What is IO-Link?
Modern manufacturing companies understand the value of their data. They want to collect as much data from their machines and sensors as possible and analyze that data to optimize their processes and operations.
Unfortunately, many sensors communicate with controllers using simple analog or digital signals, making it impossible to retrieve more data from them.
Although these sensors could be replaced by intelligent sensors that communicate over an industrial network like EtherNet/IP, the cost associated with replacing all of the sensors in a factory is too high for manufacturing companies to consider.
IO-Link offers a solution to this problem.
IO-Link is a digital communication standard that can replace analog communication between a sensor and an IO block.
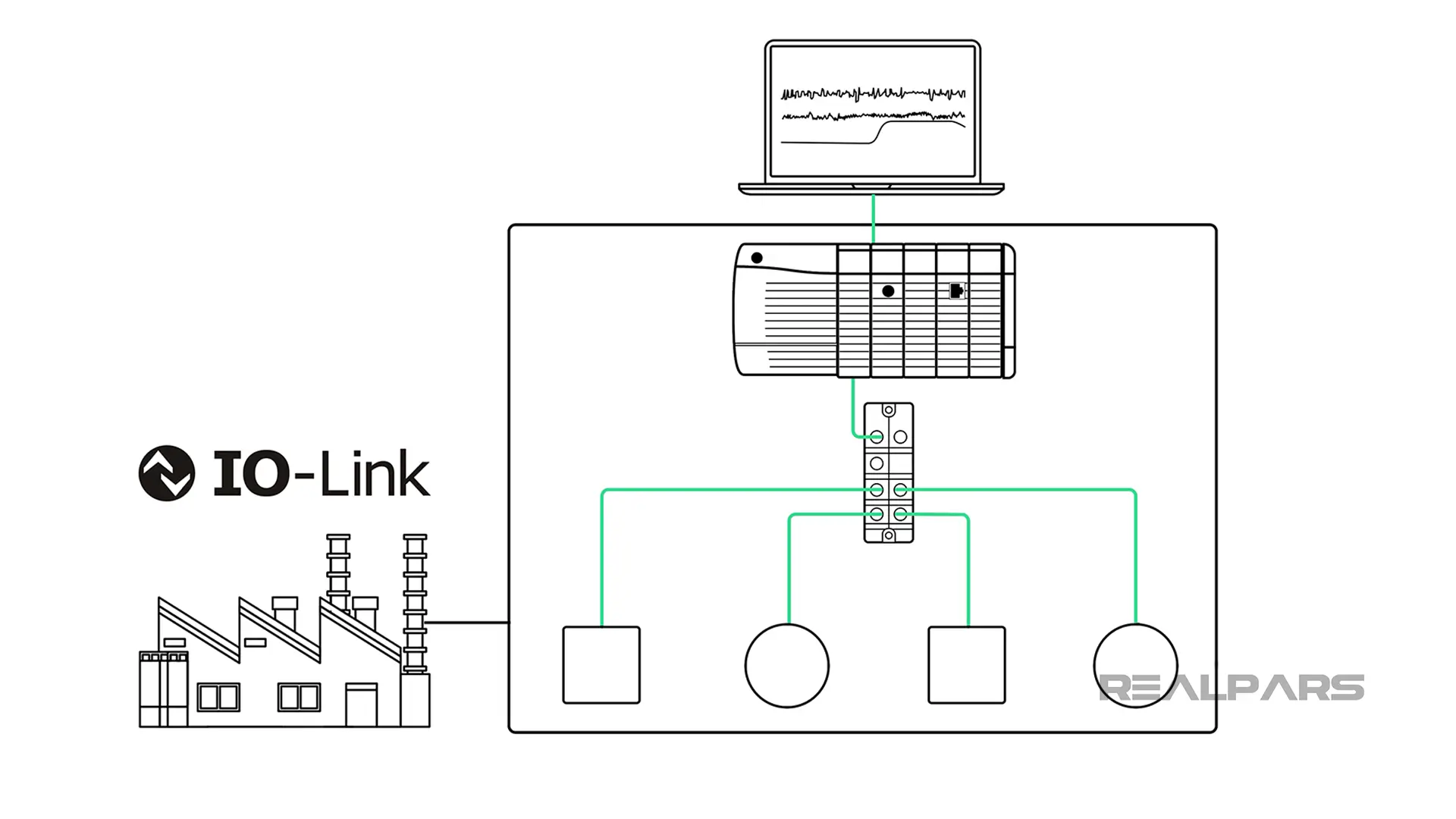
Since IO-Link is a digital communication standard, more information can be exchanged on a single cable, making it possible for companies to collect more data from sensors using their existing infrastructure.
