infrared capabilities. Every pill can be rigorously compared against a standard using sophisticated image processing algorithms. From cracks to color mismatches, nothing slips past.
This is important because these cameras use high-resolution imaging, often combined with infrared capabilities to detect inconsistencies that are not visible to the naked eye.
With the pictures obtained, advanced image processing algorithms analyze each pill, comparing them against a predefined standard to identify anomalies.
Anomalies can range from cracks, incorrect coloring, size discrepancies, or even foreign particles.
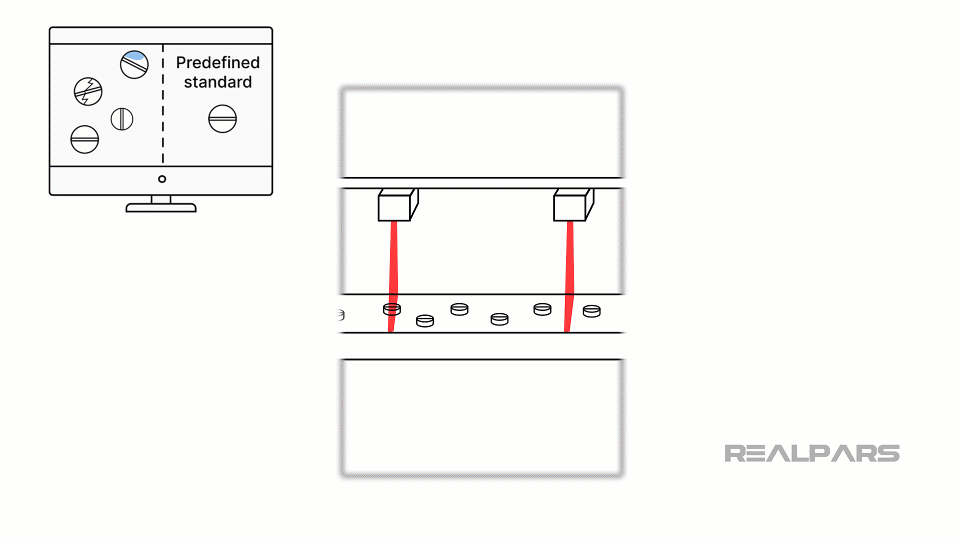
Process Analytical Technology sensors
Process analytical technology (or PAT) can be thought of as a mechanism to design, analyze, and control pharmaceutical manufacturing processes through the measurement of critical process parameters. These are key variables that affect the production process.
An example of a PAT sensor is based on near-infrared technology, which can penetrate through solid mixtures and provide feedback on how well-mixed the solids have become.
Uniformity of mixture is essential to ensure each pill has a uniform composition and can be relied upon to deliver the right amount of medication with each dose.
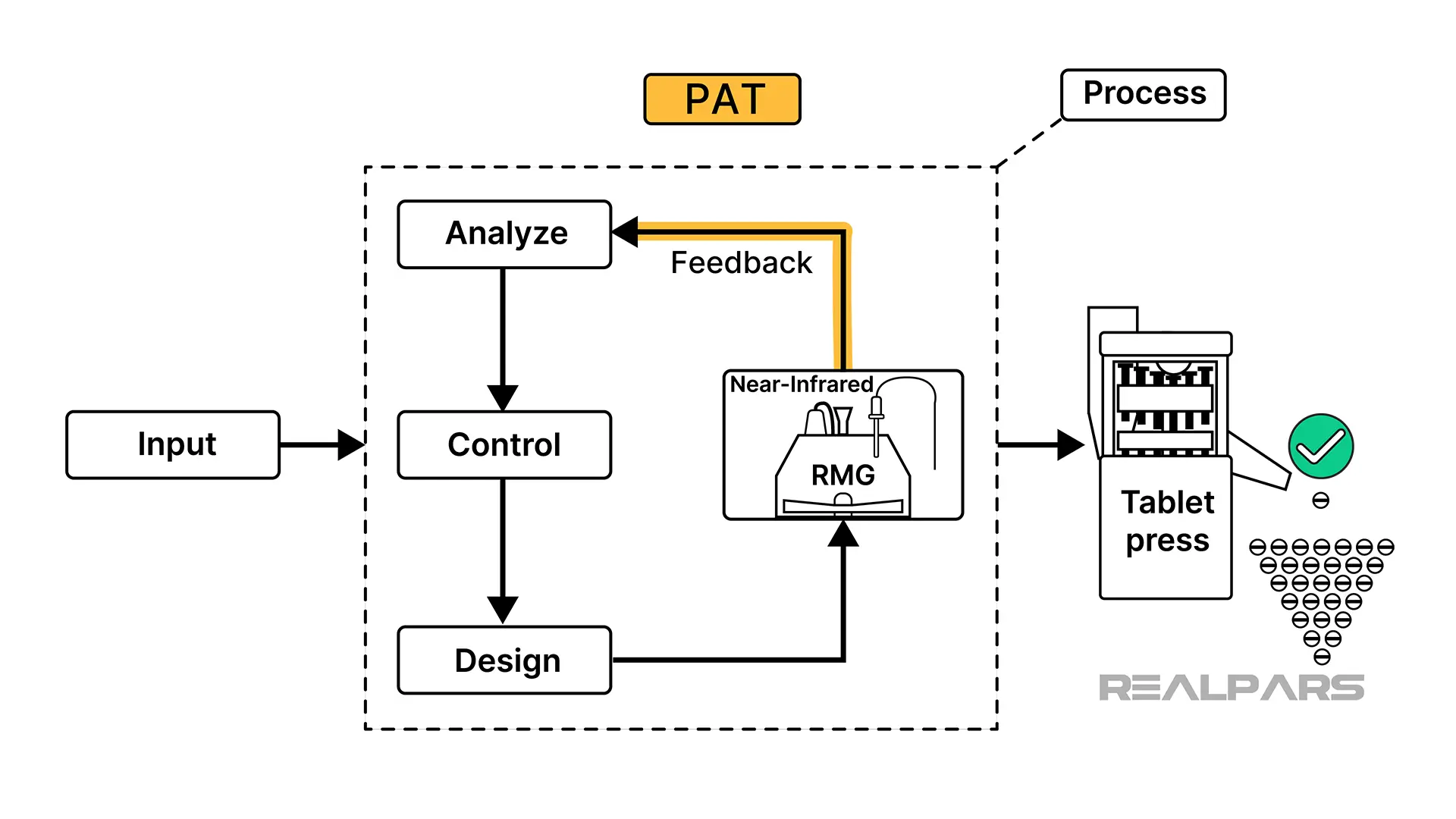
OPC-UA configuration
The sensors I described each have a specific purpose in the tablet-making process. Each provides data that is important to controlling the process, monitoring the process, and documenting how the product was manufactured.
In order to fulfill these needs, these data must be reliably, accurately, and completely accessible by the personnel and applications that need these data. This is where OPC-UA plays a big role.
Sensor data is collected in the manufacturing process by a number of computers, PLCs, and SCADA systems. In this typical architecture, important manufacturing data resides in various places.
In order to aggregate this data into a report, into a data historian, or in a computer that performs complex data analysis, there needs to be a fast, reliable way to move these data to the applications that need them.
The role of OPC-UA
In the digital realm, OPC-UA is the linchpin. OPC-UA is a machine-to-machine communication protocol used for industrial automation and provides a platform-independent protocol.
This means that applications on different computers or controllers, running different operating systems, can seamlessly share data over a common protocol.
OPC-UA allows the sampling of data at high frequencies, giving it the ability to capture every nuance of the production process in real time.
Given the proprietary nature of pharmaceutical processes, the stringent security measures that OPC-UA offers, ranging from data encryption to user authentication, are non-negotiable.
With OPC-UA's ability to support the continuous archiving and recalling of process data, every batch can be traced, which is critical should recalls be required.