By replacing their existing IO block with an IO-Link IO block, companies can;
- Collect more data from sensors including diagnostic data and multiple process values,
- Collect data from sensors in meaningful units like millimeters, leading to less time spent converting electrical signals to engineering units and more accurate readings from sensors.
IO-Link is basically a low-cost route to Industry 4.0 and data-driven decision-making for companies that want to collect more data without overhauling their existing infrastructure.
In this article, we’ll look at an example of IO-Link being applied in an application to see the benefits of IO-Link.
If you want to learn more about IO-Link, then I suggest that you check out our course IO-Link Essentials: Accelerating Towards Industry 4.0.
Application
A Hydraulic Pressure Unit, also known as an HPU, is a machine that pressurizes fluid so that it can perform heavy lifting.
By converting the movement of liquid into a mechanical force, HPUs are used to pull cars out of canyons, move massive volumes of earth, and lift giant trees.
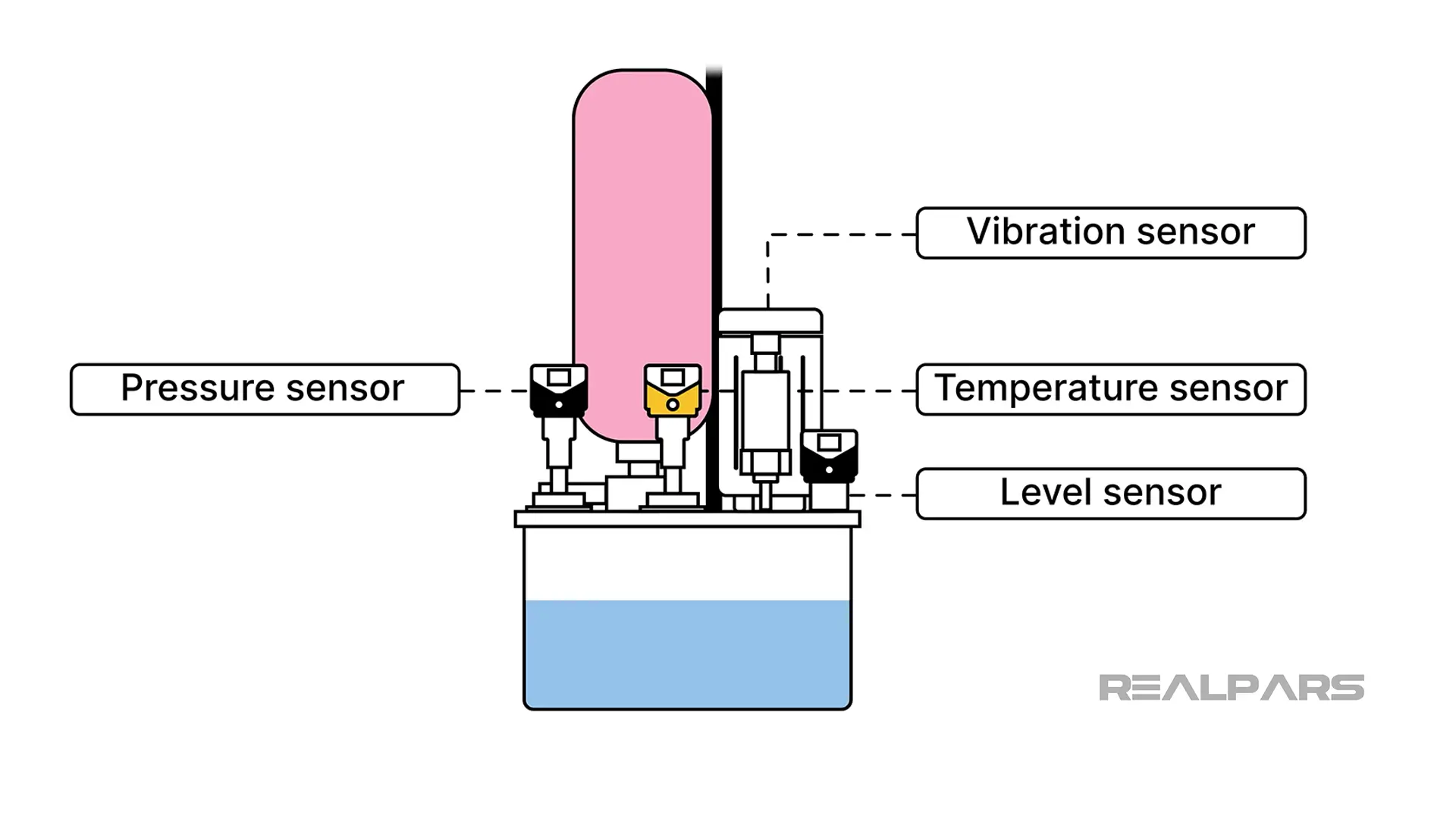
A traditional HPU is equipped with several process sensors that monitor the flow, vibration, pressure, and level in the HPU and send their data back to a controller using analog signals in a range of 4 - 20 milliamps.
By connecting these sensors to an ifm IO-Link Master, machine builders, and end users can unlock the data from the machine to optimize processes and ease engineering, commissioning, and maintenance of their machines.
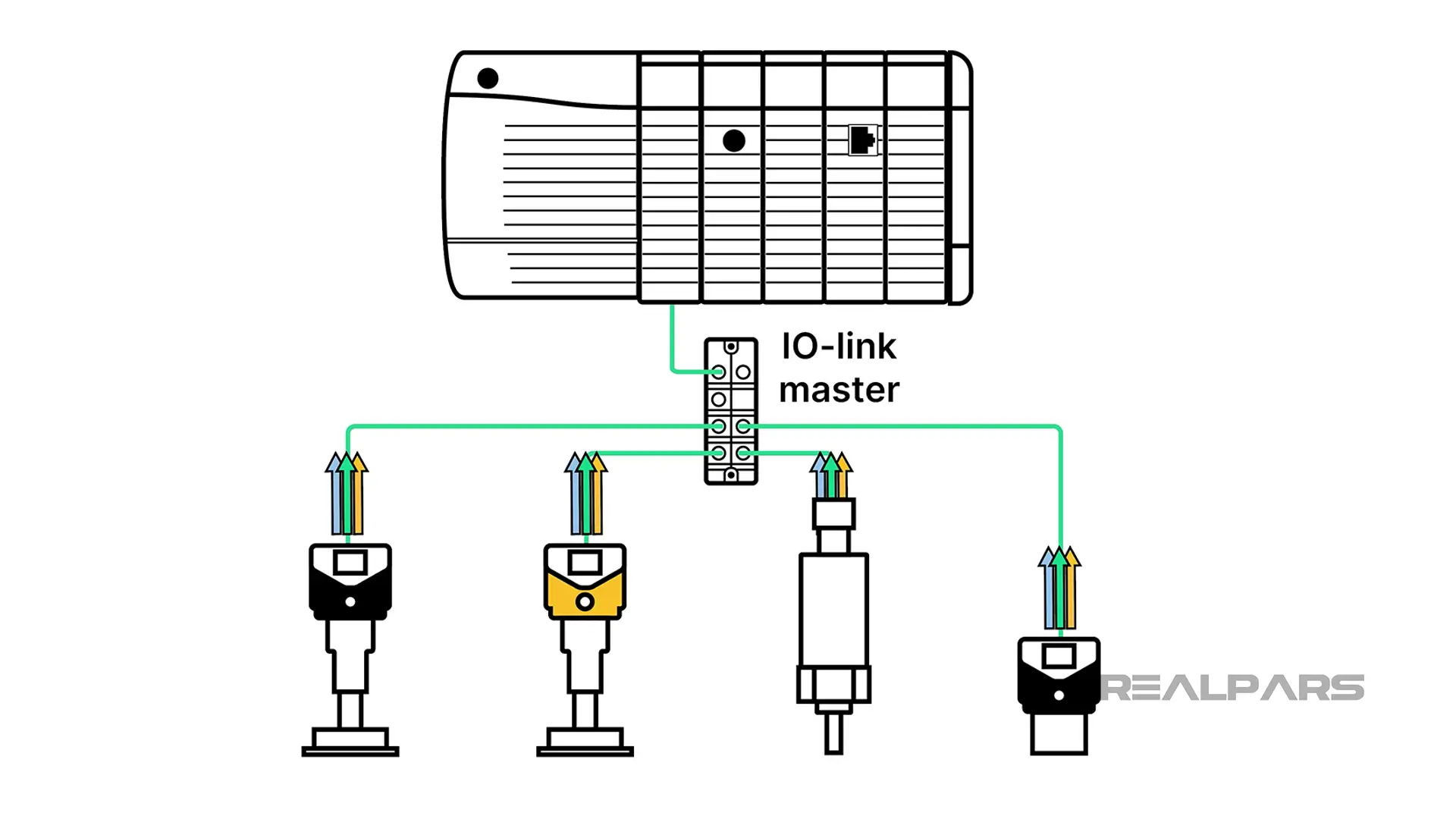
Let’s see how.