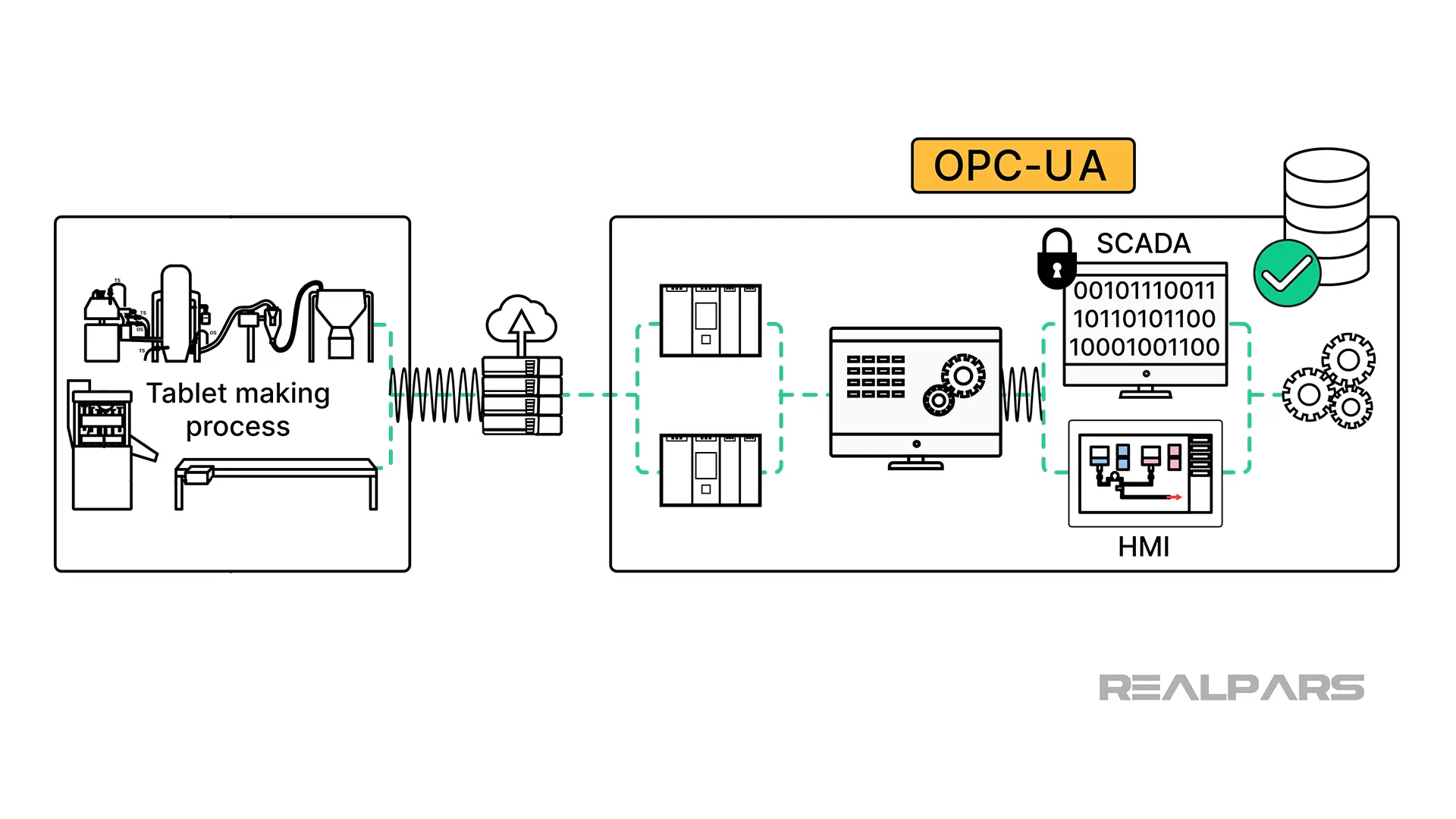
So what are the properties that make OPC-UA so valuable to the pharmaceutical industry? There are four important characteristics that make it so valuable. First OPC-UA has a configurable data communication rate.
In pharmaceuticals, rapid changes in conditions can quickly lead to significant batch wastage. Hence, high-frequency data sampling, as fast as 10 milliseconds, can be configured in the OPC-UA servers for these applications.
Second, as mentioned earlier, security measures are equally as important as data collection rates.
Due to the sensitive nature of pharmaceutical data, such as formulas and production rates, available OPC-UA security features like user authentication, encryption, and message signing are paramount. These measures also help support regulatory requirements for data integrity.
Third, for operational support, OPC-UA is set up to trigger alarms when data from sensors breach predetermined thresholds. This helps ensure timely intervention by operators.
Finally, OPC-UA provides extensive Historical Data Access support. OPC-UA is used in the process data archive tasks, which is crucial for batch traceability, especially in the event of product recalls.
Summary
To summarize, OPC-UA streamlines the pharmaceutical industry by ensuring interoperability, data integrity, and secure communication between diverse devices and systems, driving enhanced productivity and compliance in drug production and monitoring.
That concludes this case study of the benefits of employing OPC-UA in a pharmaceutical facility. If you're eager to dive deeper and truly master more of these OPC-UA concepts, don't forget to check out OPC-UA: Learn the Basics.
This course will provide you with a comprehensive understanding, along with practical exercises to solidify your knowledge.
Thank you for your time, and happy learning.