Optimization
When you are using a traditional analog sensor to measure a process value, the sensor only sends one process value back to the PLC as an analog signal. This signal must be scaled to a meaningful value and there is no way to retrieve more data like operating hours from the sensor.
By using IO-Link, you can unlock the data from these sensors.
With IO-Link, process data is sent from the sensor to the controller using a digital signal in an engineering unit. This eliminates the need to convert and scale the value in the controller and the effect of electrical noise, leading to more accurate readings and less overhead in the controller.
Since IO-Link is a digital communication standard, more data can be sent over a single wire than ever before. Sensors can send multiple process values to the controller as well as diagnostic information.
With ifm’s DataLine IO-Link Masters, this additional data can be sent from the IO-Link Master directly to the cloud via the dedicated IIoT port where it can be analyzed using IT tools and machine-learning algorithms to uncover real insights that optimize processes and operations.
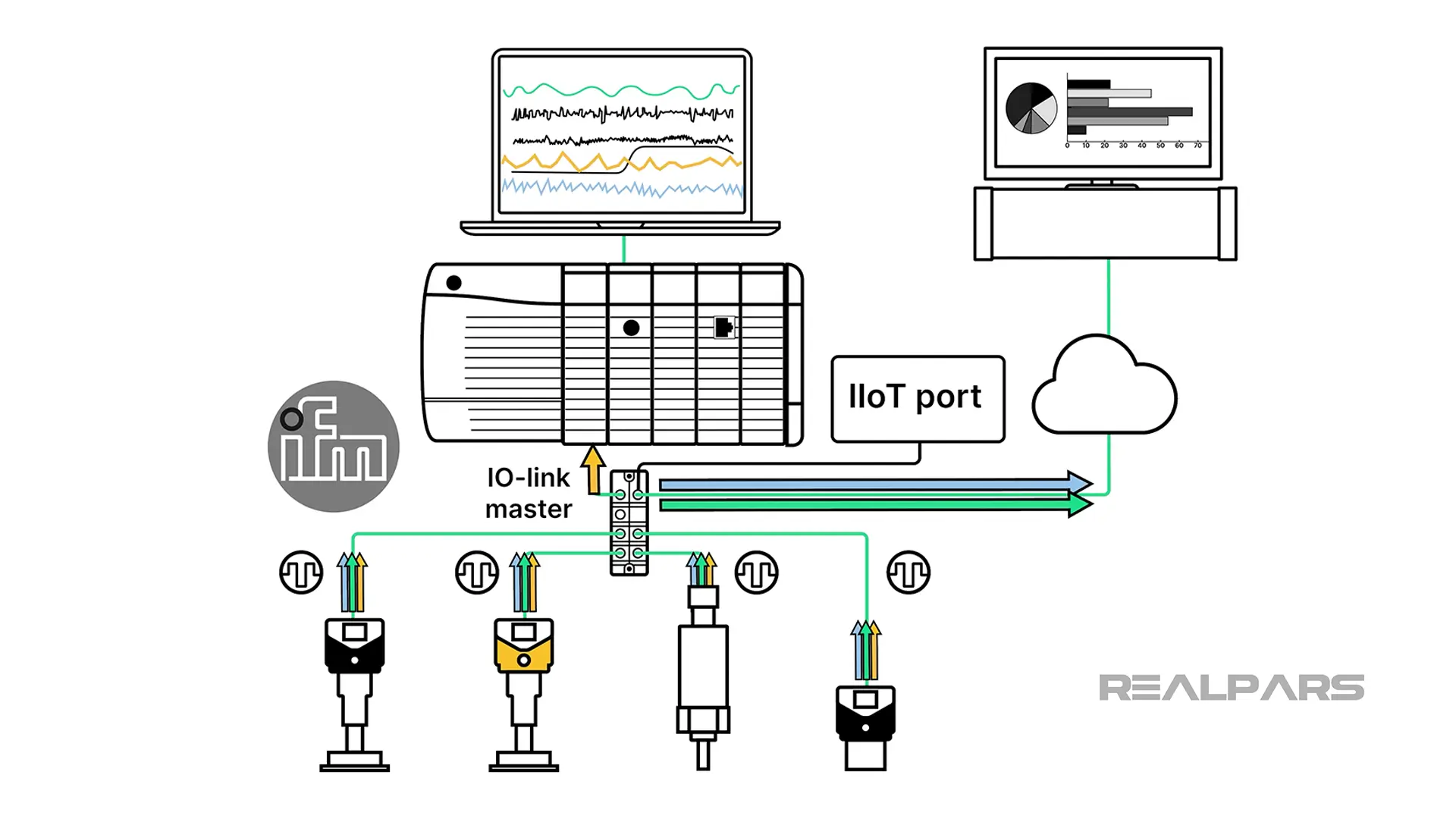
Engineering
IO-Link also helps to streamline the engineering and commissioning of machines.
Since IO-Link unlocks the intelligence of sensors, less work has to be done programming controllers.
IO-Link sensors send process values to the controller in an engineering unit so control engineers no longer need to spend time scaling values in the controller.
IO-Link sensors can also send high and low-level alarms which further reduces the amount of programming required in the controller.
Finally, ifm provides IO-Link Startup Packages that contain everything you need to integrate an IO-Link sensor into your controls application including device descriptions and add-on instructions that can be imported into your projects.
With Startup Packages, you can integrate IO-Link devices into your projects without writing a single line of code.
Commissioning
Using moneo configure, ifm’s IO-Link configuration software, you can save machine configurations as a parameter set. Since a parameter set can include multiple masters and sensors, the full configuration for a standard machine can be stored.
During commissioning, a pre-validated parameter set can be downloaded to the machine enabling one-click commissioning of new machines.
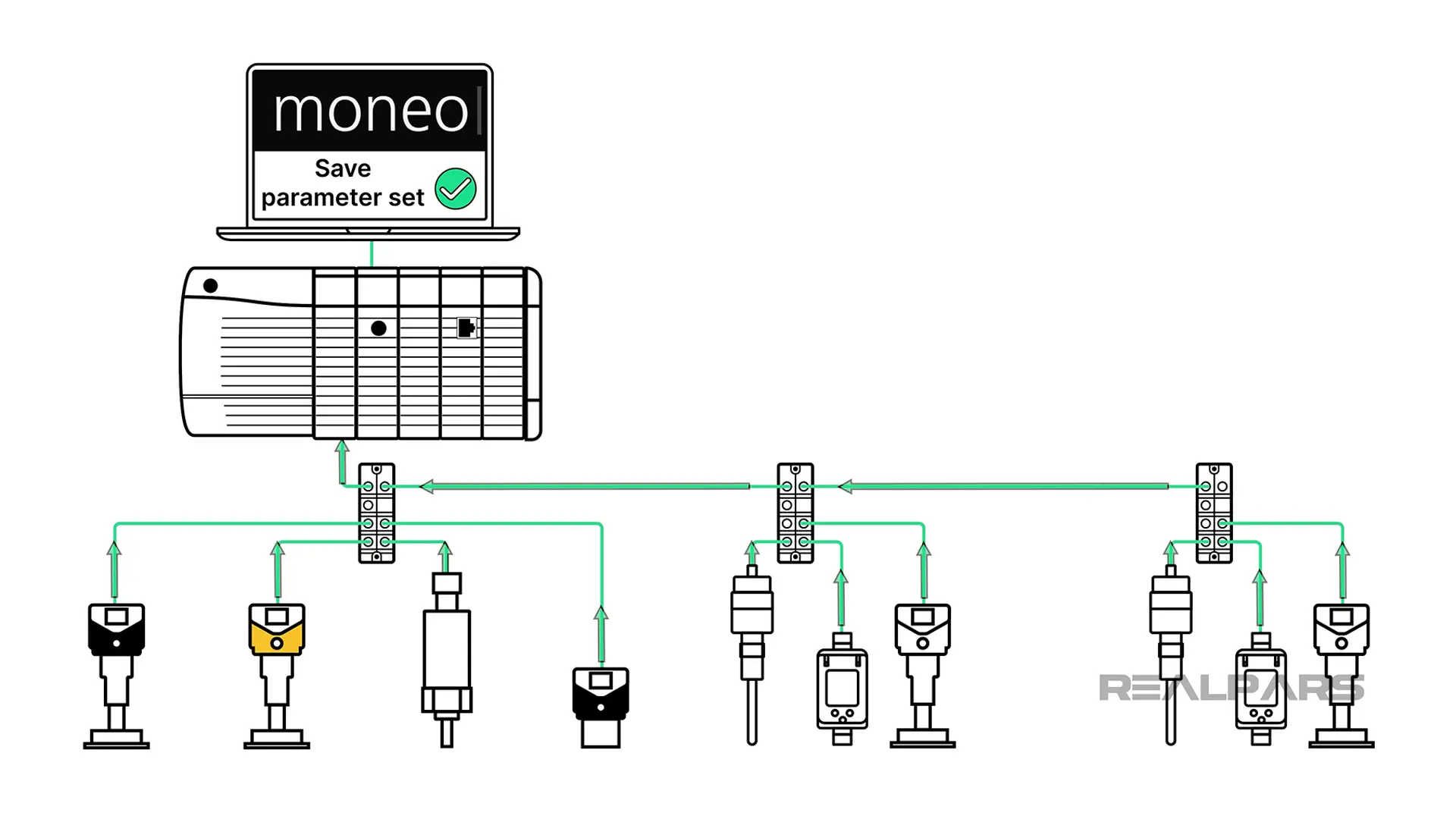
Maintenance
IO-Link makes more diagnostic data available from sensors to unlock the ability of maintenance departments to perform real predictive maintenance. When a sensor starts to fail, maintenance activities can be planned for the next convenient downtime.
IO-Link also makes maintenance easy through its Automated Device Replacement functionality. With ADR, the configuration for each device connected to an IO-Link Master is stored in the IO-Link Master.
When a broken sensor is replaced, the configuration is automatically downloaded to the new device.
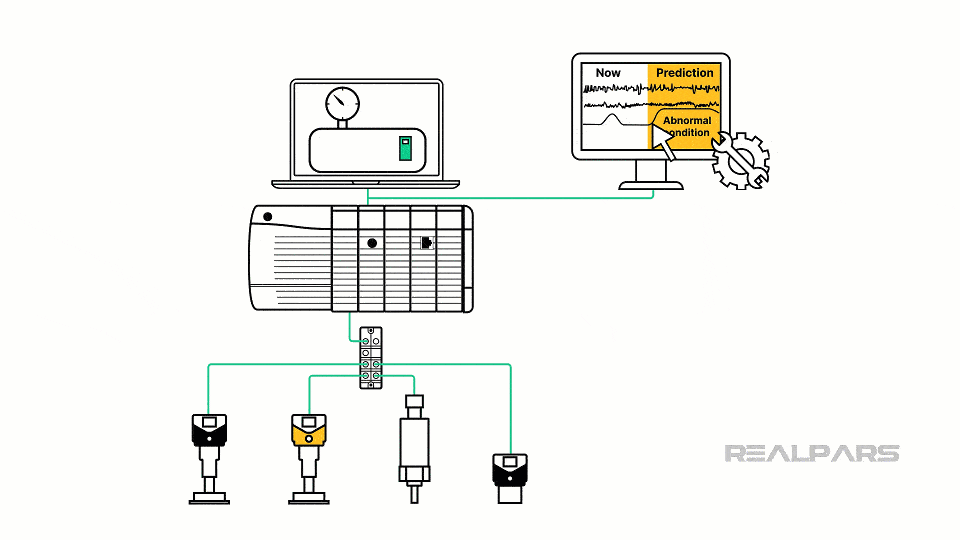
For maintenance technicians, this means no more searching for configuration files at 2 am while a production manager puts you under pressure to get the line running.
Wrap-Up
As you can see, IO-Link offers a cost-effective way for companies to unlock the data from their sensors using their existing infrastructure. This leads to real benefits for process engineers, controls engineers, commissioning engineers, and maintenance technicians.
If you would like to learn more about how to work with IO-Link devices, then I suggest you check out our course IO-Link Essentials: Accelerating Towards Industry 4.0.
This course was developed in partnership with ifm to teach you everything you need to know about working with IO-Link technology including;
- The benefits of IO-Link,
- How to set up, configure, and monitor IO-Link devices and masters,
- How to integrate IO-Link devices into control systems,
- How to integrate IO-Link devices into higher-level software systems
At the end of the course, you will have the practical skills you need to work with IO-Link technology as well as a certificate of completion from ifm to prove that you are knowledgeable about IO-Link technology.
See you inside.